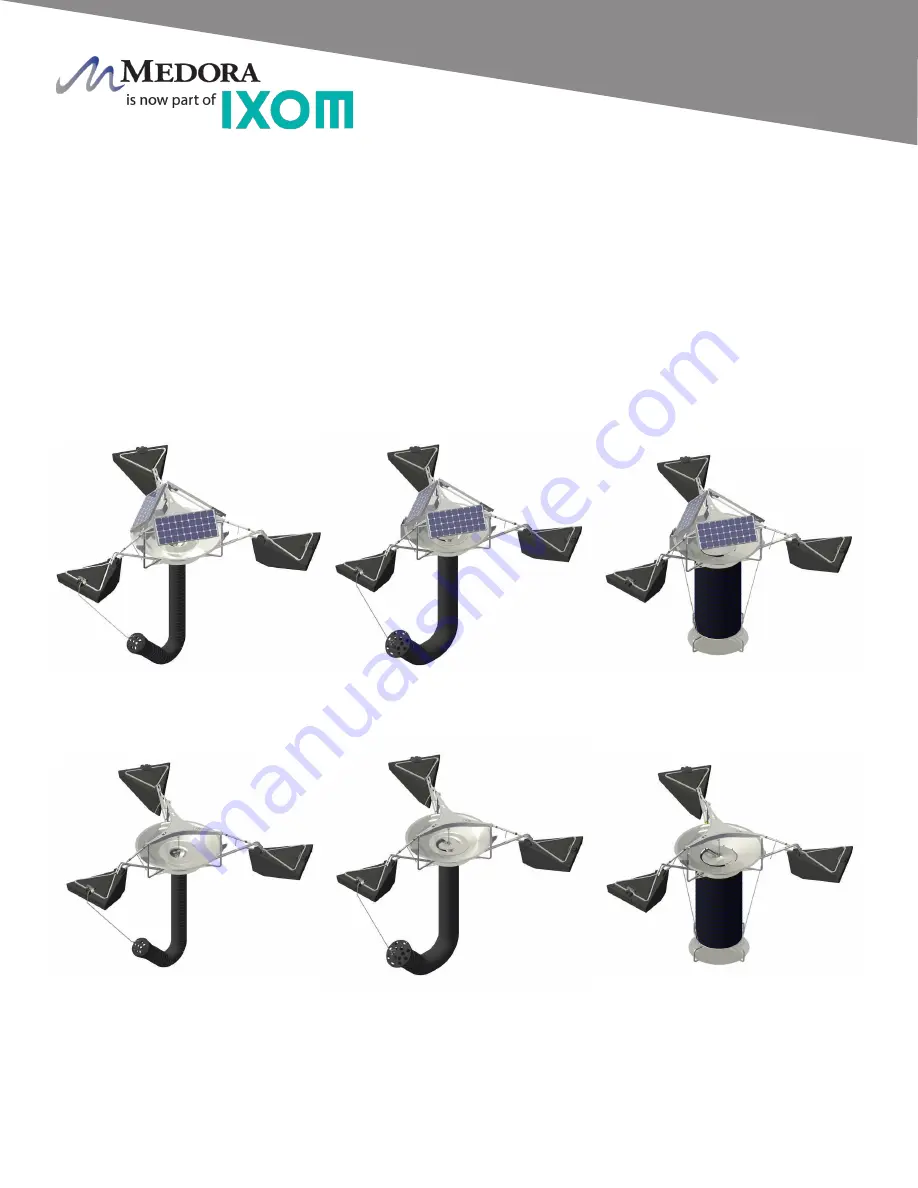
Hose / Strainer
- The hose is directly below the distributor dish and the strainer is located at the end of
the hose. The strainer contains a buoyant float ball inside that allows the strainer to draw water from
approximately 1.5 ft to 2 ft (0.45m to 0.6m) above solid bottom. The hose is designed to make a "J" shaped
bend at the bottom so that the strainer does not draw sediment up from the bottom. The strainer has a chain
connected to it and can be chained up at more shallow depths if necessary. The chain also is used for pulling
up the strainer to check it for plugging.
Hose and Strainer Configuration - MODEL MAY VARY
SB2500
SB10000
SB5000
GF2500
GF10000
GF5000
© 2020 Ixom | www.medoraco.com | 866 - 437 - 8076 | [email protected]
Features
Features
SB and GF Large Frame Mixers
10267_20200220
O&M_GF10000_10492_20201020 - 10