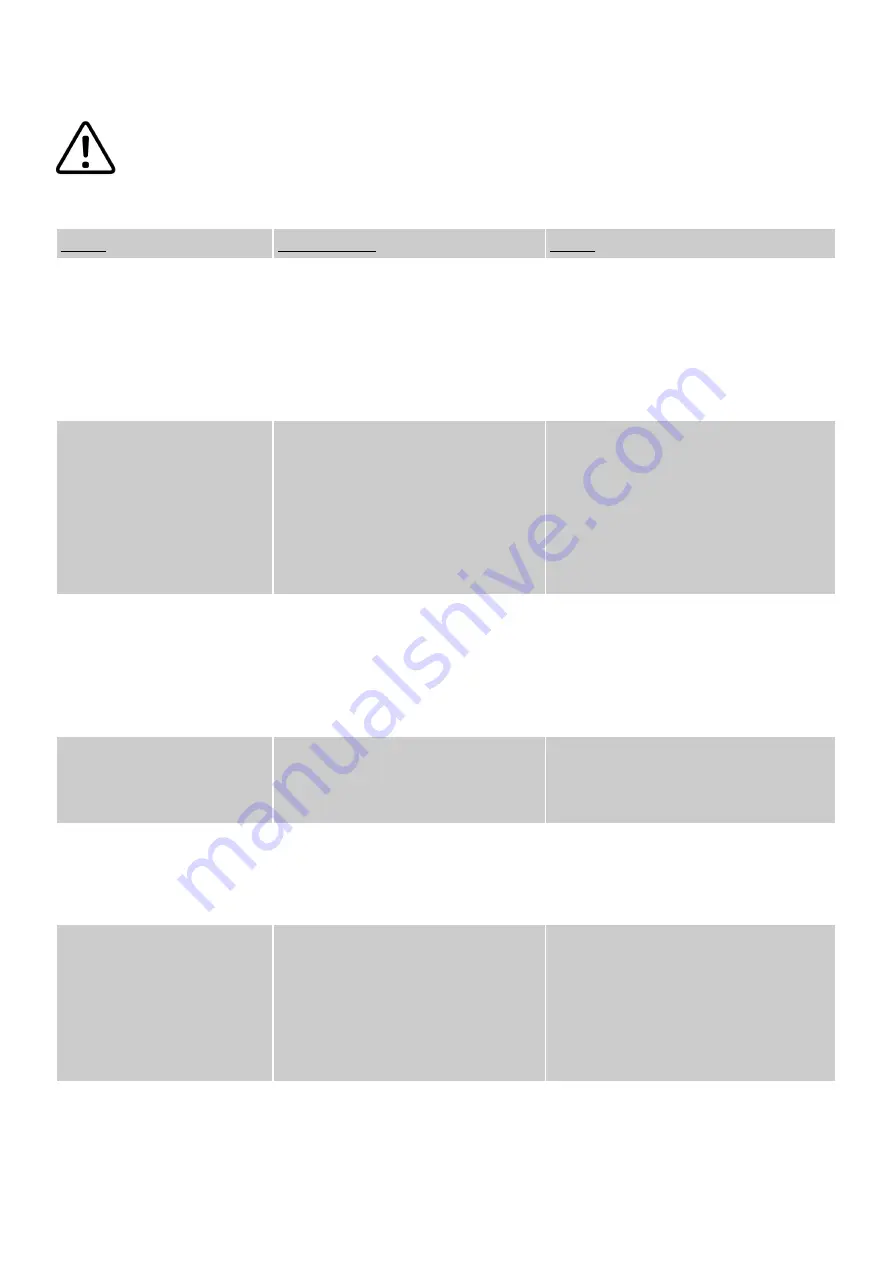
39
TIG WELDING PROBLEMS
Before starting any welding activity ensure that you have suitable eye protection and
protective clothing. Also take the necessary steps to protect any persons within the welding
area.
TIG welding defects and prevention methods
Defect
Possible cause
Action
Excessive tungsten use
Set up for DCEP
Change to DCEN
Insufficient shield gas flow
Check for gas restriction and correct flow
rates. Check for drafts in the weld area
Electrode size too small
Select correct size
Electrode contamination during
cooling time
Extend post flow gas time
Porosity/weld contamination
Loose torch or hose fitting
Check and tighten all fittings
Inadequate shield gas flow
Adjust flow rate - normally 8-12L/m
Incorrect shield gas
Use correct shield gas
Gas hose damaged
Check and repair any damaged hoses
Base material contaminated
Clean material properly
Incorrect filler material
Check correct filler wire for grade of use
No operation when torch
switch is operated
Torch switch or cable faulty
Check the torch switch continuity and
repair or replace as required
ON/OFF switch turned off
Check position of ON/OFF switch
Mains fuses blown
Check fuses and replace as required
Fault inside the machine
Call for a repair technician
Low output current
Loose or defective work clamp
Tighten/replace clamp
Loose cable plug
Check and tighten all plugs
Power source faulty
Call a repair technician
Will not strike an arc
Weld/power cable open circuit
Check all cables and connections for
continuity, especially the torch cables
No shield gas flowing
Check cylinder contents, regulator and
valves, also check the power source
Unstable arc when welding in
DC
Tungsten contaminated
Break off contaminated end and regrind
the tungsten
Arc length incorrect
Arc length should be between 3-6mm
Material contaminated
Clean all base and filler material
Electrode connected to the wrong
polarity
Reconnect to correct polarity
Arc is difficult to start
Incorrect tungsten type
Check and fit correct tungsten
Incorrect shield gas
Use argon shield gas