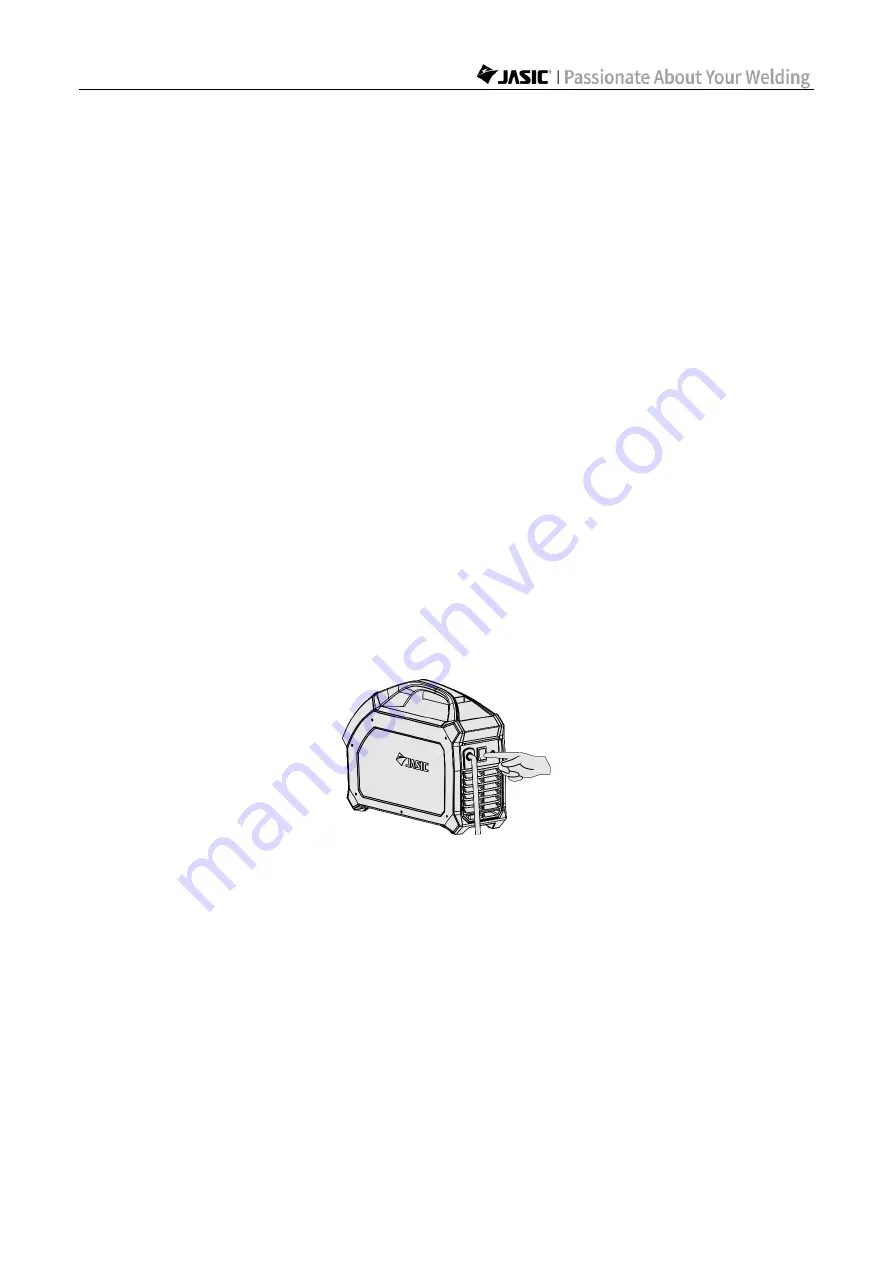
Page 36
welding electrode. For electrodes with sound arc start performance and small diameter,
generally select small hot start current; large welding current also has little requirement for
hot start current.
NOTE!
The operator should set the functions that meet the welding requirements
.
If
the selections are incorrect this may lead to problems such as an unstable arc, spatter,
or sticking of the welding electrode to the workpiece.
During DC welding the heat on the positive and negative polarities of the welding arc is
different. When welding using DC power supply, there are DCEN and DCEP connections.
The DCEN connection refers to the welding electrode connected to the negative polarity of
the power supply and the workpiece connected to the positive polarity of the power supply. In
this mode the workpiece receives more heat, resulting in high temperature, deep penetration,
easy to weld through, suitable for welding thick parts. The DCEP connection refers to the
welding electrode connected to the positive polarity of the power supply and the workpiece
connected to the negative polarity of the power supply. In this mode the workpiece receives
less heat, resulting in low temperature, shallow pool, and less penetration. This is suitable for
welding thin parts.
NOTE!
This product has anti-stick function by default. When VRD is enabled, if short
circuit occurs for 2 seconds during the welding process, the machine will
automatically enter anti-stick function and the welding current will automatically drop
to 10A; when VRD is disabled, if short circuit occurs for 2 seconds during the welding
process, the machine will automatically enter anti-stick function and the output
current will be 0.
7.1.3 Turn off the power supply after welding
Figure 7-3 Power switch position
The power switch is located on the rear panel of the machine and set it to the "off" position.
After a time delay, the panel indicator is off and the welder stops working.
Summary of Contents for TIG200
Page 53: ...Page 53 Appendix 3 List of common spare parts...
Page 56: ...Page 56...
Page 59: ...Page 59...