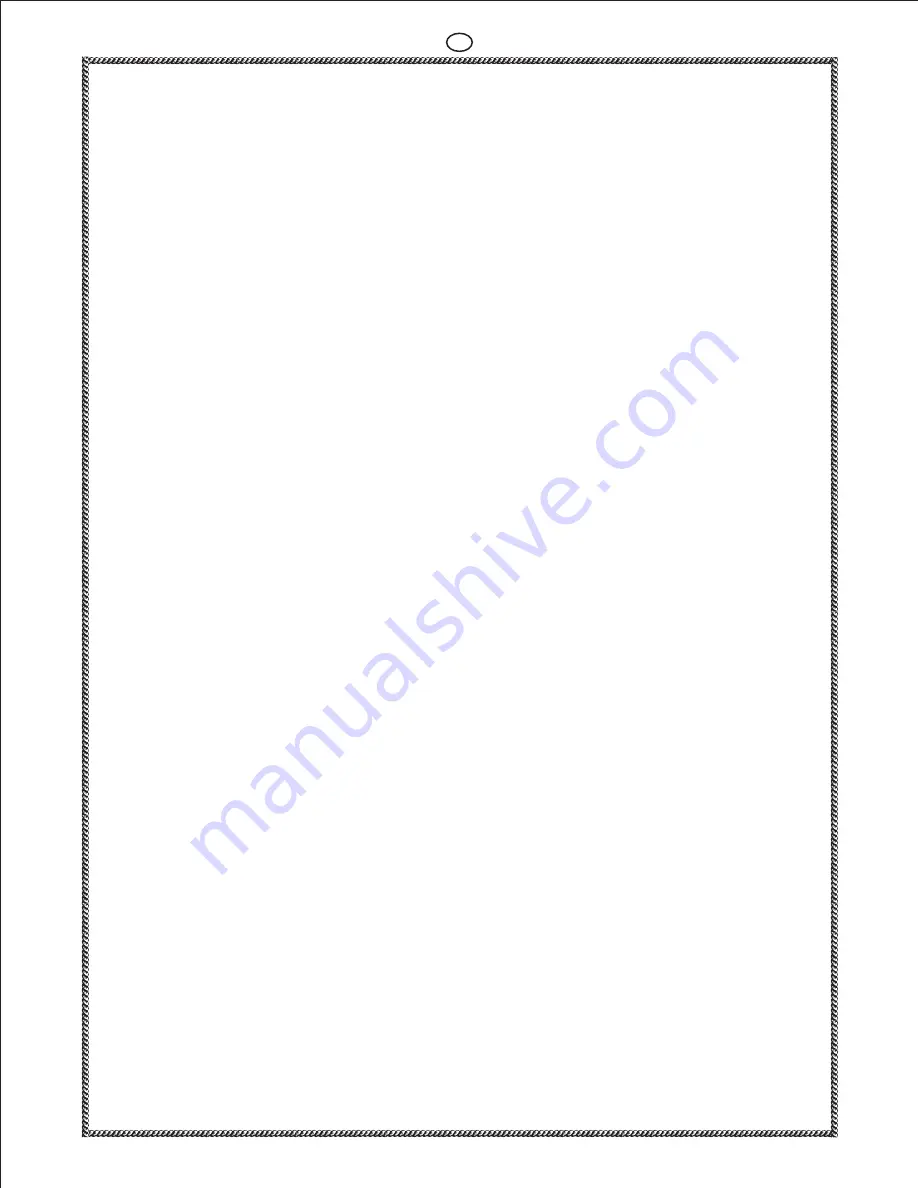
28
JAKSON & CO.
REVALIDATION POLICY FOR GENSET
Revalidation Eligibility:
1. Genset revalidation is applicable for Gensets which are not in operation for 6 months or beyond from the date of GOEM invoice.
2. Revalidation activity will be carried out on Genset at customer’s end before commissioning / PRF.
3. The revalidation activity is to be solely owned taken care by GOEMs / KGDs. KOEL and their authorized Service Dealers will not be liable for any kind of communication
with end customer regarding revalidation activity.
4. Revalidated Engine / Genset should be commissioned along with completion of PRF within 1 month from the date of revalidation else warranty benefits will not be
applicable.
Revalidation Execution Process:
A.
For revalidation GOEM /KGD / Customer has to approach nearest Service Dealer / KOEL Helpdesk along with Engine / Genset details.
B.
Service Dealer will attend the engine revalidation on chargeable basis as recommended in Annexure H.
C.
After revalidation activity Service Dealer will issue revalidation certificate for said Genset to End Customer and subsequently complete the request process in Pulse.
D.
Ownership transfer / PRF (End customer name) to be carried out by GOEM /KGD in Pulse after completion of revalidation and commissioning.
Note: Incase Genset is started and used without following the revalidation process / PRF process,
the warranty will be null and void.
Annexure E (At Customer End)
Revalidation Situations –
There are four situations as E1, E2, E3 and E4.
