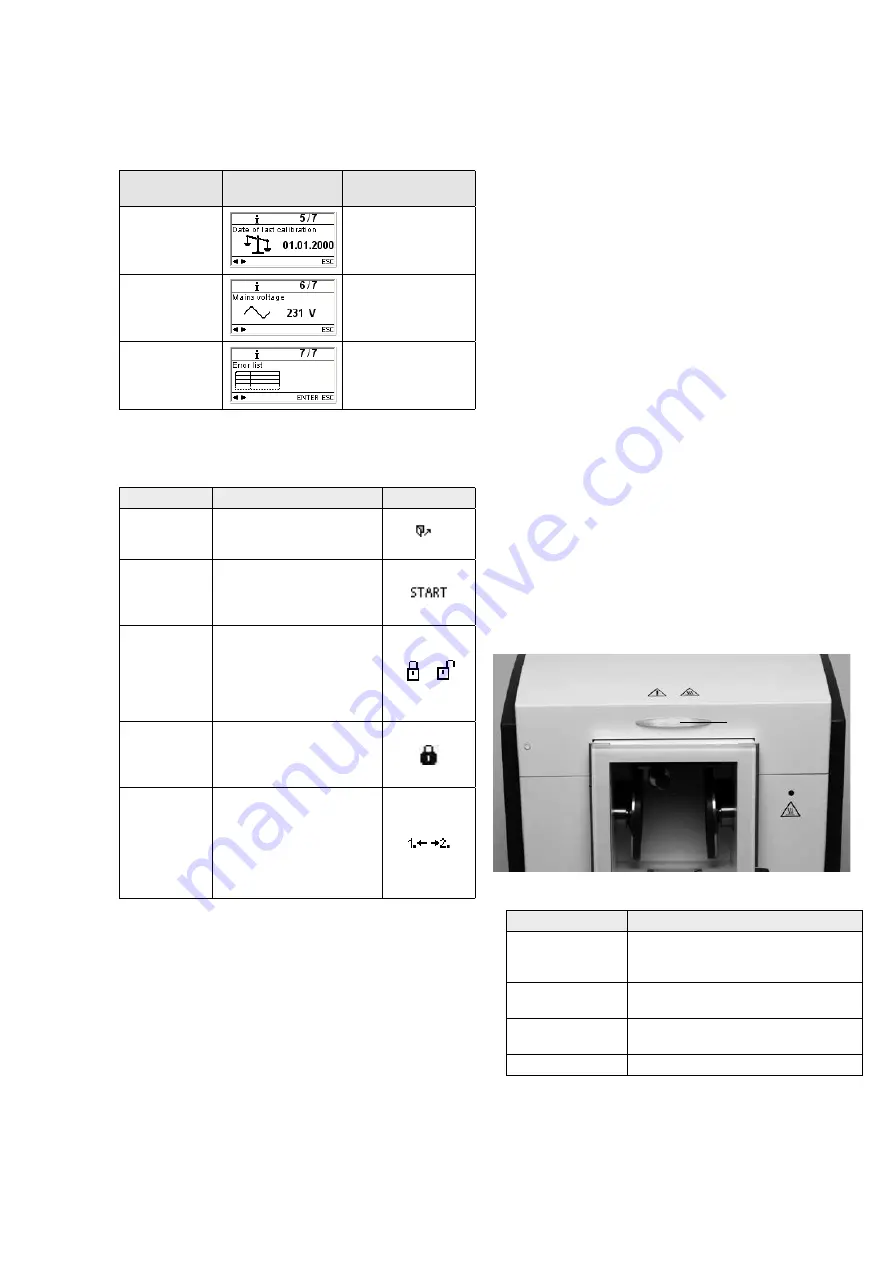
16
Settings
Indication on
display
Short description
Date of the latest
calibration
Supply voltage
Shows the current
supply voltage.
List of errors
5.5 Explanation of the symbols on the display
Symbol name
Explanation
Symbol
Door open
Shows that the door is open.
The door must be closed in
order to start a program.
Start possible
Shows that the injector is
ready to use. The door is
closed and a program can be
started.
Program write
protection
A closed lock indicates that
the program write protection
is active. With an open lock,
this protection is inactive
(adjustable with the – or +
key).
General write
protection
If this symbol is displayed, the
general write protection is
active. This protection applies
to all injector programs.
Page selection
Program parameters are
available on two pages. By
selecting the appropriate
symbol with the cursor key
and by pressing ENTER, the
program changes to the
respective page.
5.6 Description of the beeper sounds
Basically, the beeper tune and volume set by the user are used for
all acoustic signals. The acoustic signal can be stopped by pressing
STOP.
1. After the self-test has been completed
The set beeper tune briefly sounds to inform the user that the
automatic self-test has been successfully completed.
2. In the case of error messages
Error messages are indicated with the error beeper tune (endless
beeping). The beeper can be confirmed by pressing the STOP key,
while the error message still remains visible. If the error message
is confirmed by pressing the ESC key, the beeper is also ended.
3. At the end of an injection program
The set beeper tune briefly sounds to inform the user that the
current program has been completed.
4. Upon opening of the safety door during an injection program in
progress
If the safety door is opened while an injection program is
running, the user is warned by the error tune (endless beeping).
The acoustic signal can be stopped by closing the safety door.
5.7 Operating status display
The integrated optical operating status display (OSD) indicates the
different operating statuses of the injector.
The following activities are indicated:
Colour
Activities
green
The injector is ready for operation (with
the door closed and the self-test
completed).
white
The injector is in the preparation stage
(with the door open).
red
The injection process is active; injector is
busy.
yellow (flashing)
Information, note or error message.
13