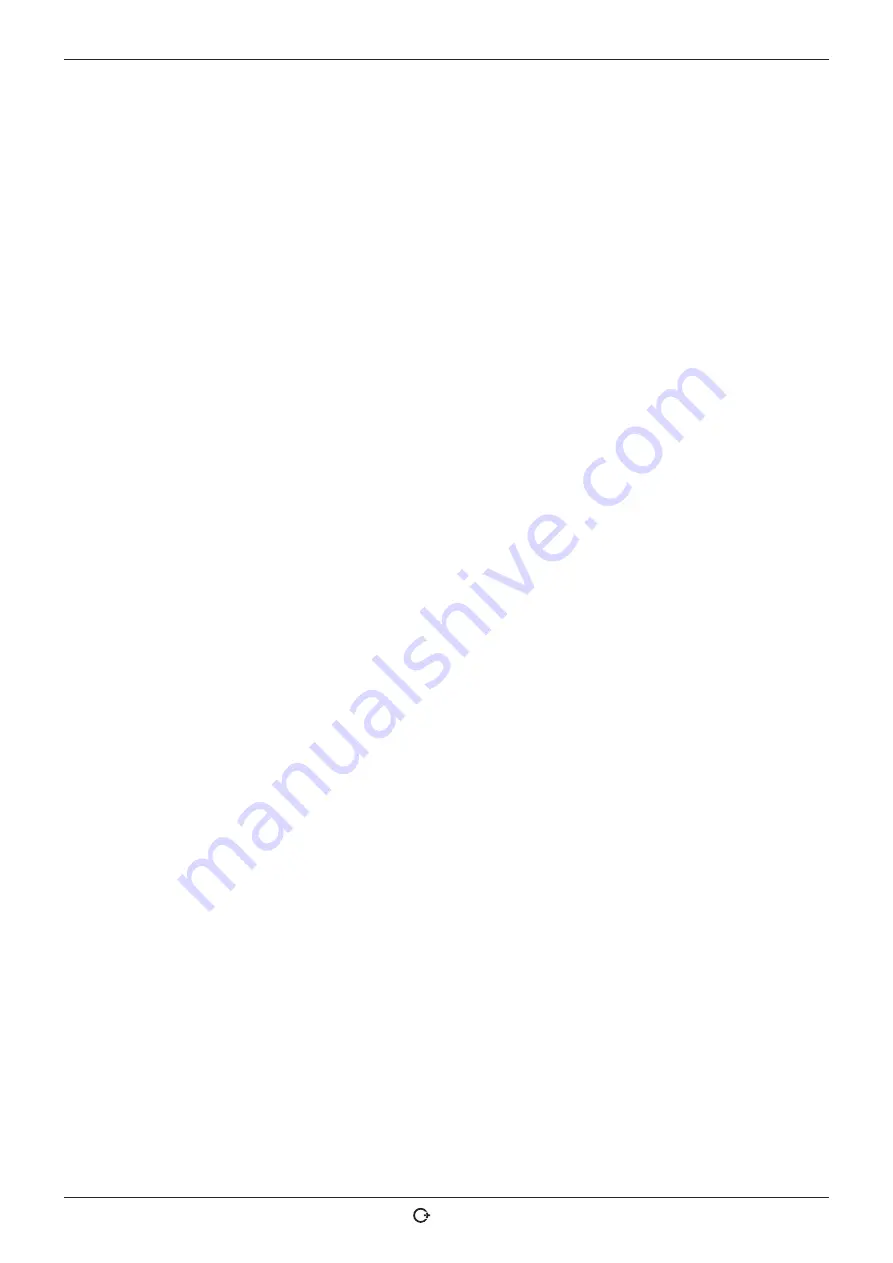
ORBIMAT CA
| Operating instructions
Features and scope of application
(09.03.15) OW_ORBIMAT_CA_BA_871060202_04_EN
orbitalum tools
GmbH, D-78224 Singen, www.orbitalum.com, Tel. +49 (0) 77 31 792-0
17
4.2.3
ORBIMAT 300 CA AVC/OSC
• The new arc voltage control calculates and programs the length of the arc automatically in "mm" from the current
voltage characteristics. This avoids the usual time spent calculating the necessary arc voltage each time the weld
power changes to maintain the arc at a consistent length in the individual sectors.
• During oscillation each of the edge holding times can be synchronized with the high-pulse settings.
• The center of the seam can be accessed manually and be determined using an automatic scanner. The electrode ac-
cesses each of side of the seam and then calculates the center of the path automatically. For asymmetric weld seam
configurations this is compensated by an OFFSET function.
• Including remote control (cable length: 7,5 m) Code 875 050 001.
• There is the option of an HF-free touch start ignition.
4.3
Functional description
• The machine is supplied with voltage and controlled by the orbital welding power supply.
• The weld head is clamped to the pipe to be welded using clamping inserts or clamping jaws. The weld head is ar-
ranged in such a way that the weld electrode is located radially over the weld joint.
• After ignition of the weld arc, the electrode is guided around the workpiece at the speed specified by the welding
controller and the weld seam is constructed.
• The cassette (closed weld heads only) is fully closed and thus forms a space which keeps the atmospheric air away
from the weld point.
• A procedure is required for welding with the machine. The machine features a procedure library, which enables pro-
cedures to be created and can create a procedure automatically via auto programming. You do not need to carry out
complex calculations, as the software calculates the required parameters automatically depending on the welding
task.
• After entering the pipe diameter, wall thickness, material and gas type, the machine creates a procedure sugges-
tion. This procedure suggestion usually requires only minimal adjustments which can be determined by carrying
out a test run of the procedure, for example.