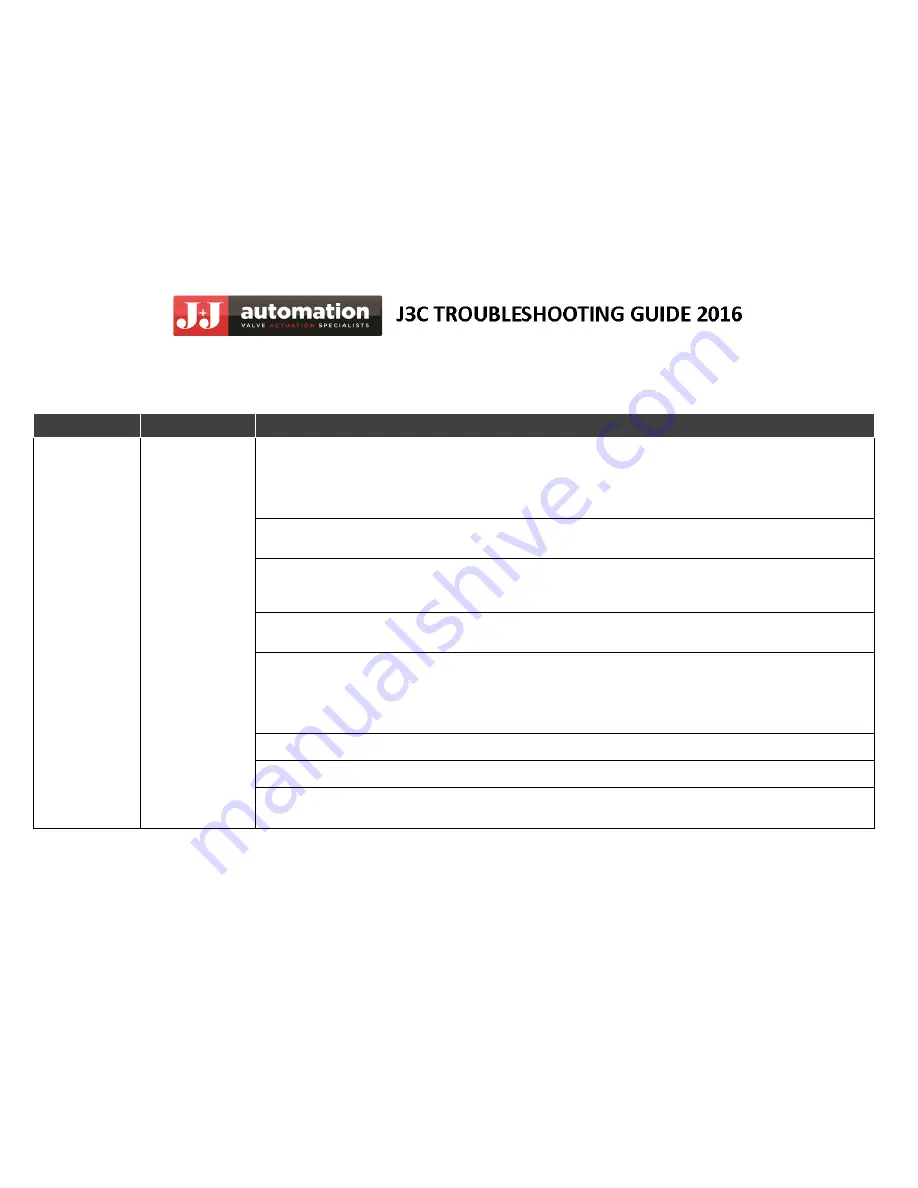
Page
13
of
18
MODULATING (DPS) – INSTALLATION ISSUES
REPORTED FAULT
POSSIBLE REASON(S) POSSIBLE SOLUTIONS/ ADVICE
DPS won’t set up
Incorrect installation
Notes:
•
ALWAYS test the actuator as an on-off actuator into which the DPS is going to be installed BEFORE installing the DPS, this confirms that
the actuator is working correctly before the function conversion.
•
Send the actuator to the CLOSED position before installing the DPS. Installing the DPS when the actuator is in the closed position
eliminates most of the issues users have associated with retro- installation.
•
The earth pin on the control Din plug has been connected to ground. This pin is used for an external soft reset procedure and must NOT
be connected to ground.
•
4 core cable has been used to wire the control Din plug and whilst respecting the wiring diagram and not connecting the earth, the
redundant 4
th
cable has been cropped but strands of it can touch terminals within the control Din plug causing short-circuit malfunction.
•
Each time this cropped cable touches the earth pin, the actuator will perform a soft reset.
•
Whenever external power is lost, on re-start the positioner performs a soft reset to recalibrate, the positioner will not respond to
control signal changes during this procedure.
•
The control Din plug wiring is incorrect and/ or
•
A signal with the wrong polarity is being applied.
•
Connecting the end of travel Din plug to the control Din plug - doing so would apply excessive voltage to the DPS PCB and cause
irreparable damage to the DPS PCB.
Such damage is not covered by the warranty.
Note
:
The control signal Din plug base is fitted upside-
down compared to the end of travel confirmation Din plug to prevent DIN plug connecting errors.
•
The white DPS PCB plug has not been pushed firmly home into the receiving socket on the main PCB.
•
The power polarity for DC power supplies has not been respected.
•
Cables trapped inside the actuator when the cover was replaced following DPS installation. Ensuring the internal cables (power, control
signal, end of travel switches and earth) are not crossed or twisted when the cover is replaced prevents a major cause of malfunctioning
DPS’s. Amongst other reasons, the control signal push-in plug can be pulled out if the cables are twisted or crossed.