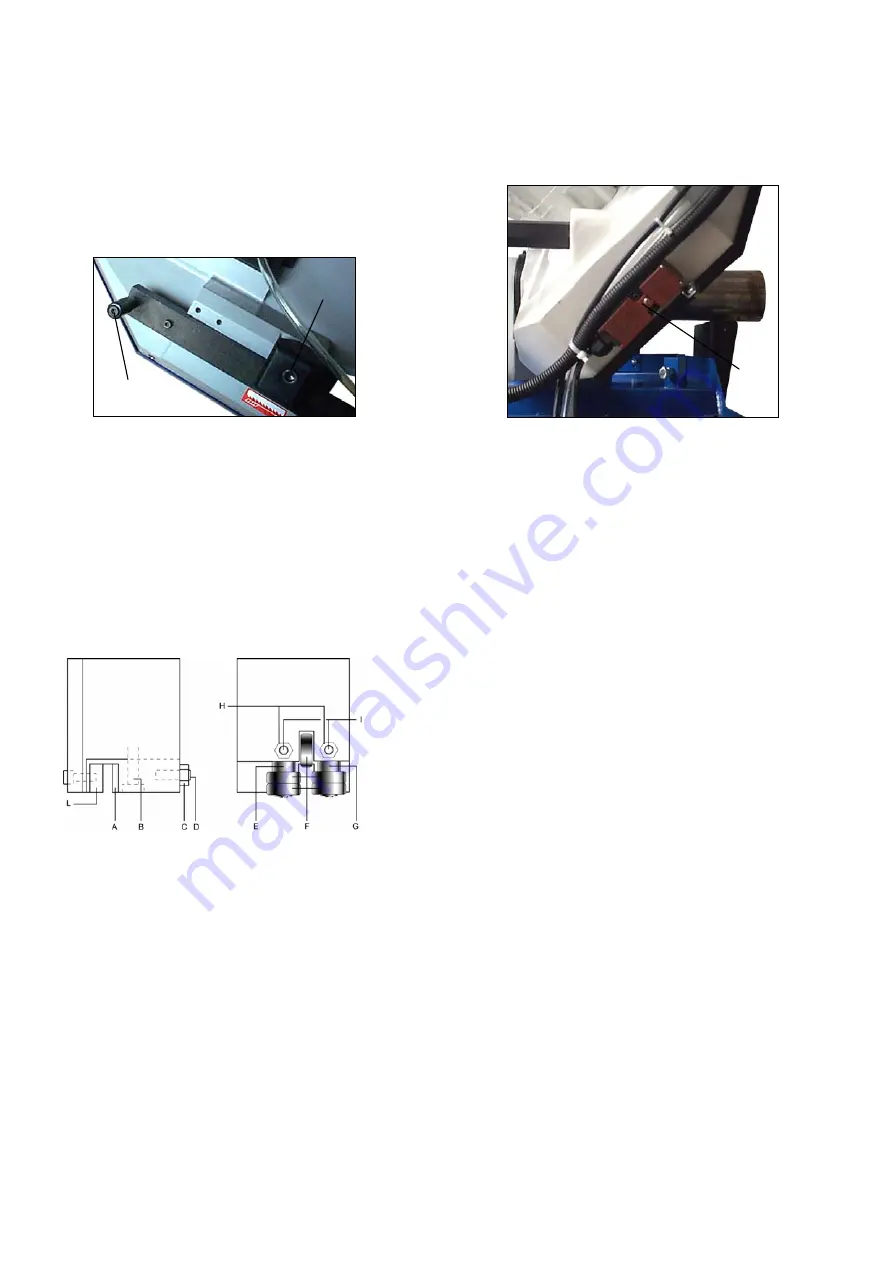
- 7 -
If the tension is set properly, but the microswitch (B)
does not contact or trigger properly, make this
adjustment.
- Loosen the setscrews (D).
- Push the microswitch (B) towards the touch plate (C).
Make sure that the plunger is pressed properly.
- Tighten down the setscrews (D) to secure the
microswitch (B) in place.
5.2 Adjusting the blade guide
- Disconnect the machine from the power source.
- Loosen hex screw (L) on the guide bar clamp.
- Hold the handle (M) and slide blade guide bar so that
the blade guide is as close as possible to the material
without interfering with the cut.
-
Tighten hex screw (L).
-
Reconnect the machine to power source.
Blade guide blocks
The
blade
is
guided
by
means of adjustable pads set in
place during
inspection
as
per
the thickness of the
blade with minimum play
as shown.
When replacing the blade use a
0.9mm
thick
blade
for
which
the
blade
guides
have been pre-set.
For
of
blades of another
thickness,
the
adjustment
should
be
carried
out
as
follows:
- Loosen
nut
(C),
screw
(B) and
loosen
dowel (D)
widening the
passage
between
the
pads.
- Loosen the nuts (H) and the dowels (I) and rotate the
pins (E - G) to widen the passage between the
bearings (F).
- To mount the new blade: place the pad (A) on the
blade, loosening the dowel, allow a play of 0.04 mm
for the sliding of the toothed blade, lock the relative
nut and screw (B), Rotate the pins (E - G) until the
bearings rest against the blade
as
indicated
in
the
figure
and
then
secure
the
dowels
(I) and
nut
(H).
- Make
sure
that
between
the
blade
and
the
upper
teeth of the pad
(L) this
is
at
least
0.2
- 0.3
mm
of
play;
if
necessary, loosen
the
screws
that
fasten the
blocks
and
adjust
accordingly.
BEFORE PERFORMING THE FOLLOWING
OPERATIONS, THE ELECTRIC POWER SUPPLY
AND THE POWER CABLE MUST BE COMPLETELY
DISCONNECTED.
5.3 Changing the blade
To change the blade:
- Lift the saw arm.
- Loosen the blade with the blade tension hand wheel,
remove the blade-guards,
open
the
blade box cover
and
remove
the old
blade
from
the
flywheels
and
the
blade
guide
blocks.
- Place
the
new
blade
in
between
the
blade guide
pads
and
on
the
race
of
the
flywheels.
Check the cutting
direction
of
the
teeth.
- Tension
the
blade.
Check that it is seated
properly
on the
flywheels.
- Replace
and fasten
the
blade guards and
the
flywheel
guard. Check the safety
interlock switch (N)
is activated otherwise the machine will not start.
WARNING:
Always
use
blades
with the same
thickness
as specified
by
this
manual to match the
blade guide’s factory setting;
otherwise,
see
chapter
5.4 Saw frame return stroke-limiting device
It
consists
in
a mechanical
adjustment
system,
mounted
parallel
to
the
saw
frame
rise
cylinder,
to
reduce
the
passive
phases
of the
operating
cycle.
In
other
words
to
eliminate
the
idle
stroke that
takes
place
when
the
size
of
the
part
to
be
cut
is
much smaller
than
the
maximum
cutting
capacity.
Practically,
you
adjust
the
starting
position
of
the
blade
in
proximity
of
the
part, independently
of
its
dimensions.
Operate
as
follows:
- Slightly
open
the
flow regulation valve(K).
- Bring
the
blade
as
near
as
10mm
from
the
work piece
with the bow up/bow down switches (C and D).
- Loosen handle (7) to release the adjustable stop (8)
against the limit switch (9).
- Lock the handle (7)
ATTENTION:
- It
is
necessary
to
adjust
the
mechanical
stop
(8)
every time; bring
the
blade
near
the
workpiece
by
means of
bow switch
(D) and
then
start
the
automatic
cutting
cycle (F) which
will
begin
operation from
this
position
of
the
blade.
M
L
N