Situation E1
Genset revalidation is required where Genset not commissioned at customer’s end more than 6 months and below 12 months from date of GOEM Invoice.
Following check points to be carried out for situation E1
1. Check contamination in lube oil, if found contaminated replace Lube Oil. Check fuel tank & Filters. If found that filters are damaged or can’t be used then only go for
replacement otherwise not.
2. Check conditions of V Belts, all Hoses, Air filter, Fuel pipes, rubber parts and replace if required.
3. Check turbocharger free rotation and for water, dirt, foreign particles ingress in Intake / Exhaust system, initiate corrective action accordingly.
4. For HE cooled engines, check heat exchanger & CAC for raw water entry, also check for cooling tower basin cleanness and control valve function.
5. Check electrical parts for physical condition, wiring connections, intactness and functionality. Same check may please be carried out for Alternator by opening a
terminal box.
6. Check monitoring and safety devices for functionality.
7. Check FIP rack freeness and rectify as per manufacturer’s guidelines.
8. Electrical system -Check Main Alternator winding insulation by 500 volt megger. Insulation Resistance of the winding and earth should be greater than 2 Mega Ohm.
If Resistance is less than this value, in case of deviation rectify through authorised Service Centre.
9. Start Genset and check its performance as per test cycle and in case of abnormality rectify as per standard operating practices.
Situation E2
Genset revalidation is required where engine/ Genset not commissioned beyond 12 months and below 18 month from date of GOEM Invoice.
In addition to the above checks (carried out in Section –E 1), following additional checks to be carried out -:
·
Oil and filter change are mandatory.
·
Air Intake / Exhaust system –Open cylinder heads, check the condition of liner & piston top for rust formation, any damage, scratch marks, foreign material entry or
any abnormality and initiate the corrective action accordingly. Air filter, rubber hoses and belts, can be checked and to be replaced if needed.
·
Check the turbocharger rotational freeness, axial and radial play of turbocharger. If turbocharger found jam, get it rectified from authorized turbocharger Dealer.
In addition to the above also check oil supply and return lines of turbocharger.
Lube Oil System –Drain engine oil, remove oil sump, check main & connecting rod bearings, crank shaft for rust formation etc. Refill the fresh engine oil after
thorough inspection of above.
·
Fuel Injection System -Remove Fuel injection pump & injectors, get them calibrated from authorized service centre. At the time of fitment ensure thorough checking
and replacement of relevant fuel injection system accessories.
·
Cooling System -Check & clean the radiator fins for accumulation of dust and foreign particles. Check Water pump freeness, replace if necessary. In case of HE cooled
engine change the raw water in cooling tower basin, also check the raw water pumps, valve for operation. In case of air cooled engine, remove air baffle, check for
dust and foreign particles in fins. Blow compressed air from exhaust outlet side.
·
Electrical System - Check Main Alternator and Engine Electricals as per process mentioned in situation E 1.
·
Genset to be tested at least for 90 minutes on full load.
·
During testing of Genset, check its performance as per test cycle and in case of abnormality rectify as per standard operating practices.
·
Blow By, smoke and other relevant parameters to be checked.
·
If blow by or any other abnormality is there during testing then we should go for the checking of cylinder heads and liners, etc.
·
The replacement of the parts will purely be restricted to the most desired one & the labour cost charged towards revalidation activity must be as per KOEL
recommendation.
Situation E3
Genset revalidation is required where engine/ Genset not commissioned beyond 18 months below 24 month from date of GOEM Invoice.
On GOEM’s request KOEL may consider Revalidation policy & the warranty offer as a very special case with a prior approval of VP –Marketing Sale & Service for Gensets
which are not commissioned at Customer end for more than 18 months and below 24 months from the date of GOEM invoice. The authorised KOEL service dealer will
carry out the necessary repair work on chargeable basis in order to bring Genset into operational condition.
Situation E4
Genset revalidation is required where engine/ Genset not commissioned beyond 24 months from date of GOEM Invoice.
Revalidation policy is not applicable for Gensets which are not commissioned at Customer end for more than 24 months from the date of GOEM invoice. However on
GOEM/ KGD / Customer request, the authorised KOEL service dealer may carry out the necessary repair work on chargeable basis in order to bring Genset into
operational condition.
Annexure F (At Customer End)
Revalidated Genset warranty period
Situation E1
–Genset revalidation is completed at customer’s end where Genset not commissioned more than 6 months and below 12 months from date of GOEM Invoice.
Or
Situation E2
–Genset revalidation is completed at customer’s end where Genset not commissioned more than 12 months and below 18 months from date of GOEM Invoice.
Or
Summary of Contents for JakPower Kirloskar Koel Green 2R1040 G1
Page 1: ......
Page 2: ......
Page 30: ...26 JAKSON CO BY KIRLOSKAR POWER JAKSON COMPANY 550 13 ...
Page 31: ...27 JAKSON CO BY KIRLOSKAR POWER JAKSON COMPANY 550 13 ...
Page 35: ...POWER JAKSON CO ...
Page 36: ......