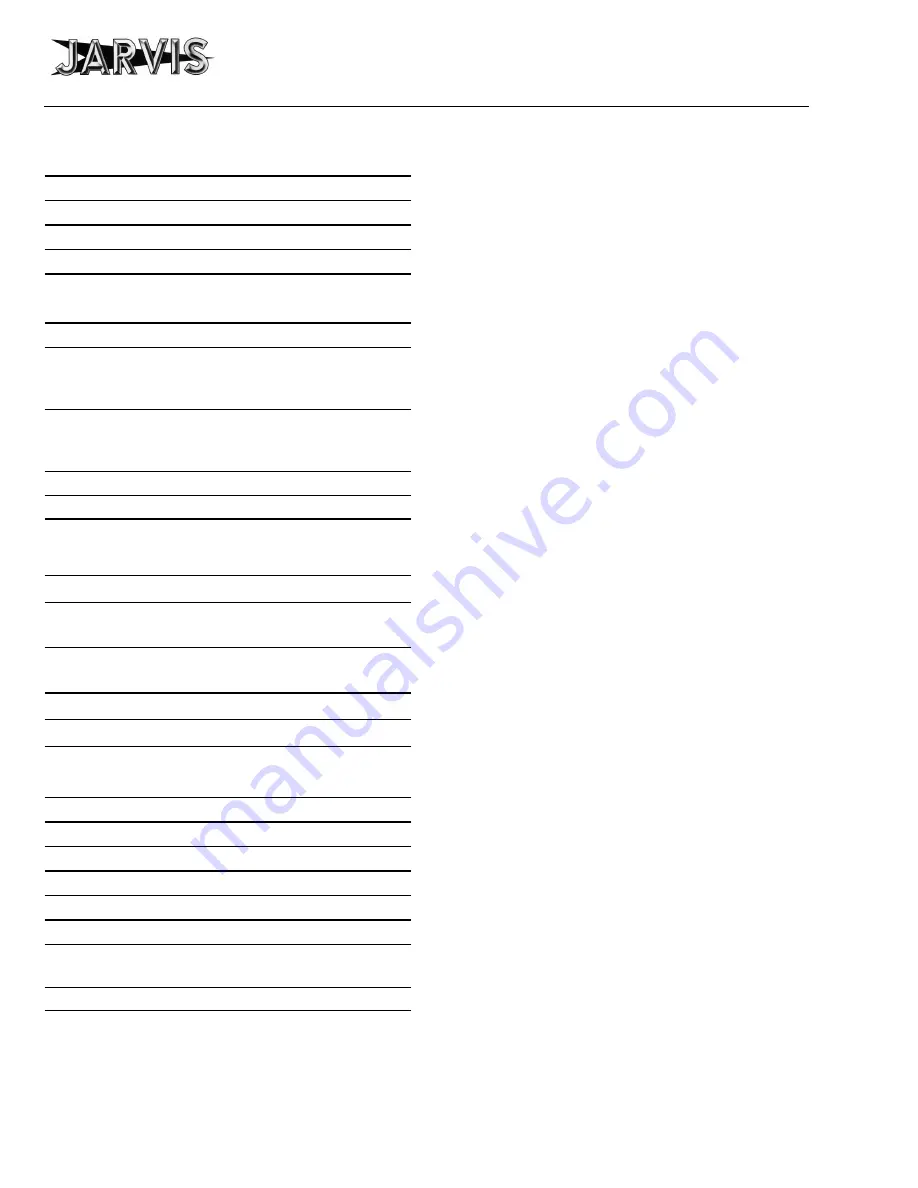
specifications and
installation instructions
Model SHC 140, 165, 165B, 165G, 165GT and 205
page 14 of 20
PRODUCTS CORPORATION
33 ANDERSON ROAD, MIDDLETOWN, CONNECTICUT 06457-4926
UNITED STATES OF AMERICA E--MAIL.
TEL. 860-347-7271
FAX. 860-347-6978
WWW.
jarvisproducts.com
JARVIS
6207016::::.
SPECIFICATIONS
All Models
Motor Power
2.5 hp
1865 W
Blade Speed at 3.5 gal/min
2725 rpm
Vibration
less than (<) 100 dB
< 0.1 m/sec
2
Noise (one meter from tool)
87 dB
Model SHC 140, 165 and 205
Control Handle
Single trigger / Pneumatic
Blade Diameter
8.1 in
205 mm
6.5 in
165 mm
5.5 in
140 mm
Cutting Depth
2.8 in
71.0 mm
2.0 in
50.8 mm
1.5 in
38.1 mm
Overall Length
16.5 in
419 mm
Weight
7 lbs
3.2 kg
Model SHC 165G and 165GT
Control Handle
Dual Anti--Tie Down / Pneumatic
Cutter Head Width Pork
0.51 in
13 mm
Beef
0.63 in
16 mm
Cutting Depth
Pork
0.81 in
20.6 mm
Beef
0.88 in
22.4 mm
Overall Length
15 in
381 mm
Weight
8.6 lbs
3.9 kg
Hydraulic Power Unit
Motor Power
5 hp
3728 W
Operating Voltage all voltages and 50 Hz. available
Hose Length
16 ft
5 m
Oil Capacity
20 gal
76 L
Oil Visc. at 100
°
F/40
°
C
200 SUS
46 ISO
Oil Flow Rate
3.5 gal/min
13.2 L/min
Overall Dimensions (l x w x h)
28 x 23 x 28 in
711 x 584 x 711 mm
Weight (without oil)
225 lbs
102 kg
INSTALLATION INSTRUCTIONS
ALWAYS DISCONNECT THE POWER SUPPLY IN
ACCORDANCE WITH OSHA’S LOCKOUT/TAGOUT
PROCEDURES (29 CFR 1910.147) BEFORE PERFORM-
ING ANY REPAIRS OR MAINTENANCE.
ALL WIRING MUST BE DONE IN ACCORDANCE WITH
NATIONAL, STATE AND LOCAL ELECTRICAL CODES.
Refer to Figure 1 or 2 on page 12 or 13 as a guide for con-
necting the air and hydraulic hoses.
1 Install the SHC saw above the work station from a
balancer.
Jarvis
part number 4042033 or 4042044
is available.
1.1 The SHC saw should have enough travel to al-
low the operator to reach the entire work area.
2 Install the hydraulic power unit overhead or on the
floor behind the work station.
2.1 Avoid excessive height and long pipe runs.
3 Wire the power unit. Refer to the wiring diagram la-
bel inside the control box cover (item 37, Figure J,
page 11) for the correct operating voltage and fre-
quency.
4 Equip the power unit with a master pilot light switch
at the operators station.
This will facilitate shut-
down in case of an equipment failure.
5 Fill the oil reservoir with a USDA approved pre-
mium grade hydraulic fluid (viscosity: 200 SUS at
100
°
F / 46 ISO at 40
°
C).
6 Make all necessary air hose connections.
Single Trigger Tools: Refer to Figure J, page 11.
6.1 For the air supply line: use tube to tube connec-
tor (item 12) to connect blue plastic tubing (item
11) from air filter / regulator (item 15) to blue
plastic tubing (item 189, Figure G, page 8) from
the port marked “IN” on hydraulic manifold
(item 187, Figure G, page 8 or item 65, Figure
B, page 5).
6.2 For the air return line: use tube to tube connector
(item 12) to connect yellow plastic tubing (item
19) from tube connector (item 10) to yellow
plastic tubing (item 123, Figure F, page 7) from
the port marked “OUT” on hydraulic manifold
(item 187, Figure G, page 8 or item 65, Figure
B, page 5).