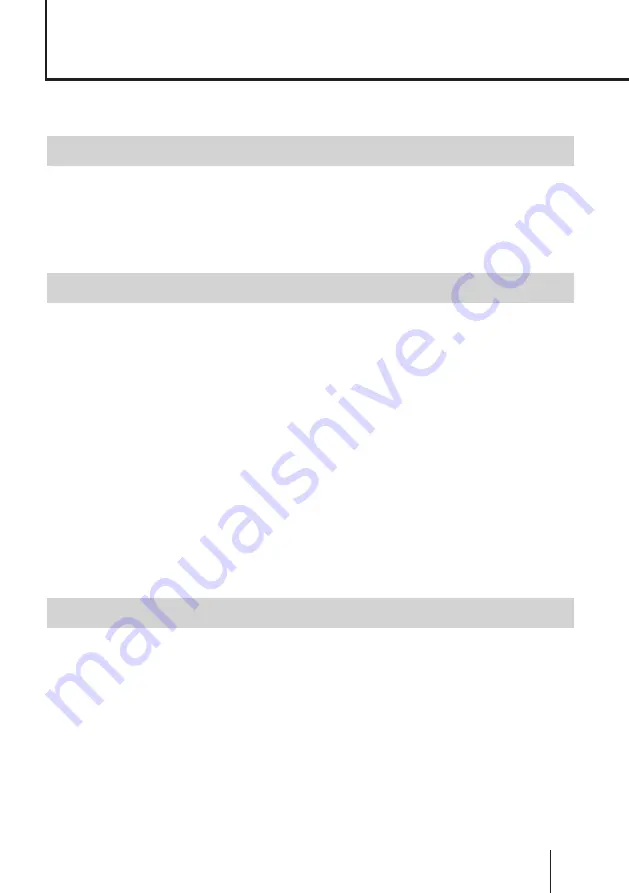
3
Contents
Contents
Order confirmation
............................................................................................. 2
Safety instructions .......................................................................6
Warning
............................................................................................................. 7
Caution
.............................................................................................................. 8
Precautions for use
........................................................................................10
Overview ...................................................................................... 12
Introduction
.....................................................................................................12
Pump structure & Operating principle
.........................................................12
Features
.......................................................................................................13
Operational functions
....................................................................................13
Manual mode
...............................................................................................13
Part names
.......................................................................................................14
Pump
............................................................................................................14
Operational panel
........................................................................................15
Basic displays & Pump states
................................................................16
Identification codes
........................................................................................17
Installation .................................................................................. 18
Pump mounting
...............................................................................................18
Plumbing
..........................................................................................................19
Tube connection
..........................................................................................19
Check valve mounting
.................................................................................21
Wiring
.............................................................................................................. 23
Power voltage/Earthing
.............................................................................. 23