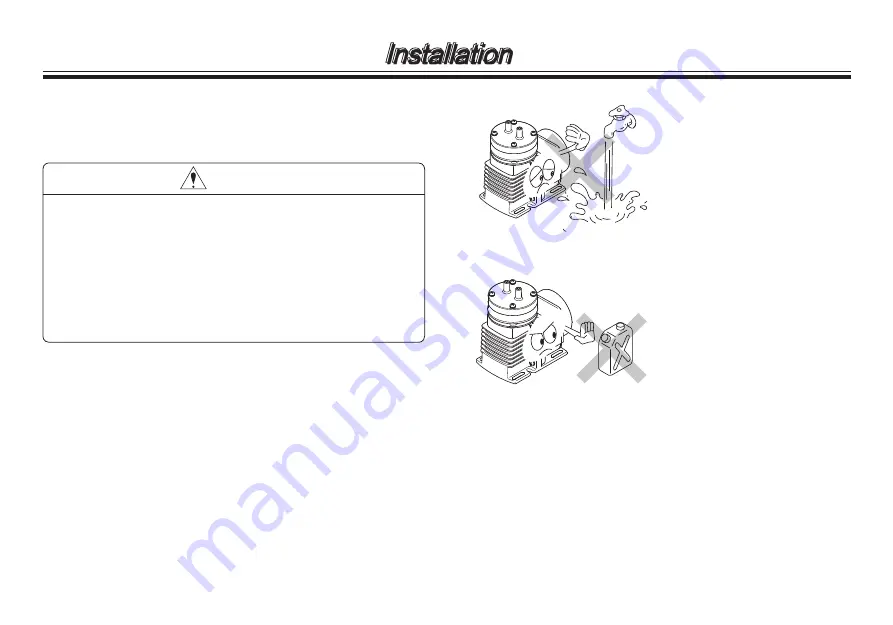
- 8 -
● Do not install the pump in a
place where the pump can
get wet. Avoid using wet gas,
or internal condensation will
build up and consequently
result in the short lives of the
valve and diaphragm.
● Do not install the pump in a
corrosive or flammable gas
atmosphere. Keep good ven-
tilation in a working area.
● Ambient temperature should
not fall below 0°C or exceed
40°C. Observe the allowable
gas temperature range of 0
and 40°C.
1. Before Installation
Read through this instruction manual before use. Carry
out installation work with a full understanding.
Installation
● Do not operate the pump in a flammable atmos-
phere
Do not place explosive or flammable material near
the pump.
● Do not use a damaged pump
Use of a damaged pump could lead to an electric
shock or death.
CAUTION