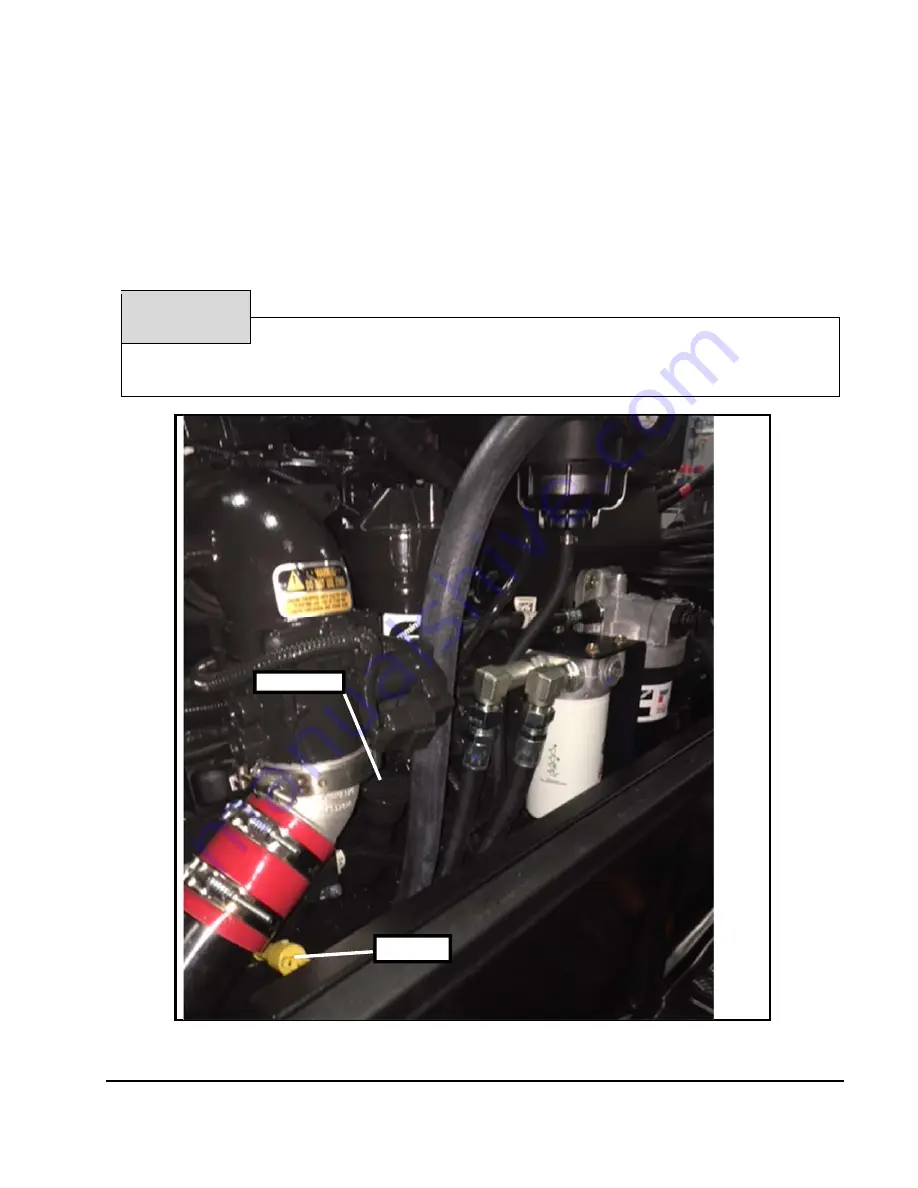
Operation Manual – ITW GSE 4400 Tier 4
d) Changing engine oil
Change the oil once after the first 50 - 150 hours of use and then every 500 hours of engine
operation thereafter. The generator set is equipped with an hour meter to record actual engine
operating time.
The ideal time to change engine oil is soon after a power delivery run, when the engine is at
operating temperature. If lubricating oil is drained immediately after the unit has been run for
some time, most of the sediment will be in suspension and will drain readily.
Change the oil filter element each time the oil is changed.
CAUTION
High ash oils may produce harmful deposits on valves that can cause valve
burning.
Do not use solvents as flushing oils in running engines.
Always use clean containers, funnels, etc.
Figure 2-2-3: Oil Fill and Check Locations
Dipstick
Oil Fill
OM2247 Rev B
Page 69 of 125
Summary of Contents for 4400 Tier 4
Page 27: ...Operation Manual ITW GSE 4400 Tier 4 OM2247 Rev B Page 26 of 125 ...
Page 42: ...Operation Manual ITW GSE 4400 Tier 4 OM2247 Rev B Page 41 of 125 ...
Page 44: ...Operation Manual ITW GSE 4400 Tier 4 OM2247 Rev B Page 43 of 125 ...
Page 52: ...Operation Manual ITW GSE 4400 Tier 4 c Black Box OM2247 Rev B Page 51 of 125 ...
Page 56: ...Operation Manual ITW GSE 4400 Tier 4 OM2247 Rev B Page 55 of 125 ...
Page 123: ...OM2247 Rev B Page 122 of 125 ...
Page 124: ...OM2247 Rev B Page 123 of 125 ...
Page 125: ...OM2247 Rev B Page 124 of 125 ...
Page 126: ...OM2247 Rev B Page 125 of 125 ...