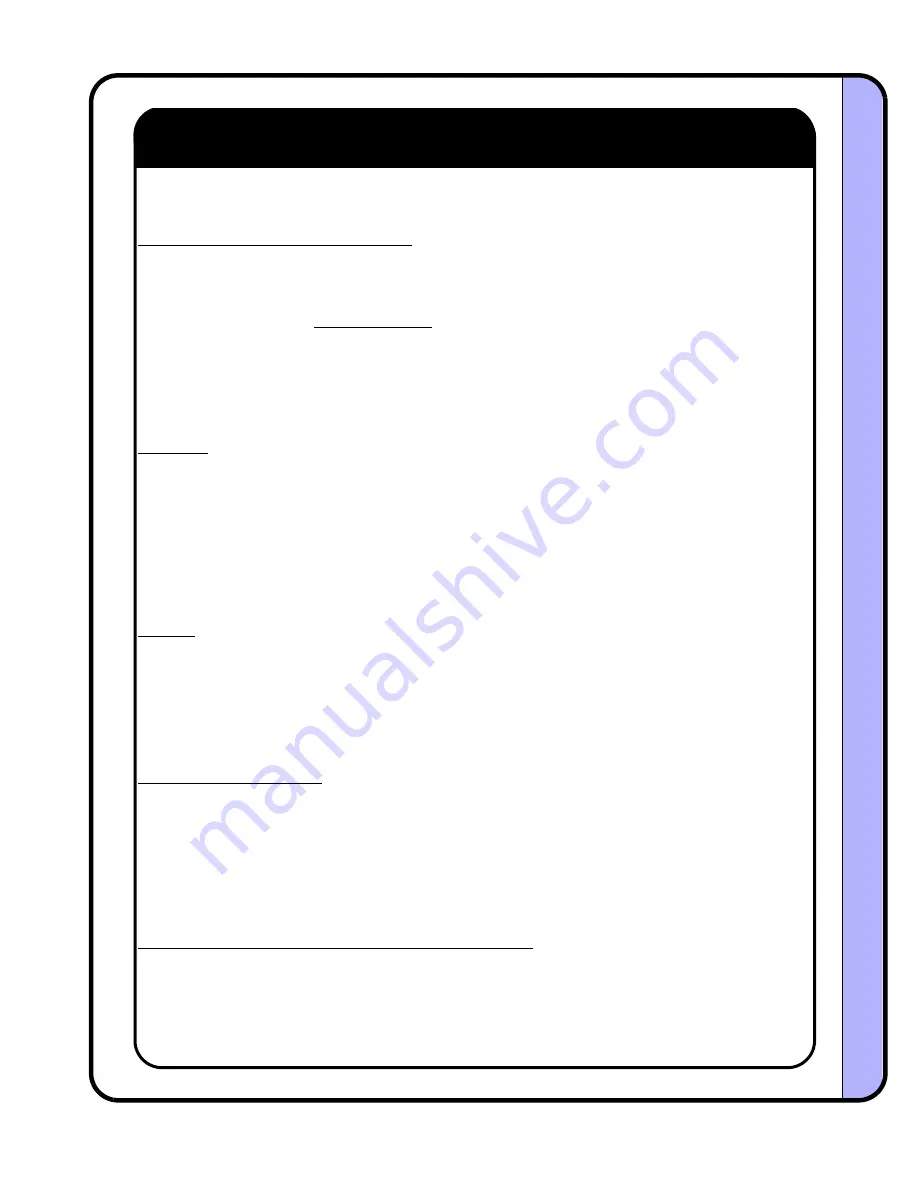
Step 15 - Make Final Adjustments
Goal:
Make fine adjustments to optimize the performance of the system once running
•••• Sub-Step (a) ••••
Product Delay (Second Product Delay)
The product delay controls the time between the product detector trigger and start of the application
cycle. To get a good starting value, use the following equation:
This would place the label on the leading edge of the product, so extra time must be added to place
the label further down the product.
•••• Sub-Step (b) ••••
Air Assist
As other changes are made to the system, including tamp cylinder mount adjustments, air cushion
settings, and label adjustments, it may be necessary to re-adjust the air assist tube position and/or air
assist flow control to have a strong air current driving the label up toward the pad. Keep in mind that
labels closest to the core of the roll will have more “memory” or curl, than labels located away from the
core. An air assist flow that works well for the majority of the roll in the beginning may not be enough
for the last labels near the core. After the first full roll has been run through, the air assist may need to
be slightly increased to overcome the label curl.
•••• Sub-Step (c) ••••
Vacuum
Similar to the adjustment above for the near roll-end labels, the memory curl of the labels closest to
the core may require a greater vacuum setting then the labels on the beginning of the roll. Increase
the vacuum to a level that works well for the beginning 80% of the roll, but equally as well for the
remaining 20%. If the vacuum is too high, it will be most notable when the transfer to the product
suffers. It will also be noticeable over time in the frequency of filter cleaning required.
•••• Sub-Step (d) ••••
Auto Retract (if equipped)
The auto retract delay time can be adjusted to suit the needs of the particular application. By setting
the correct time value, the sensor can detect the product and reverse direction of cylinder travel to
provide the lightest contact possible. Since the sensor can detect brown corrugate up to 2 inches
away, it is possible to use the maximum cylinder speed and the lowest contacting force, simply by
adjusting this value. This means that variable height (or width if side apply) products will be contacted
with the same force, regardless of tamp duration time.
•••• Sub-Step (e) ••••
Repeat Print / Repeat Tamp (if label present is installed)
Once the system is operating to satisfaction, the repeat print and repeat tamp settings can be
activated to detect any feeding anomalies. By setting the repeat print to a value greater than zero, the
unit will go offline with an error if the system attempts to print more than the specified value without
tamping. Likewise, the repeat tamp will prevent multiple applications of the same label to multiple
products. These two controls prevent label jams, mis-labeled products, labels stuck to the tamp pad
face, and out of sequence labeling.
Product Delay (mS) =
5000
Linespeed (FPM)
Product Detect to Peel Blade Distance (inches)
X
Diagraph - an ITW Company PA/4600 & PA/6000 User Manual
Setup
Page 25
Setup
Summary of Contents for Diagraph PA/4600
Page 1: ...PA 4600 PA 4600 PRINTER APPLICATOR PRINTER APPLICATOR PA 6000 PA 6000 4600 010 Revision G ...
Page 47: ...Diagraph an ITW Company PA 4600 PA 6000 User Manual Maintenance Page 46 Maintenance ...
Page 48: ...Diagraph an ITW Company PA 4600 PA 6000 User Manual Maintenance Page 47 Maintenance ...
Page 49: ...Diagraph an ITW Company PA 4600 PA 6000 User Manual Maintenance Page 48 Maintenance ...