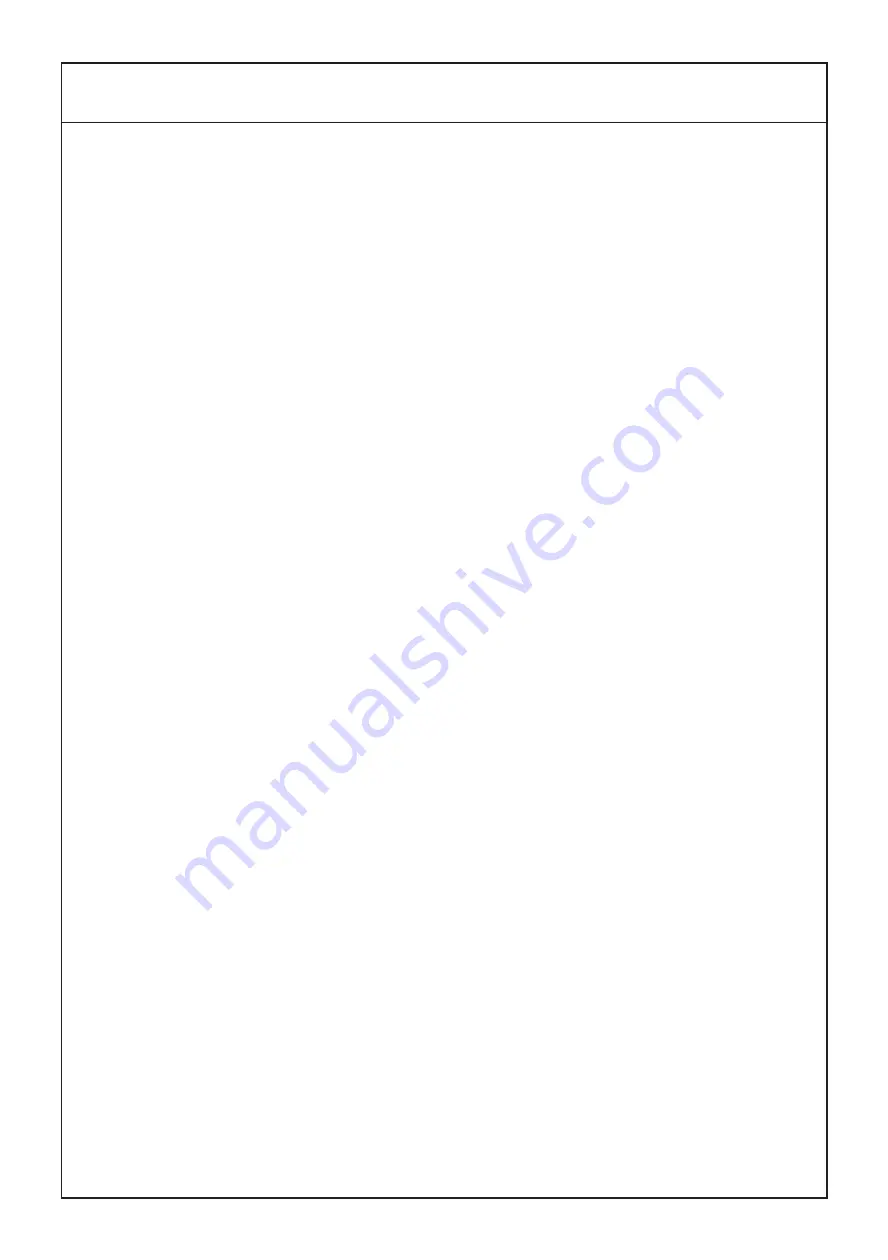
5b
HEIGHT AND ORIENTATION OF NEEDLE BAR IN RELATION
TO THE NEEDLE PLATE HOLES
20
1. Remove: Mains lead - Sewing foot.
2. Insert a new needle (No.90) in "R1".
3. With needle bar at its highest position, loosen screws "a" just enough so that
needle bar slides with friction.(Fig.1)
4. Place gauge on needle plate and adjust height of needle bar so that needle "R1"
grazes the gauge.(Fig.2)
5. For the orientation of needle bar or needle holder, insert new needles in "L0 , L1
and L2", orientate needle bar so that the needles are centered in the needle plate
holes. Make sure that neither needle "L0 , L1 nor L2" is touching the inside of the
needle plate holes. Tighten screw "a" and recheck the height.(Fig.3)
6. Remove needle plate and check the clearance between the chain and lower looper
and needle(s). If necessary, adjust clearance of chain looper (see page 11) and
clearnace of lower looper (see page 6).
Summary of Contents for 1200D
Page 1: ...PARTS LIST SERVICE MANUAL MODEL 1200D First Edition 21 February 2019 ...
Page 2: ...SERVICE MANUAL ...
Page 8: ...ADJUSTMENT OF THE AUTOMATIC TENSION UNIT D d B B r s 6 s r ...
Page 18: ...3b ANGULAR POSITION OF BALANCE WEIGHTS AND POSITION OF ECCENTRICS 16 ...
Page 19: ... a HEIGHT AND ALIGNMENT OF CLOTH PRESSER BAR 4a 5 b c 4 7mm 17 ...
Page 25: ...TIMING OF LOWER LOOPER 8a A B C D b a 5 2mm R1 Fig 1 Fig 2 Fig 3 23 ...
Page 26: ...TIMING OF LOWER LOOPER 8b 24 ...
Page 32: ...CHAIN LOOPER ANGULAR POSITION CLEARANCE ORBITAL TIMING CLEARANCE OF CHAIN NEEDLES GUARD 11d ...
Page 34: ...Fig 2 Fig 1 R F 2mm L2 c d e c a b Fig 4 Fig 3 ...
Page 35: ......
Page 36: ...R1 A a B d c Fig 2 Fig 4 Fig 3 Fig 1 2mm 0 5 0 5mm 0 5 0 8mm ...
Page 37: ......
Page 38: ......
Page 39: ......
Page 40: ......
Page 41: ......
Page 42: ......
Page 43: ......
Page 44: ......
Page 45: ......
Page 46: ......
Page 47: ...21c ...
Page 48: ......
Page 50: ...ANNEX SETTING POSITIONS OF SL DF DIALS a Fig 1 48 A b a ...
Page 51: ...ANNEX SETTING POSITIONS OF SL DF DIALS b c d g e 2 1 1 C B A 49 ...
Page 52: ...ANNEX SETTIN POSITIONS OF SL DF DIALS c 50 ...
Page 62: ......
Page 63: ...PARTS LIST MODEL 1200D First Edition 28 February 2019 ...
Page 64: ...2 MODEL 1200D PARTS LIST 16 15 14 17 18 19 20 21 22 23 24 25 26 27 28 29 30 31 745 12 13 ...
Page 68: ...6 MODEL 1200D PARTS LIST 1 2 3 4 5 6 7 8 9 10 11 12 13 14 15 16 17 17 18 19 19 ...
Page 76: ...14 MODEL 1200D PARTS LIST 1 2 3 4 5 6 6 6 6 9 4 7 8 4 10 10 10 4 4 4 10 4 4 ...
Page 82: ...20 MODEL 1200D PARTS LIST ...
Page 84: ...22 MODEL 1200D PARTS LIST ...
Page 86: ...24 MODEL 1200D PARTS LIST ...