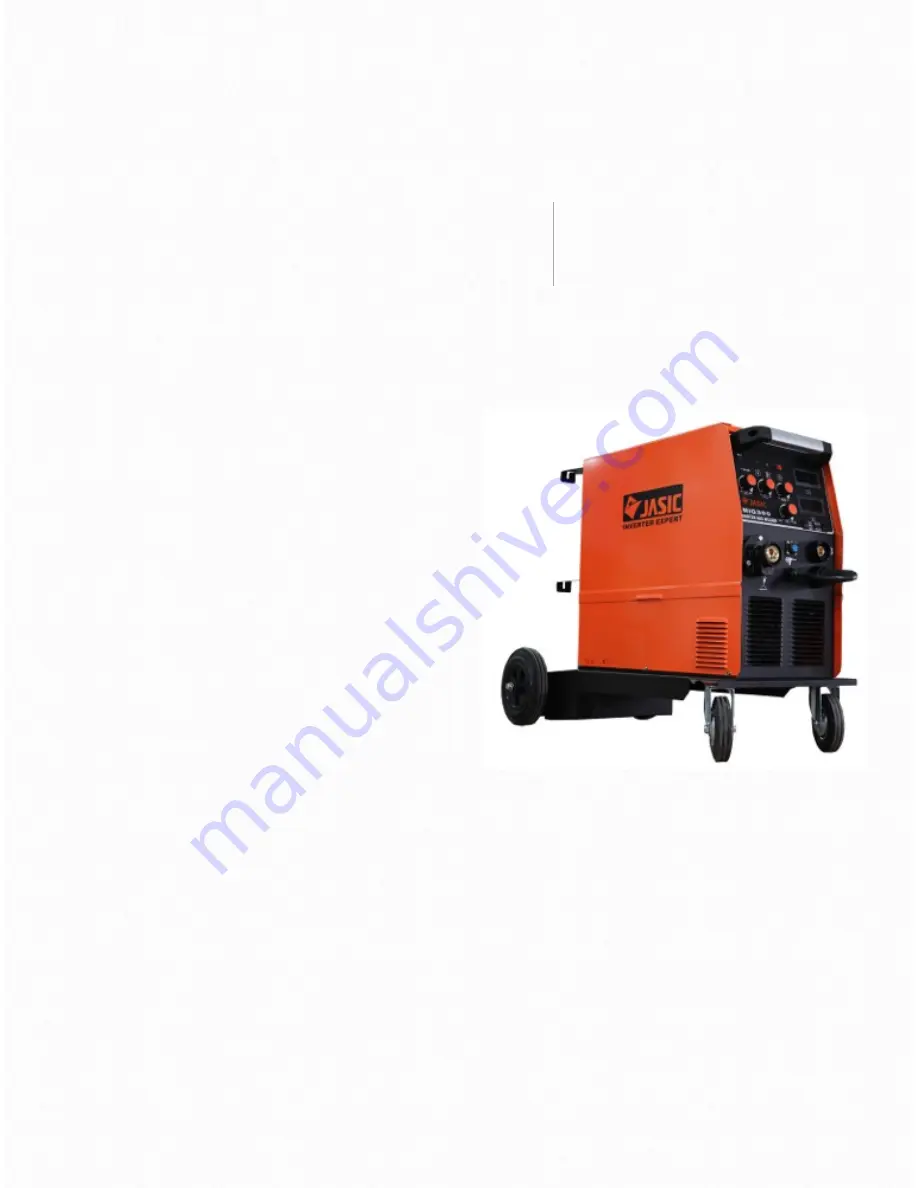
Product Overview
2
The MIG 250 is an inverter power source that can provide
MIG, MMA and gas less self- shielded welding welding
options.
Its IGBT power device with unique control mode provides
excellent reliability with a high duty cycle.
The system has a closed loop feedback control, constant
voltage output, which allows it to operate with a wide
tolerance to mains fluctuation, within ±15%.
It has continuously adjustable welding voltage and current,
to provide excellent welding characteristics.
Adopting a unique welding dynamic characteristic control
circuit in MIG, provides a stable arc, low spatter, excellent
weld appearance and high welding e
ffi
ciency.
By removing the ball at the end of the wire after welding, a
high no-load voltage, and slow wire feed at the start
presents exceptional arc starting.
The machine also has a very stable welding current in MMA,
excellent arc ignition, and can be used with a wide variety of
welding electrodes.
Its high inverter frequency greatly reduces the volume and
weight of the welder and the great reduction in magnetic
and resistance loss obviously enhances the welding
e
ffi
ciency and energy saving e
ff
ect.
Switching frequency is beyond audio range, which almost
eliminates noise pollution.
5
Summary of Contents for JM-350C
Page 16: ...Electrical schematic 7 15 VDC ...