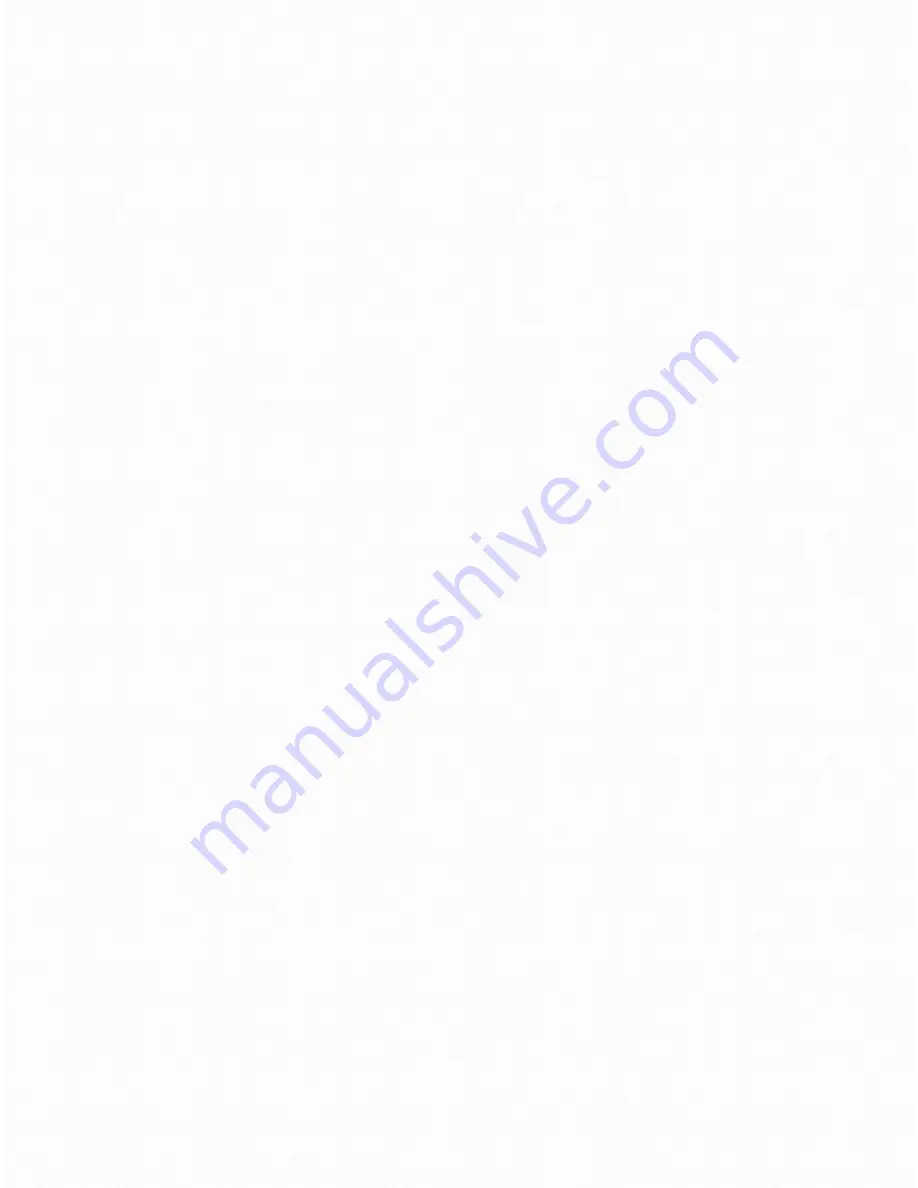
①
During welding, users always enter into operation mode control after the torch trigger is pushed and arc is successfully
ignited, so users do not need to care about the arc ignition requirements of welding in the code design.
②
Operation mode control will be exited once arc stops. If users want to enter into it again, arc should be ignited for another
time.
③
Operation codes "1X" and "2X" are with a rapid response, while "3X", "4X" and "5X" are with a slow response, because it
takes about 0.5s for the latter to collect the e
ff
ective changes of torch trigger.
④
Except C0, select “0” in any other codes means no operation and not turning to the next step (i.e. waiting).
⑤
Since as many as 100 kinds of operation codes are available for this machine, there is more than one code sequence to
achieve the specific operation function, and users only need to choose one of them.
⑥
It should be stressed that not all the programming codes can be combined arbitrarily. Some code combinations do not
make sense, and some can achieve some specific functions but against users’ habit. Therefore, users should pay attention
when obtaining code combinations.
20 kinds of TIG operation modes are available for this machine, in which 0-15 are non-programmable, and 16-19 are
programmable. Whether non-programmable ones or programmable ones, they are achieved by their own operation mode code
sequences, which are obtained based on “Operation mode encoding rules” (see Attached Table 1). Please refer to the
description of the operation modes in the text when reading this table.
32
Summary of Contents for TIG 200 AC/DC Digital Series
Page 26: ...Electrical schematic 7 25...
Page 27: ...Parts list 8 JT 200D 26...
Page 29: ...JT 315D 28...