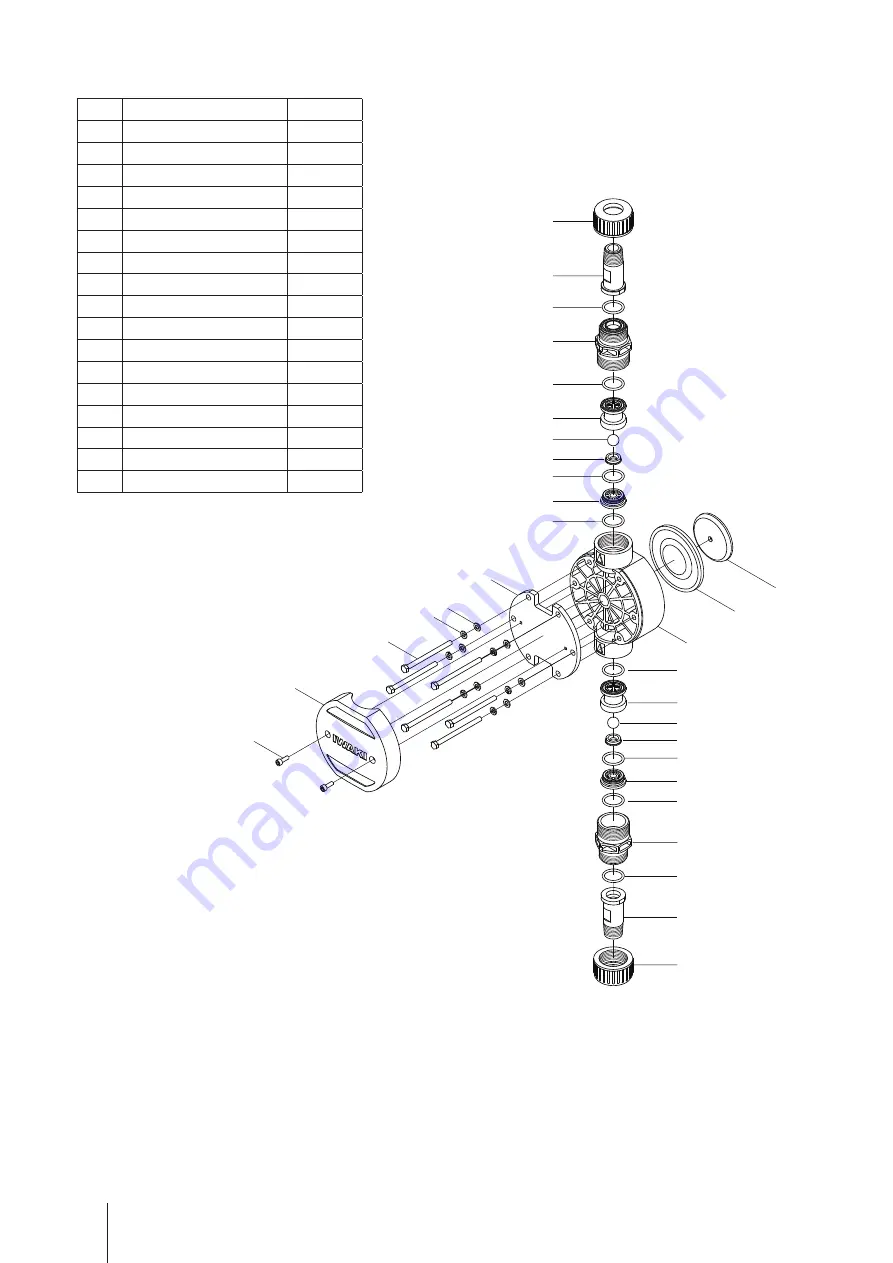
72
Exploded view
■ IX-C060 TC N
No.
Part names
# of parts
1
Pump head
1
2
Valve
2
3
Valve guide
2
4
Valve seat
2
7
O ring
8
9
Seat holder
2
16
Adapter
2
19
Hex socket head bolt
2
20
Hexagon head bolt
6
21
Spring washer
6
22
Plain washer
6
28
Bolt cover
1
29
Reinforcing plate
1
30
Diaphragm
1
31
Retainer plate
1
50
Nut
2
73
Fitting
2
1
30
31
20
22
3
9
4
7
2
73
50
7
7
7
16
3
9
4
7
2
73
50
7
7
7
16
19
29
28
21