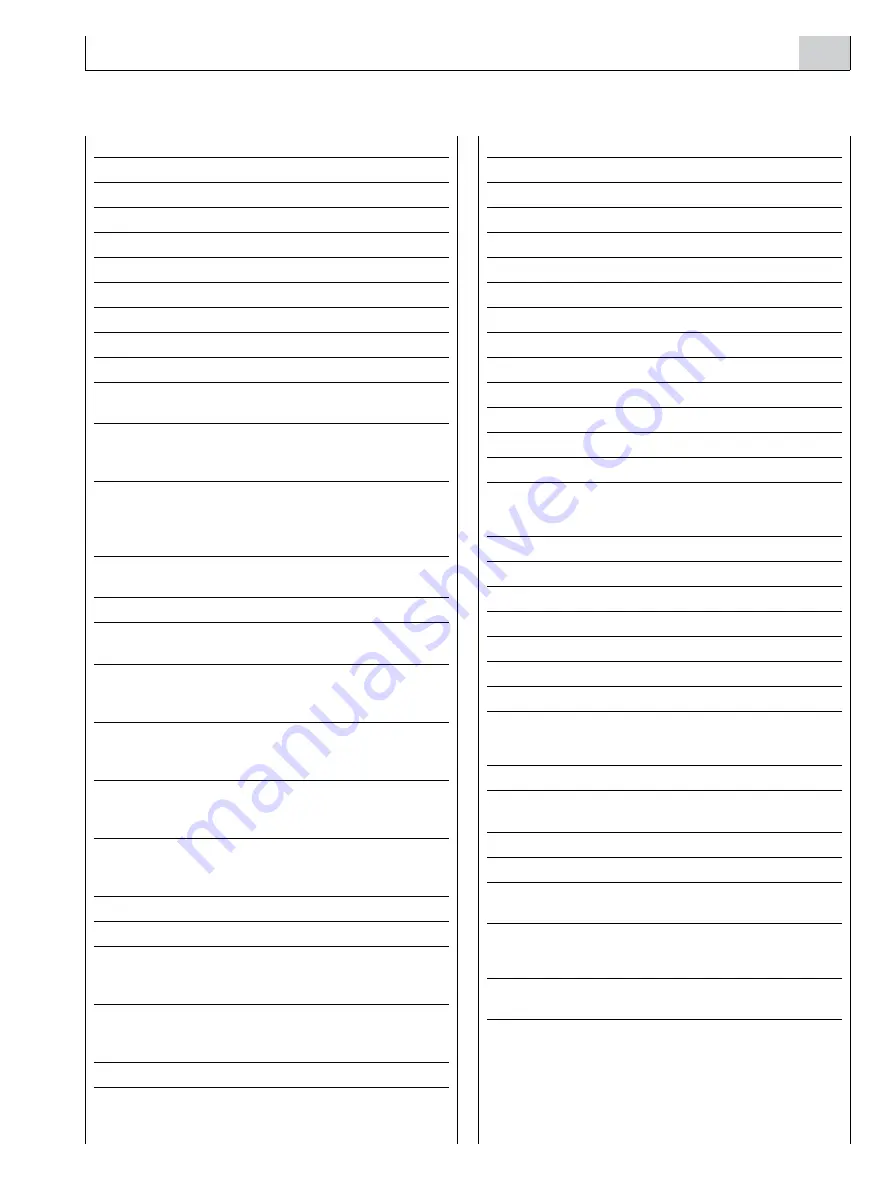
installation directiVe
51
MAY 2006
N40 ENT M25
N60 ENT M37-M40
Electrical equipment component code (follows)
connectors
A
36 pole EDC engine components
A1
16 pole EDC electro-injectors
A2
89 poles EDC boat side
E1
cylinders 1 and 2 electro-injectors
E2
cylinders 3 and 4 electro-injectors
E3
(
*
)
cylinders 5 and 6 electro-injectors
ECF
(
s
) for the engine stopping function if stressed
ECM
(
s
) for the engine stopping function if stressed
J1
external diagnostic tool (on the relay box panel)
JA
connection between engine wiring and interface
wire harness
JA
on
secondAry
digitAl
instrument
pAnel
set for connection to the main digital
instrument-panel
JB
on
engine
wire
hArness
set for connection to the main analog
instrument-panel or to the interface wire
harness for converter module
Jc
on
mAin
AnAlog
instrument
pAnel
set for connection to the engine wire harness
JD
IVECO MOTORS indications and alarms module
Jd
on
interfAce
wire
hArness
for
converter
module
external throttle control
Je
on
mAin
AnAlog
instrument
pAnel
set for connection to the secondary analog
instrument panel
Je
on
interfAce
wire
hArness
for
converter
module
set for connection to the main digital
instrument-panel
Je
on
mAin
digitAl
instrument
pAnel
set for connection to the secondary digital
instrument panel
Je1
on
interfAce
wire
hArness
for
converter
module
set for connection to the 2
nd
main digital
instrument panel
JF1
relay box
JF2
relay box
Jh
on
secondAry
AnAlog
instrument
pAnel
set for connection to the main analog
instrument-panel
Jh
on
mAin
digitAl
instrument
pAnel
set for connection to the interface wire harness
for converter module
JO
converter for digital panels
indicator lights
EDC
EDC malfunction
SAC
presence of water in fuel pre-filter
SATA
high coolant temperature
SBLA
low coolant level
SBPO
low oil pressure
SCP
pre-post heating
SIFA
clogged air filter
SIFB
clogged oil vapor filter
SIFC
clogged fuel filter
SIFO
clogged oil filter
SP
pre-lubrication
SS
alternator fault
SSV
runaway engine
Gauges
CG
revolution-counter
MI
gear box oil pressure gauge
MO
engine oil pressure gauge
TA
engine temperature
TI
gear box oil temperature
TS
exhaust gas temperature
V
voltmeter
relays contained in the relay box
K1
fuel filter heater element power supply
K2
power supply to terminal 50 of the electric
starter motor
K3
key switch electric discharge
K4
emergency engine shut-down provision
K5
start request signal, from key switch to EDC
electronic unit
Fuses contained in the relay box
F1, F2, F3, F4, F5
self restoring (not replaceables)
(
*
) Not applicable for the 4 cylinders
(
s
) Present on the wiring of the new model
Summary of Contents for NEF N40-ENT-M25
Page 64: ...INSTALLATIONDIRECTIVE 64 N40 ENT M25 N60 ENT M37 M40 MAY 2006 ...
Page 69: ......