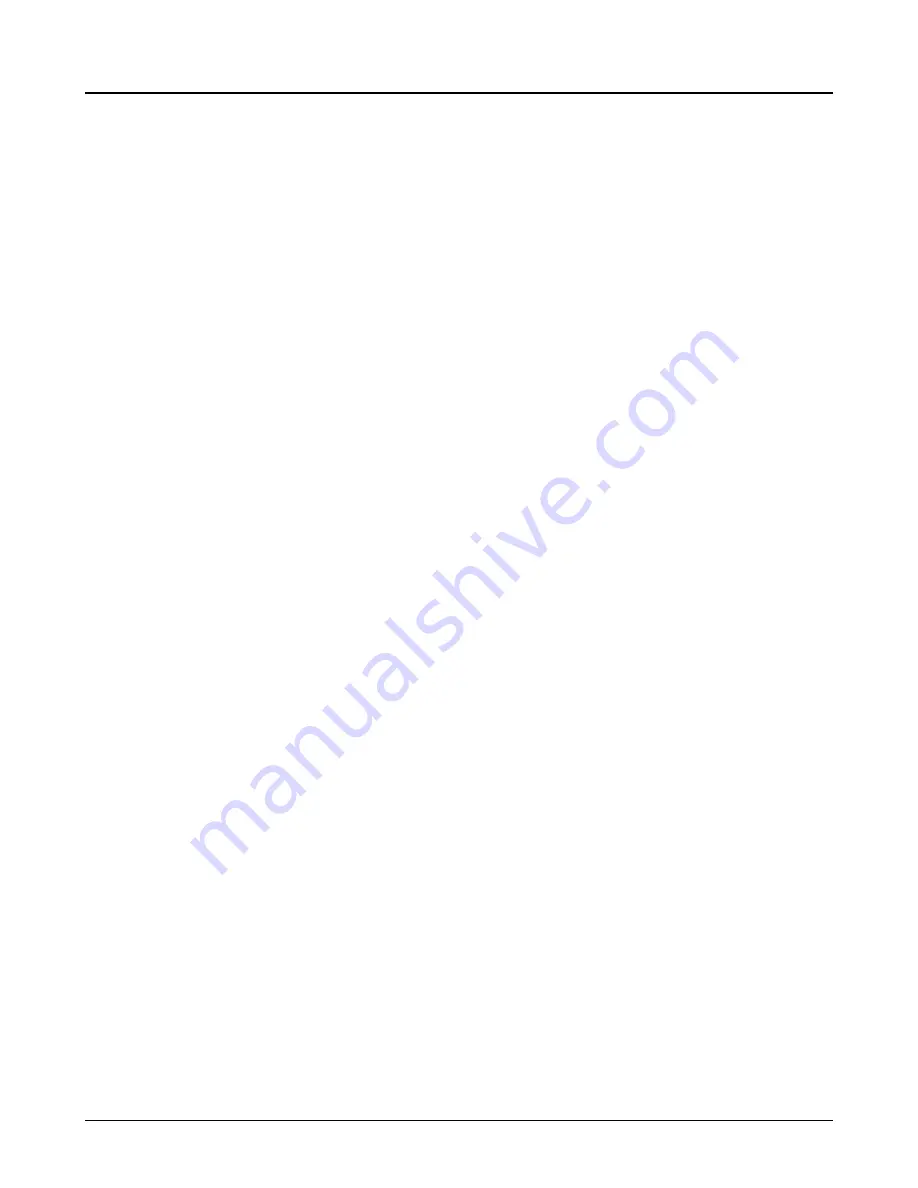
4 Installation
4.1 General
Pumping unit should be placed as close as practical to the source of supply. Floor space and head room
allotted to the unit must be sufficient for inspection and maintenance. Be sure to allow for crane or hoist
service. The unit should be mounted on a substantial rigid and leveled base to prevent distortion of the
pump. Grouting of the base is recommended. Oil lubricated pumps must be installed in the horizontal po-
sition. The Model 3335 should never run dry. If there is any possibility that the pumps source of liquid
might fail, a protective device should be incorporated into the system to shut the pump down.
4.2 Piping
The suction pipe must never be smaller than diameter of pump suction nozzle. Use of suction pipe one
or two sizes larger is desirable. Quick closing valves should be avoided to protect the pump from dam-
age due to shock. All piping should be independently supported and align naturally to the pump flanges.
Piping should be run from the pump with final connections made at a point downstream. This is to pre-
vent problems with pump flange bolt hole alignment. The discharge head should never be loosened to
make up piping downstream of the pump. For operation at low flow, or to ensure liquid will always be
flowing through the pump, a bypass line should be installed. The bypass line should be returned to the
liquid source and injected below minimum liquid level to prevent air entrainment. If a bypass line is not
used, it is recommended that precautions be taken to insure that the pump will not run dry, run at closed
discharge, or handle pumpage of excessive temperature at pump suction. Devices which can protect the
pump from the above problems are flow switches or high temperature switches.
Install gauge connections at the pump discharge and suction. The connections should be located be-
tween the pump and its discharge and suction valves. When a suction screen is used an additional con-
nection is recommended for measuring pressure drop across the screen.
4.3 Alignment procedures
Pump and motor must be brought into both parallel and angular alignment, using one of the methods
listed below. Use of the dial indicator method of parallel alignment is preferred.
Parallel Alignment - Dial Indicator Method
Mount a dial indicator on the driver shaft to read on the pump coupling hub. "Zero" the dial indicator at
the top. Turn the driver shaft and check the dial indicator reading at four points 90° apart on the pump
coupling hub. Correct the parallel alignment by moving the driver side to side or by shimming it up or
down. Parallel alignment is achieved when side to side readings agree within 0.004" TIR. Set mo-
tors .002" (.004" TIR) to .004" (.008" TIR). Low regardless of pumpage temperature. Note: TIR is Total
Indicator Reading.
4 Installation
8
3335 Installation, Operation and Maintenance Instructions