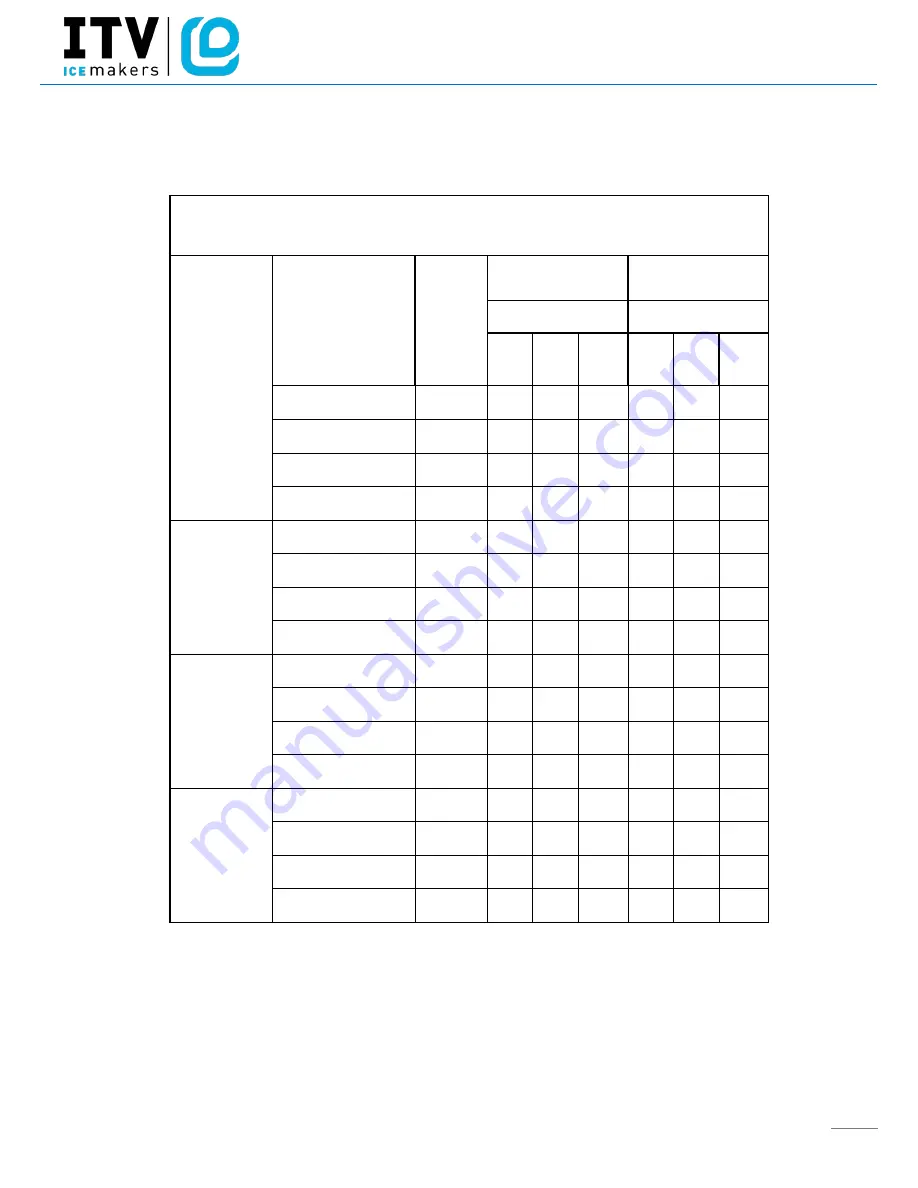
SERVICE MANUAL SPIKA SERIES
30
7.1. Dimensions, voltage
SPIKA NG
MODELS
(USA)
COOLING
machine dimensions pakaging dimensions
(inch)
(inch)
Width
X
Depth
Z
Height
Y
Width
X
Depth
Z
Height
Y
SPIKA NG
125
SPIKA NG 125-A1F
Air
21,1
23,4
31,3
24,4
26,0
36,2
SPIKA NG 125-A1H
Air
21,1
23,4
31,3
24,4
26,0
36,2
SPIKA NG 125-W1F
Water
21,1
23,4
31,3
24,4
26,0
36,2
SPIKA NG 125-W1H
Water
21,1
23,4
31,3
24,4
26,0
36,2
SPIKA NG
175
SPIKA NG 175-A1F
Air
26,0
27,6
33,0
29,3
30,3
38,2
SPIKA NG 175-A1H
Air
26,0
27,6
33,0
29,3
30,3
38,2
SPIKA NG 175-W1F
Water
26,0
27,6
33,0
29,3
30,3
38,2
SPIKA NG 175-W1H
Water
26,0
27,6
33,0
29,3
30,3
38,2
SPIKA NG
215
SPIKA NG 215-A1F
Air
26,0
27,6
33,0
29,3
30,3
38,2
SPIKA NG 215-A1H
Air
26,0
27,6
33,0
29,3
30,3
38,2
SPIKA NG 215-W1F
Water
26,0
27,6
33,0
29,3
30,3
38,2
SPIKA NG 215-W1H
Water
26,0
27,6
33,0
29,3
30,3
38,2
SPIKA NG
285
SPIKA NG 285-A1F
Air
30,0
30,0
33,0
32,9
32,9
38,2
SPIKA NG 285-A1H
Air
30,0
30,0
33,0
32,9
32,9
38,2
SPIKA NG 285-W1F
Water
30,0
30,0
33,0
32,9
32,9
38,2
SPIKA NG 285-W1H
Water
30,0
30,0
33,0
32,9
32,9
38,2
Summary of Contents for SPIKA MS 1000
Page 39: ...SERVICE MANUAL SPIKA SERIES 39 9 WIRING DIAGRAMS 9 1 SPIKA NG under counter models ...
Page 40: ...SERVICE MANUAL SPIKA SERIES 40 9 2 SPIKA MS 700 ...
Page 41: ...SERVICE MANUAL SPIKA SERIES 41 9 3 SPIKA MS 500 AND SPIKA MS 1000 A W ONE PHASE ...
Page 42: ...SERVICE MANUAL SPIKA SERIES 42 9 4 SPIKA MS 1000 THREE PHASES ...