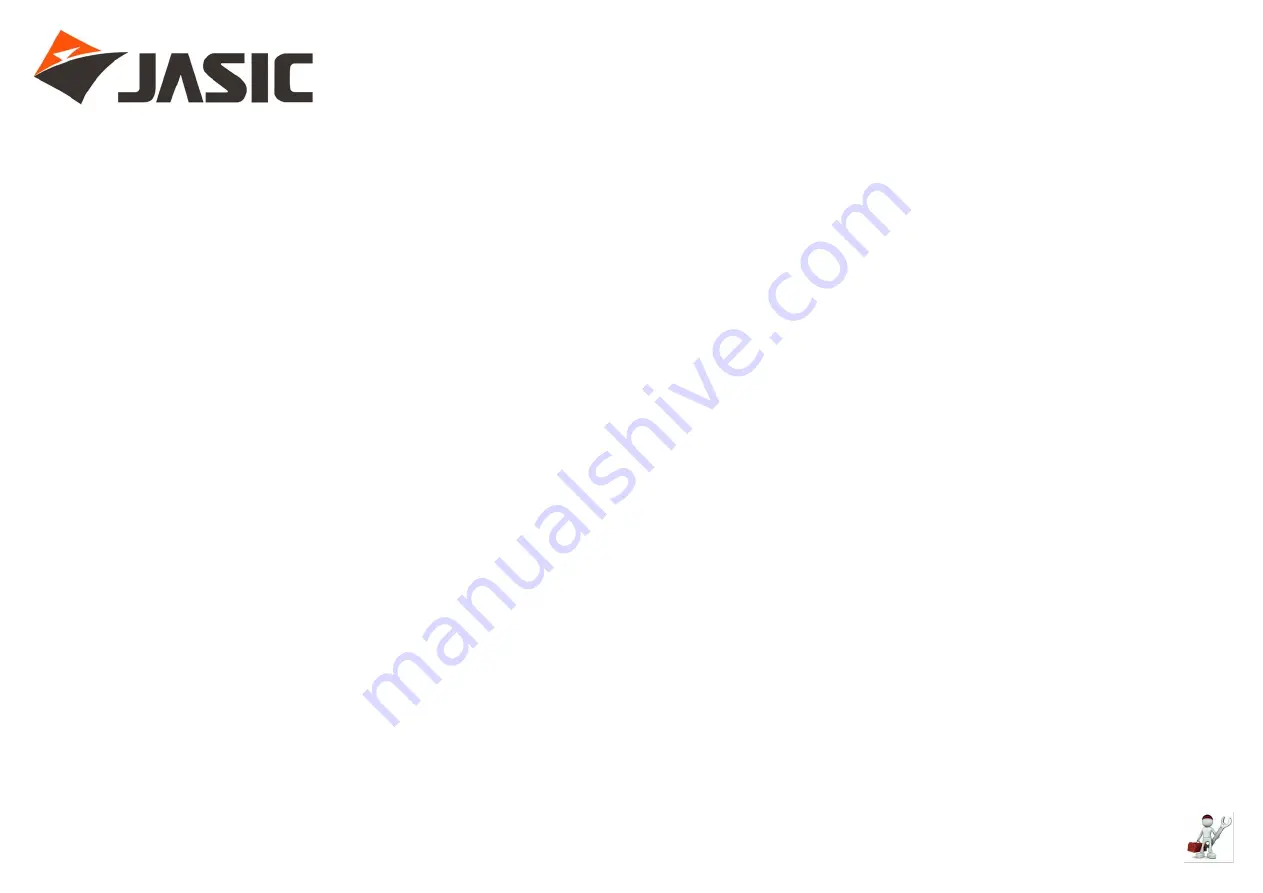
13
Piercing
Piercing is the process in which a quick hole is made in the workpiece. Piercing is often just a starting hole that will be used to make a
circular cut within the workpiece.
You can use standard cutting tips for piercing although ensure the plasma machines output amperage matches the cutting tips amperage
rating. No accessories are required when piercing.
The thickness of the material to be pierced will need to fall in the proper amperage range for the machine and tip you will be using.
There are two different techniques for piercing depending on the thickness of the workpiece. If the work piece is less than 2mm sheet metal,
the torch should be held at a 15°
-
30° angle with the cutting tip touching the workpiece.
Begin by establishing the pilot arc, as soon as the pilot arc penetrates the workpiece, use a smooth, rolling motion to move the torch to a 90°
(perpendicular) angle. At this point, the pierce has been created in the workpiece allowing you to begin the cutting process. If the material
being cut is thicker than 2mm the torch should be held at a 90° (perpendicular) angle approximately 12mm or more above the workpiece.
Begin by establishing the pilot arc and slowly move the torch towards the workpiece until the cutting arc transfers.
Once the transfer has occurred, hold the torch still until the arc exits the bottom of the workpiece.
Once the pierce has been made, the torch can be lowered to normal cutting height and the cutting process can begin.
Bevelling
Bevelling allows you to angle the edge of a flat plate or pipe to allow for deeper weld penetration.
This process is normally used for materials that are 9mm or thicker. You can utilize standard cutting tips for bevelling, again you need to
ensure you utilize the correct plasma machine amperage to match the cutting tips used.
Ensure that the thickness of the material to be bevelled falls in the amperage range of the plasma machine and cutting tip that you will be
using. If bevelling by hand, a roller and/or angle guide can be helpful in maintaining the consistent bevel face and the desired angle which is
usually determined by the weld joint design.
The industry standard angle ranges are from 15°
-
45°. The cutting tip would normally be between
3
–
6
mm from the workpiece.
Plasma Cutting Techniques
Wilkinson Star Technical