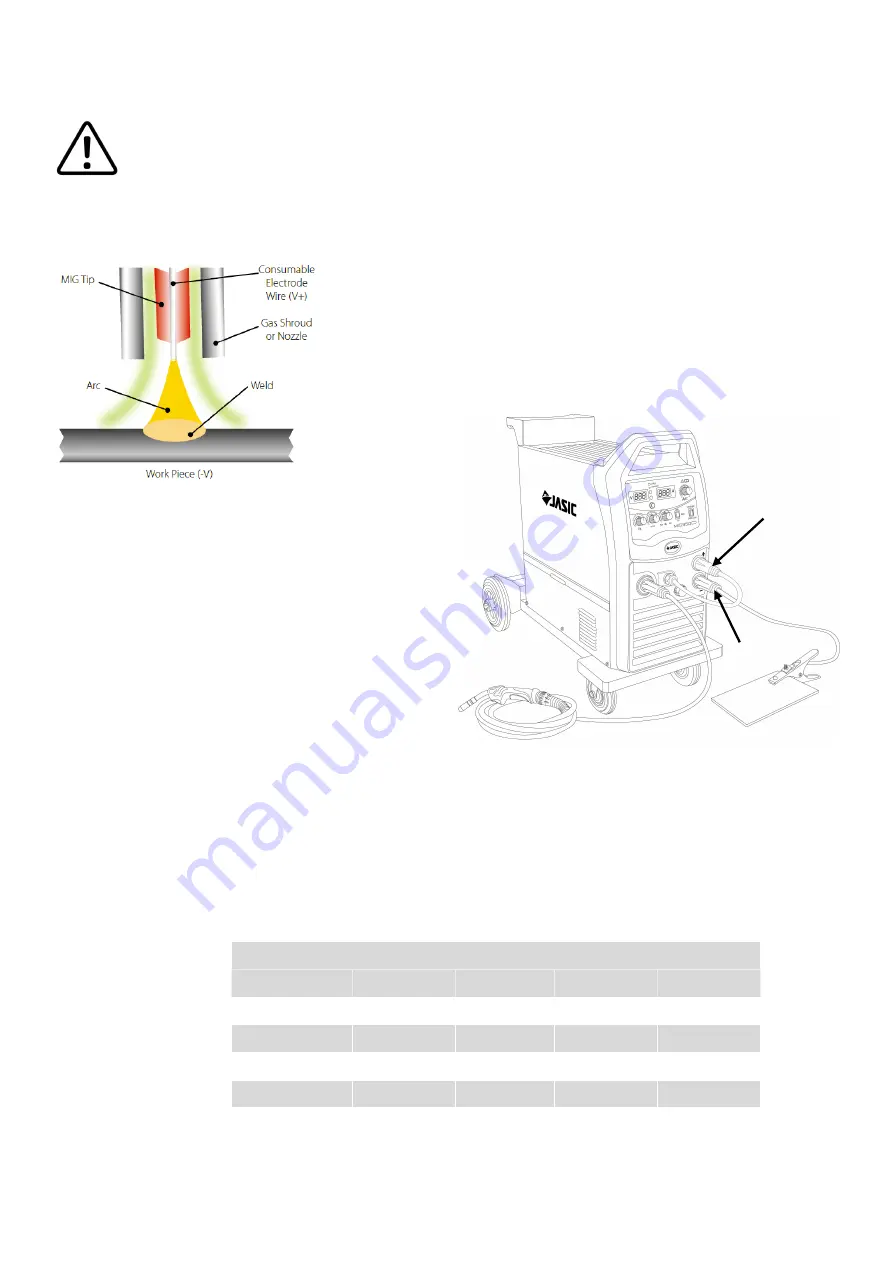
17
OPERATION - MIG
Before starting any welding activity ensure that you have suitable eye protection and
protective clothing. Also take the necessary steps to protect any persons within the welding
area.
MIG/MAG welding mode
MIG - Metal Inert Gas Welding, MAG - Metal Active Gas Welding, GMAW - Gas Metal Arc Welding
MIG welding was developed to help meet production demands of the
war and post war economy which is an arc welding process in which a
continuous solid wire electrode is fed through a MIG welding gun and
into the weld pool, joining the two base materials together.
A shielding gas is also sent through the MIG welding gun and protects
the weld pool from contamination which also enhances the arc.
Connect the MIG torch leads as detailed on page 15.
Work return lead to ‘-’ (B) and torch trailing lead to
‘+’ (A).
Ensure that a suitable inert gas supply is connected.
Switch the power switch on the back panel to “ON”
the machine is started with the power LED on and the
fans are running.
Switch the MMA/MIG switch to MIG mode (ensuring
the standard/spool gun switch is set to standard).
Open the gas valve of the cylinder and adjust the gas
regulator to obtain the desired flow rate.
Adjust the “voltage control knob in MIG” and “wire feed speed control knob in MIG” on the front panel of
the machine to get the correct welding voltage and welding current. Operate the torch trigger and
welding can be carried out.
Where required adjust the burn-back time potentiometer (above the feed unit inside the machine) to get
the proper wire stick-out. One second after the arc stops, the gas supply will be cut off.
The MIG wire guide below can vary depending on material used, work piece thickness, welding position
and joint form.
MIG - Gasless
The operation method is the same as the above MIG operation except there no shielding gas is used and
the output polarity is reversed (see page 15).
Wire Diameter
DIP Transfer
Spray Transfer
(mm)
Current (A)
Voltage (V)
Current (A)
Voltage (V)
0.6
30 ~ 80
15 ~ 18
n/a
n/a
0.8
45 ~ 180
16 ~ 21
150 ~ 250
25 ~ 33
1.0
70 ~ 180
17 ~ 22
230 ~ 300
26 ~ 35
1.2
60 ~ 200
17 ~ 22
250 ~ 400
27 ~ 35
1.6
100 ~ 280
18 ~ 22
250 ~ 500
30 ~ 40
A
B
Model shown as example is the JM-352C