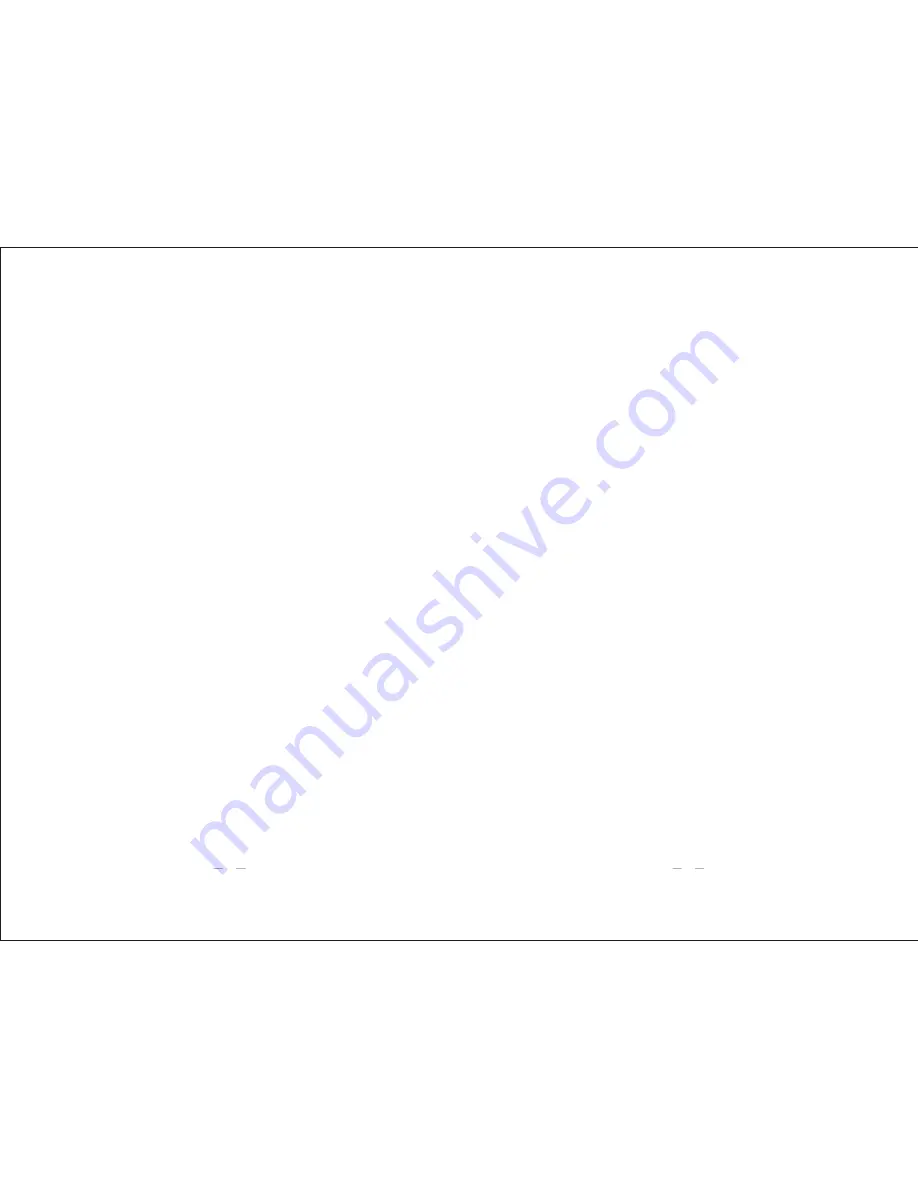
(
-10)
Err
REASON:
Panel no display or panel no power
The way to check:
1.
check if connection between panel and control box is broken or not.
2.
Interchange the panel to check if it is the panel problem.
3.
Interchange the control box to check if it is the control box problem.
Solution:
1.
If connection problem, just need to improve connection.
2.
If panel problem, just change the panel.
3.
If control box problem, change another one or send the defective control box back to
company to repair.
The way to check:
1.
Testing discharge cement resistor is burn out or not;
Solution:
1.
Replace the cement resistor with same model.
2.
Replace the control box or send it back to supplier for repairing.
(Err-09)
REASON:
Discharge circuit fault.
The way to check:
1.
Check if there is any other mechanical fault from machine in running condition.
2.
Recheck motor angle.
3.
Interchange the control box to check control box have problem or not.
Solution:
1.
Make sure there is no any mechanical fault from machine.
2.
Use P43 , change the last digital parameter from 0 to 2 , step on the pedal, recheck the motor
angle , then change the last digital parameter from 2 to 0 and save.
3.
If control box problem, change another one or send the defective control box back to
company to repair.
(
12/13/15)
Err-
REASON:
Motor initial rotor position fault
The way to check:
1.
Check if connection between motor encoder and control box is in good condition or not.
2.
Interchange the encoder to check if it is the encoder problem.
3.
Interchange the control box to check if it is the control box problem.
Solution:
1.
If connection problem, just need to improve connection.
2.
If encode problem, just change the encode.
3.
If control box problem, change another one or send the defective control box back to
company to repair.
(Err-08)
REASON:
Motor blocked
Common fault treatment(4)
Common fault treatment(5)
Common fault treatment(6)
Common fault treatment(7)
18
19
Summary of Contents for JK-SHIRLEYIIE
Page 18: ...MEMO MEMO...