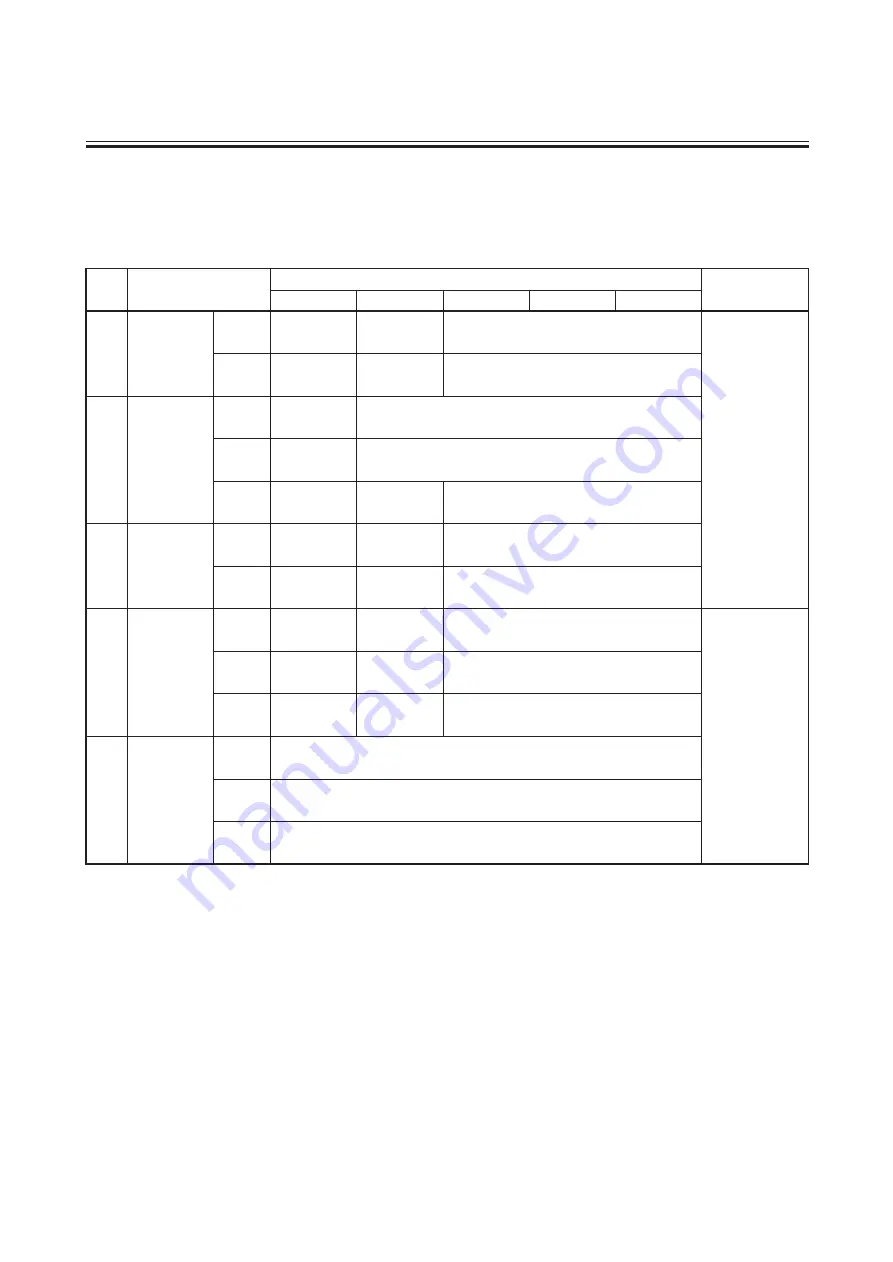
- 28 -
4. Consumable parts
Consumable parts are necessary to be replaced to ensure long, continuous operation of the pump. Replace following
consumable parts according to the time to be replaced and notes shown as below.
See pages 8, 9 and 29 to identify parts number and parts.
Note 1. Time to be replaced mentioned above is based on pumping clear water at ambient temperature and it depends
on the characteristics, temperature and other condition of pumped liquid.
2. Rear casing unit (2+19.1+20), bearing (21) and mouth ring (22) must be replaced when their wear limit comes
as mentioned on page 37 regardless of the time to be replaced shown on above table.
3. O ring (23) and gasket (24) must be replaced every time when pump is disassembled regardless of the time to
be replaced shown on above table.
4. Parts of KK type of MDF-L401 are replaced as totally assembled pump head unit.
No.
Parts name
Parts code
Time to be
replaced
MDF-L250
MDF-L401
MDF-L422
MDF-L423
MDF-L425
2
+
19.1
+
20
Rear casing
unit
CF
AA
MFL1393
MFL1437
MFL1502
10,000 hours
KK
MFL1394
——
MFL1503
21
Bearing
CF
MFL0565
MFL0580
AA
MFL0567
MFL0582
KK
MFL0568
——
MFL0583
22
Mouth ring
CF
AA
MFL0555
MFL0555
MFL0755
KK
MFL0556
——
MFL0756
23
O ring
FKM
MFL0034
MFL0080
MFL0130
10,000 hours
EPDM
MFL0035
MFL0081
MFL0131
Aflas
MFL0036
MFL0082
MFL0132
24
Gasket
FKM
MFL0031
EPDM
MFL0032
Aflas
MFL0033