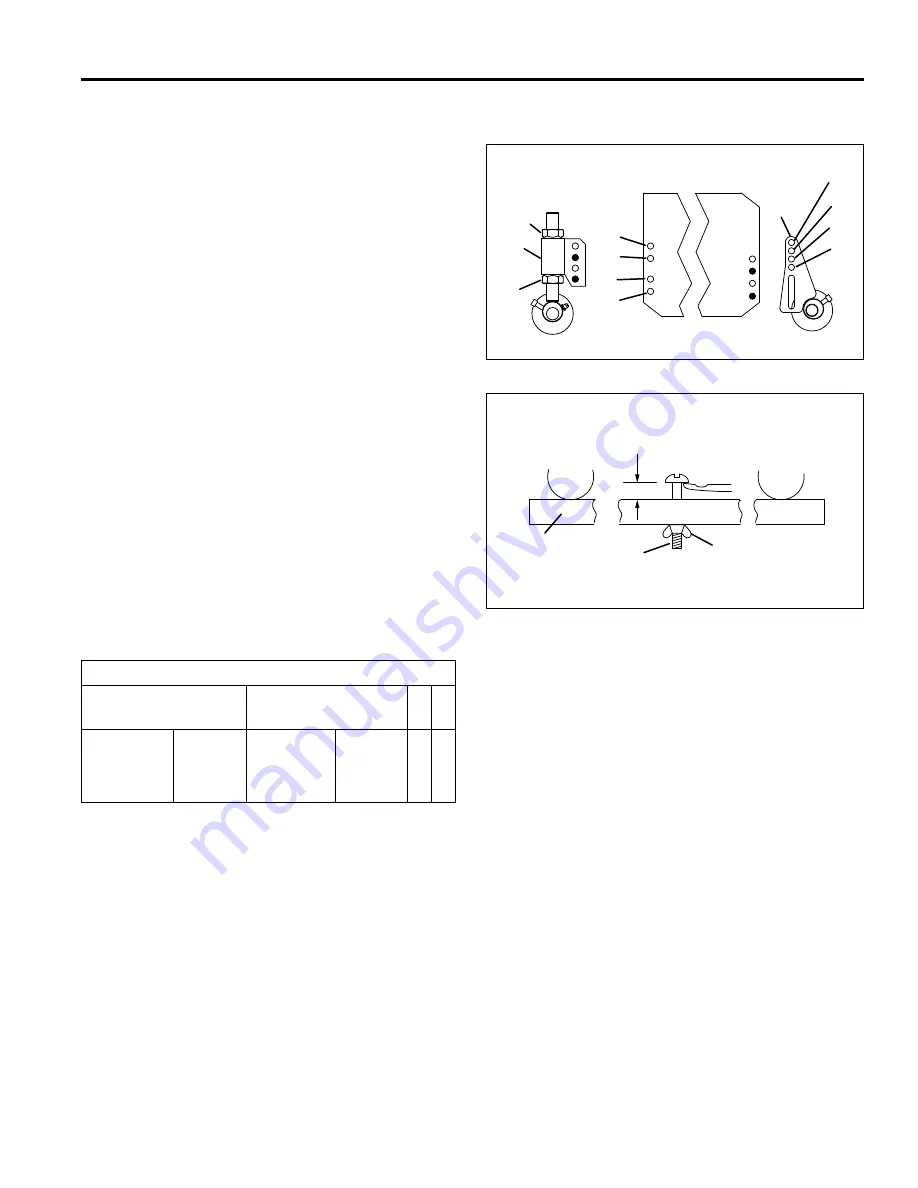
ADJUSTMENTS 5
23
5.19 CUTTING HEIGHT - FLOATING MODE _________________________________________
Follow the procedures outlined in Section 5.16.
1.
Assemble the front roller adjuster (
B
) to holes num-
ber 2 and 4 only of the mower frame. Do not use hole
numbers 1 and 3. Refer to the chart below for correct
hole of front roller adjuster to use.
2.
Reposition the rear roller adjusters (
F
).
a.
For cutting heights from 3/8 to 1-3/4 in. (9 to
44 mm), use holes (
M
) on the mower frame, and
two holes (shown in black) of adjuster (
F
) as
shown.
b.
For cutting heights greater than 1-3/4 in.
(44 mm), disassemble adjuster (
F
) and turn the
mounting bracket upside down; then use holes
(
N
) of the frame, and the two holes (shown in
black) of adjuster (
F
).
3.
Loosen nut (
L
) and adjust screw (
K
) to obtain
desired cutting height (
X
) then lock nut (
L
) against
gauge (
P
).
4.
Place one end of the gauge under the front roller at
either end of the reel, and slide the head of screw
(
K
) over the bedknife.
a.
Adjust nut (
G
) to lower the rear roller to the
gauge, then tighten nut (
E
) against the adjuster.
b.
Move the gauge to the other end of the reel and
repeat Steps 4a and 4b.
Figure 5S
Figure 5T
Range of Cut
Grooved Roller
Inches Millimeters
Solid Roller
Inches Millimeters
Fr
o
n
t
Rea
r
3/8 - 3/4
10 - 19
3/8 - 5/8
10 - 16
R
M
3/4 - 1-1/4
19 - 32
5/8 - 1-1/8
16 - 29
S
M
1-1/4 - 1-3/4
32 - 44
1-1/8 - 1-5/8
29 - 41
T
M
1-3/4 - 2-1/4
44 - 57
1-5/8 - 2-1/8
41 - 54
U
N
1
2
3
4
5
6
7
8
N
M
N
M
U
T
S
R
B
E
F
G
Front Roller
P
Rear Roller
X
-Cutting Height
K
L