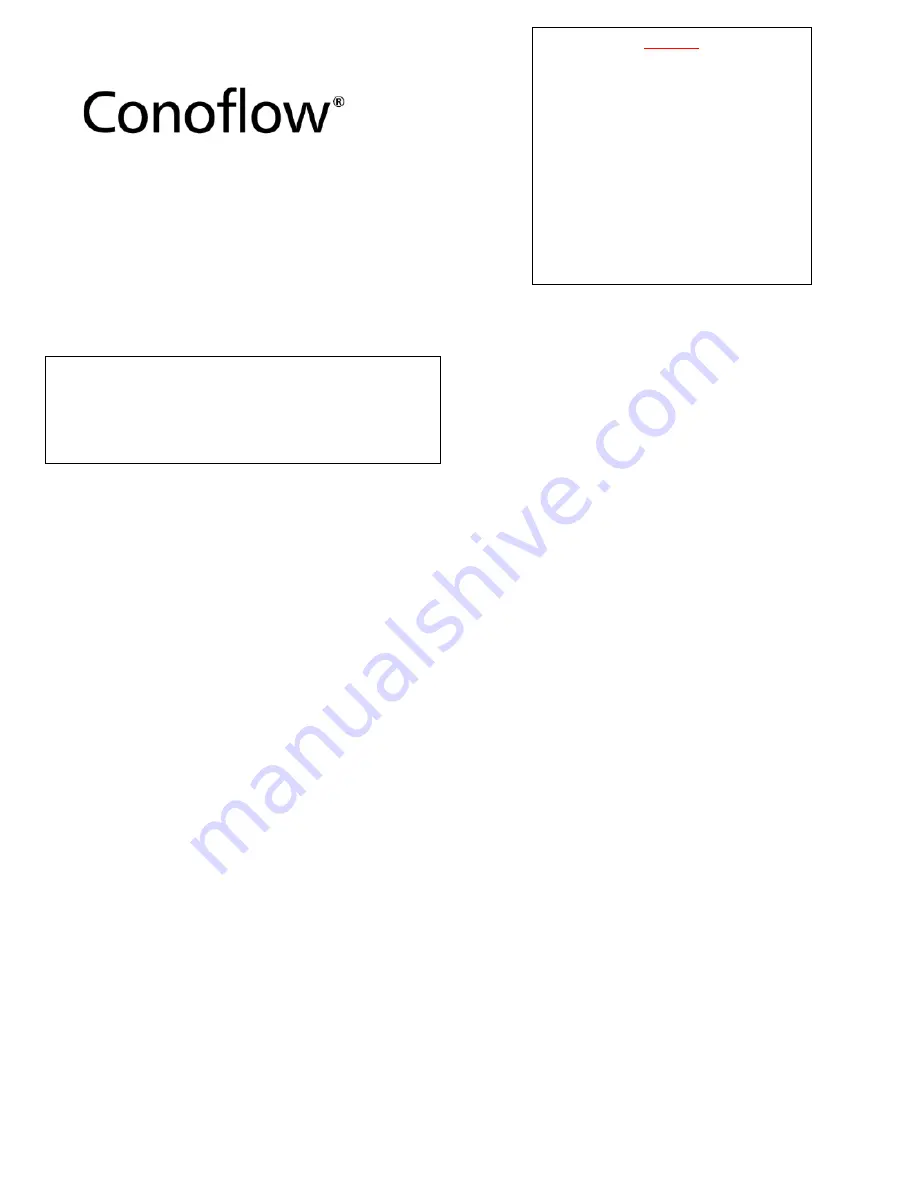
GB50-IOM Rev. 0 8/20
THIS INFORMATION IS SUBJECT TO THE CONTROLS OF THE EXPORT ADMINISTRATION REGULATIONS (EAR). THIS INFORMATION SHALL NOT BE PROVIDED TO
NON-US PERSONS OR TRANSFERRED BY ANY MEANS TO ANY LOCATION OUTSIDE THE UNITED STATES CONTRARY TO THE REQUIREMENTS OF THE EAR.
105 Commerce Way
Westminster, SC 29693
Tel: (864) 647-9521
Fax: (864) 647-9568
INSTRUCTION AND MAINTENANCE MANUAL
GB50 Series Piston Actuator
CAUTION:
These instructions should be read and
understood prior to installation, use, or maintenance.
WARNING
: Forces generated during actuator operation
are significant. Keep clear of moving parts during
actuator operation.
This manual describes the GB50 Series Piston
Actuators. Actuators of various piston diameters,
strokes, and mounting arrangements are available.
These piston actuators are typically equipped with a top
mounted positioner and range (control) spring assembly.
Other configurations are available, including on-off (full
extend / retract) operation, failsafe operation, and
different mounting or lever operation. See sales
literature for these standard offerings.
UNPACKING ACTUATOR
Check for accessory equipment packed with the
actuator. The actuator nameplate will provide necessary
data required for complete identification. Always refer to
actuator model number when ordering spare parts,
conversion parts or accessory equipment.
INSTALLATION
The piston actuator can be mounted in any position. In
most configurations, a regulator and gauge for loading
one side of the piston are mounted and piped. Air supply
should be regulated and filtered.
NOTE: A Conoflow Airpak (filter-regulator) can be
integrally mounted to provide constant regulation and
filtration of air supply to the actuator
.
OPERATION
Normal range of the actuator positioner for full stroke is
3-15 PSI (21-103kPa) (Other ranges, including 3-9 PSI
(21-62 kPa) and 9-15 PSI (62-103 kPa) are available).
Connect the signal input to the connection marked
“INST,” on the positioner. Then connect a supply of
clean, filtered air to the supply connection port to supply
both the positioner and the cushion loading device. The
supply pressure required is a function of the cylinder
diameter and the force required. Air supply up to 100
PSI (690 kPa) can safely be used to insure a reserve of
power and maximum speed. However, for economy of
operation, use the lowest supply pressure with which
satisfactory results can be obtained. The positioner has
been tested, and adjusted for operation with a supply
pressure up to 100 PSI (690 kPa).
ZERO ADJUSTMENT
To check the zero adjustment (preset at factory), set the
instrument output signal at the mid-point of its range (9
Psi (62 kPa) on a 3-15 PSI (21-103 kPa) range), turn
zero adjustment coupling and note the position of the
actuator stem. Continue rotation of the zero adjustment
coupling in the proper direction until the actuator stem is
at the midpoint of stroke. Adjust the instrument output
signal to low and high points in the range and check the
stem position at both ends of the stroke.
If stroke adjustment does not fall within specifications,
refer to the positioner manual for further instructions.
CUSHION LOADING REGULATOR
Fixed cushion loading pressure has been arbitrarily set
at approximately 20 PSI (138 kPa). This pressure may
be adjusted by means of the cushion loading regulator
when higher or lower return forces are required. The
standard regulator supplied can provide settings up to 60
Psi (414 kPa) and as low as 5 PSI (35 kPa).
WARNING
Conoflow’s products are designed and
manufactured using materials and workmanship
required to meet all applicable standards. The use
of these products should be confined to services
specified and/or recommended in the Conoflow
catalogs, instructions, or by Conoflow application
engineers.
To avoid personal injury or equipment damage
resulting from misuse or misapplication of a
product, it is necessary to select the proper
materials of construction and pressure-
temperature ratings which are consistent with
performance requirements.