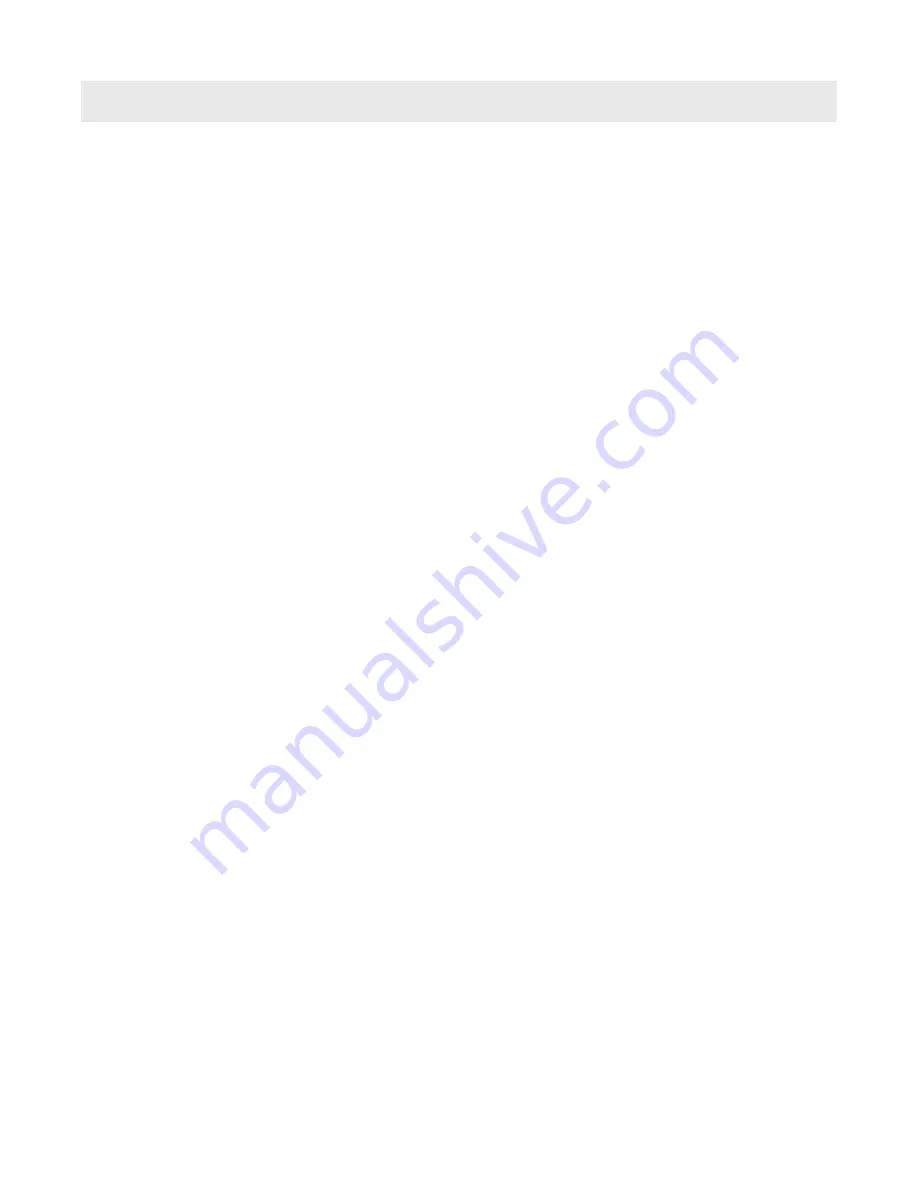
important
safety
instructions
4
c) Prevent unintentional starting. Ensure the switch is in the “OFF” position before connecting to power source
and/or battery pack, picking up or carrying the tool.
Carrying power tools with your finger on the switch or
energizing power tools that have the switch on invites accidents.
d) Remove any adjusting key or wrench before turning the power tool on.
A wrench or key left attached to
a rotating part of the power tool may result in personal injury.
e) Do not overreach. Keep proper footing and balance at all times.
This enables better control of the power
tool in unexpected situations.
f) Dress properly. Do not wear loose clothing or jewelry. Keep your hair, clothing and gloves away from
moving parts.
Loose clothes, jewelry or long hair can be caught in moving parts.
g) If devices are provided for the connection of dust extraction and collection facilities, ensure these are
connected and properly used.
Use of dust collection can reduce dust-related hazards.
4. Power tool use and care
a) Do not force the power tool. Use the correct power tool for your application.
The correct power tool will
do the job better and safer at the rate for which it was designed.
b) Do not use the power tool if the switch does not turn it on and off.
Any power tool that cannot be controlled
with the switch is dangerous and must be repaired.
c) Disconnect the plug from the power source and/or the battery pack from the power tool before making any
adjustments, changing accessories or storing power tools.
Such preventative safety measures reduce the
risk of starting the power tool accidentally.
d) Store idle power tools out of the reach of children and do not allow persons unfamiliar with the power tool
or these instructions to operate power tool.
Power tools are dangerous in the hands of untrained users.
e) Maintain power tools. Check for misalignment or binding of moving parts, breakage of parts and any other
condition that may affect the power tool’s operation. If damaged, have the power tool repaired before use.
Many accidents are caused by poorly maintained power tools.
f) Keep cutting tools sharp and clean.
Properly maintained cutting tools with sharp cutting edges are less
likely to bind and are easier to control.
g) Use the power tool, accessories and tools etc. in accordance with these instructions, taking into account
the working conditions and the work to be performed.
Use of the power tool for operations different from
those intended could result in a hazardous situation.
h) Check for damaged parts.
Before further use of the tool, a guard or other part that is damaged should be
carefully checked to determine that it will operate properly and perform its intended function. Check alignment
of moving parts, binding of parts, breakage of parts, mounting and any other conditions that may affect its
operation. A guard or other part that is damaged should be properly repaired or replaced by an authorized
service center.
5. Service
a) Have your power tool serviced by a qualified repair person using only identical replacement parts.
This
will ensure that the safety of the power tool is maintained.