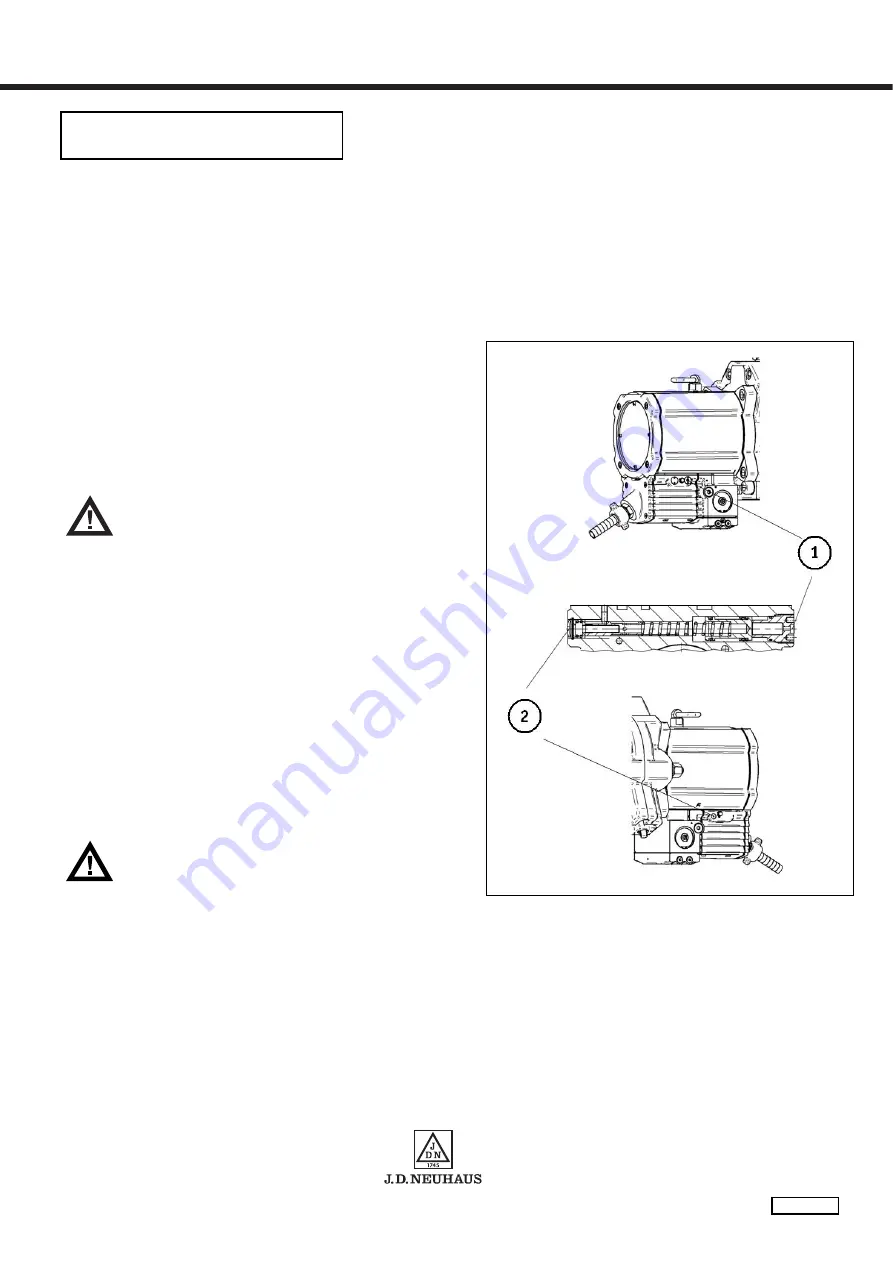
powered by air!
Page 61
MAINTENANCE
CHECKING AND ADJUSTING
OVERLOAD PROTECTION
All JDN Air Hoists are equipped with overload protection
as standard. This automatically deactivates the lifting movement of
the load hook if the hoist is loaded to the
pre-defined load parameter or higher. The switch-off point is 110%
to 125% of the permitted maximum load. After load hook is switched
off, the only movement available is lowering.
The overload protection can also be activated if the hoist is moved
at full unloaded speed and with a slack chain against a load to be
lifted, even when it is below the load size set.
We therefore recommend slowly tensioning the slack chain before
lifting the load.
OVERLOAD TESTING ON PROFI 25 TI TO PROFI 50 TI
The overload protection can be overridden for the purpose of an
overload test by simply unscrewing the screw plug.
DANGER!
After the test, make sure to screw the screw plug
back in and ensure that it fits tightly.
Unscrew the screw plug. The high-pressure hydraulic valve is
not now activated on the “Lift” side. For this reason the
deactivation function has no effect.
After the test, screw the screw plug back in and ensure that it
fits tightly.
ADJUSTING OVERLOAD PROTECTION
The adjustment method described here is based on the attachment
of test loads.
The adjustment is usually made at room temperature (approx.
20°C).
In the event of very high or very low operating temperatures, the
adjustment is to be corrected in relation to the temperature.
DANGER!
If the overload protection is set too high,
impermissibly high stresses may arise if a load
exceeding the permissible load carrying capacity is
attached.
There is a danger that the chain and device could
break.
Attach overload of 125% of the load-carrying capacity.
If the overload is lifted, the adjusting bolt must be adjusted
clockwise until it is no longer possible to lift the overload.
If the overload is not lifted, the adjusting bolt must be adjusted
anticlockwise until it is possible to lift the overload. The
adjusting bolt must then be turned back until it is just no
longer possible for it to lift the overload.
After the adjustment process, it must be possible to lift 110%
of the nominal load. A dynamic overload test at 110% of the
nominal load is thus possible.
Control valve with overload protection
(1) Screw plug for overload test
(2) Locking disc with cylinder screw for adjusting the overload
protection
Summary of Contents for PROFI 25TI
Page 67: ...powered by air Page 67 APPENDIX CIRCUIT DIAGRAM Rope control...
Page 68: ...powered by air Page 68 APPENDIX Dual control...
Page 69: ...powered by air Page 69 APPENDIX Dual control with pin valve Lower side OPTIONAL...
Page 70: ...powered by air Page 70 APPENDIX Quadruple control...
Page 71: ...powered by air Page 71 APPENDIX Quadruple control with pin valve Lower side OPTIONAL...