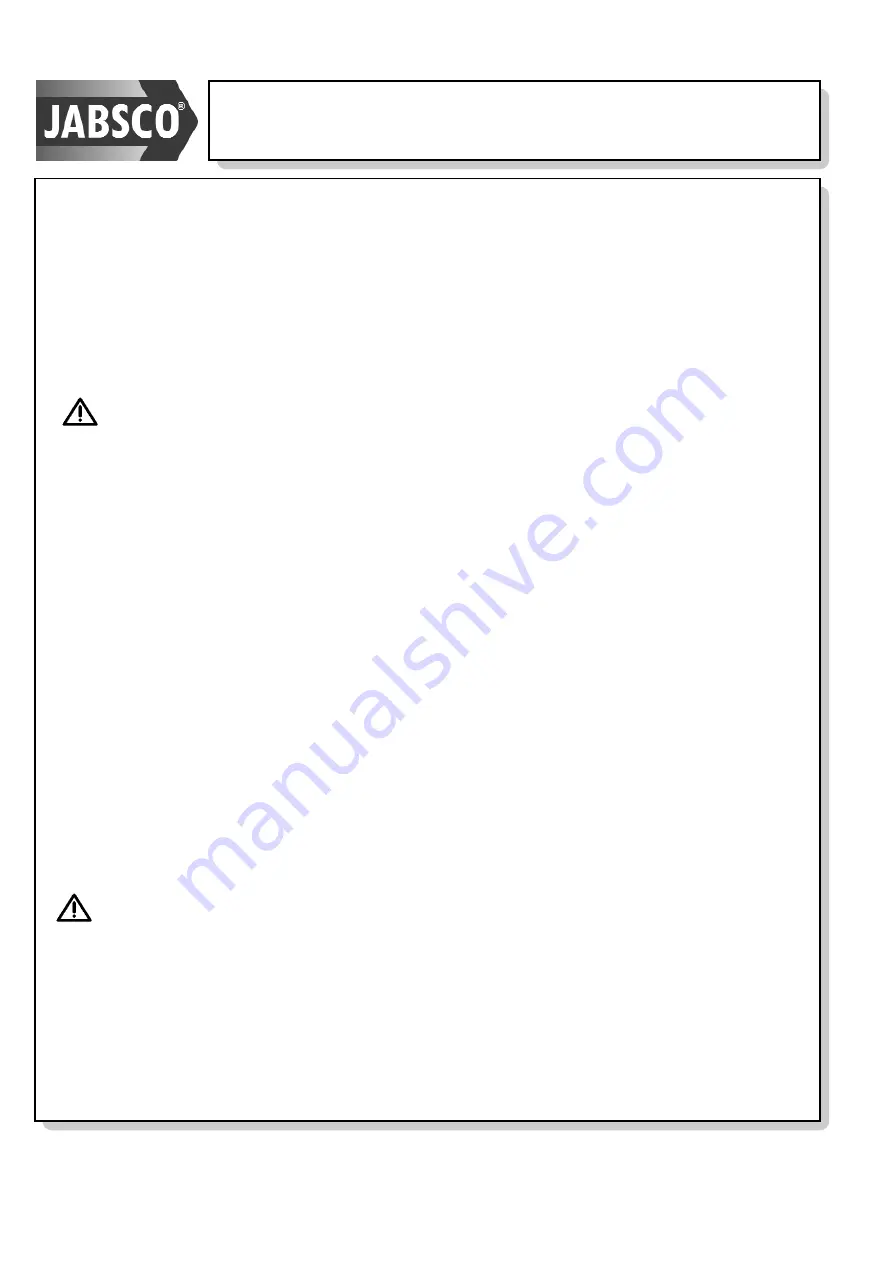
2.
INSTALLATION
Careful attention to correct installation of
Hy~Line
and
Ultima
lobe pumps, and
recognition of certain limitations to the
operating conditions of the pump, will
ensure long life and trouble-free running.
Failure to follow these instructions
could result in personal injury or
loss of life.
Take particular care over
the following:-
2.01 OPERATING LIMITATIONS
PRIMING:
Hy~Line
and
Ultima
pumps are
not truly self-priming and should be installed
in a “flooded inlet” pipe arrangement i.e. with
the pump lower than the level of liquid to be
pumped and with the supply pipe falling
continuously to the pump with no loops.
PRESSURE: Do not operate the pump
above the maximum differential pressure
shown on the Performance Data Sheet, not
even for a few seconds, as damage to the
pump components will result, leading to
metal particles in the pumped fluid,
ineffective cleaning and possibly complete
pump seizure.
NEVER run the pump against a closed
valve. Note that the pressure limit
varies with temperature.
SOLIDS:
Hy~Line
and
Ultima
lobe pumps
can handle soft solids in suspension but will
be damaged by hard particles. Take care
pumping solids, crystals, etc.
Never allow metal parts to enter pump, e.g.
weld metal, screws, tools, etc. as these will
stop the pump, leading to damaged rotors,
rotorcase and shafts.
CAVITATION: The pumps cannot operate
without sufficient pressure of liquid at the
inlet port to supply the pump. Normally
atmospheric pressure is sufficient but the
actual pressure needed (Nett Inlet Pressure
Required or NIPR), is higher for:-
High Viscosities
High Temperature
High Pump Speeds
Volatile Liquids
Insufficient inlet pressure will cause the
pump to cavitate leading to low
performance, noise and short pump life.
Ensure inlet pipes are short, large bore and
do not collapse under vacuum. Refer to
Performance Data Sheet for Nett Inlet
Pressure Required (NIPR) charts. If in doubt
consult your supplier before operating the
pump.
2.02 LOCATION & POSITIONING
Pump should be located:
• As close as possible to the fluid source
and as low as possible to maximize the
nett inlet pressure available to the pump.
• In a clear area allowing access all around
pump and drive for easy servicing.
• With space above for lifting equipment if
required.
• With port axis vertical if pump is required
to be self draining.
Page 4
Hy~Line
and
Ultima
Lobe Pumps
07/03
Summary of Contents for Hy-Line
Page 41: ...07 03 Page 39 Hy Line and Ultima Lobe Pumps 7 00 MODEL NUMBER BUILD CODE...
Page 43: ...07 03 Page 41 Hy Line and Ultima Lobe Pumps 8 01 PARTS LIST...
Page 44: ...Page 42 Hy Line and Ultima Lobe Pumps 07 03 8 01 PARTS LIST CONTENTS OF KITS...
Page 45: ...Page 43 Hy Line and Ultima Lobe Pumps 07 03 8 02 Hy Line EXPLODED DIAGRAM...
Page 46: ...07 03 Page 44 Hy Line and Ultima Lobe Pumps 8 03 Ultima EXPLODED DIAGRAM...
Page 47: ...07 03 Page 45 Hy Line and Ultima Lobe Pumps 8 04 Hy Line 3 Size SECTIONAL VIEW...