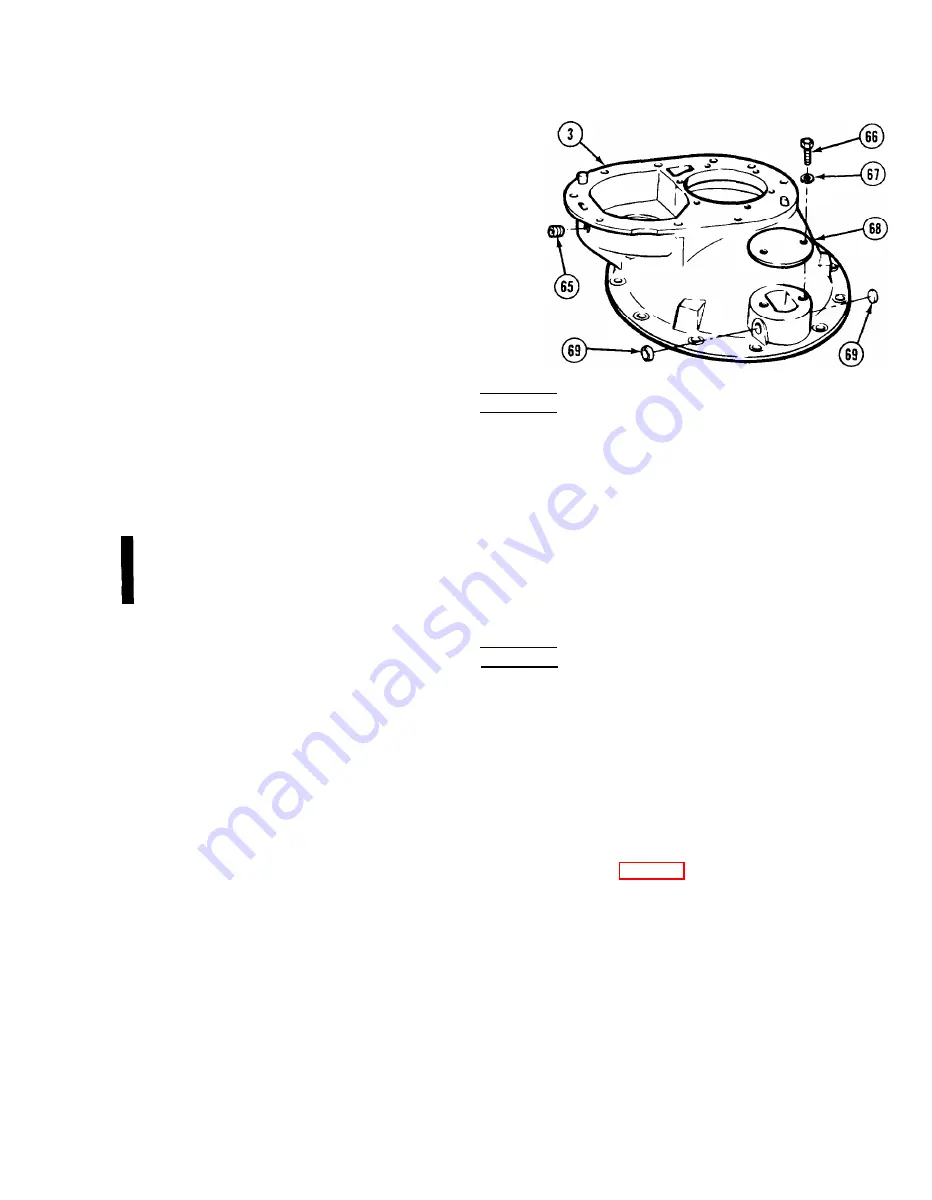
TM 9-2320-279-34-1
Axles No. 1 and No. 2 Maintenance Instructions (Cont)
(48)
Remove filler plug (65) from
differential carrier (3).
(49)
Remove two screws (66),
lockwashers (67), and cover (66).
(50)
Remove two expansion plugs (69).
b. Cleaning/Inspection.
(1)
Clean all metal parts with drycleaning solvent.
(2)
(3)
(4)
(5)
(6)
(7)
(8)
(9)
(10)
(11)
WARNING
Adhesives, solvents, and sealing compounds can burn easily, can give off harmful
vapors, and are harmful to skin and clothing. To avoid injury or death, keep
away from open fire and use in well-ventilated area. If adhesive, solvent, or
sealing compound gets on skin or clothing, wash immediately with soap and
water.
NOTE
If differential carrier housing must be replaced, the new housing will come as
part of a kit. This kit will contain parts not required in this application. Refer to
TM 9-2320-279-24P for proper identification of parts.
WARNING
Compressed air used for cleaning purposes will not exceed 30 psi (207 kPa). Use
only with effective chip guarding and personal protective equipment, goggles,
shield, and gloves.
Use clean, lint-free cloth or compressed air to dry all metal parts, except bearings.
Allow bearings to air dry.
Scrape old sealant from carrier.
Inspect all metal parts for breaks, cracks, and sharp edges.
Inspect machined parts for nicks and burrs.
NOTE
If support bearing is bad, replace support bearing race (para 9-9).
Inspect bearings for loose rollers and cracked or broken races.
Coat bearings with lubricating oil.
Replace differential and output shaft bushings.
If pinion or ring gear is bad, replace both as a matched set.
Inspect dowel pins for breaks or cracks. Replace if damaged.
Change 3
Summary of Contents for 2320-01-097-0248
Page 2: ......
Page 21: ......
Page 22: ......
Page 26: ......
Page 30: ......
Page 38: ...1 1 Figure 1 1 Figure 1 2 TM 9 2320 279 34 1 1 2...
Page 39: ...Figure 1 3 Figure 1 4 TM 9 2320 279 34 1 1 3...
Page 40: ...1 1 Figure 1 5 Figure 1 6 TM 9 2320 279 34 1 1 4...
Page 69: ...TM 9 2320 279 34 1 Troubleshooting Malfunctions Cont Table 2 3 Troubleshooting Cont 2 2 3...
Page 72: ......
Page 75: ...TM 9 2320 279 34 1 Troubleshooting Malfunctions Cont Table 2 3 Troubleshooting Cont 2 27...
Page 77: ...TM 9 2320 279 34 1 Troubleshooting Malfunctions Cont Table 2 3 Troubleshooting Cont 2 28 1...
Page 79: ...TM 9 2320 279 34 1 Troubleshooting Malfunctions Cont Table 2 3 Troubleshooting Cont 2 28 3...
Page 81: ...TM 9 2320 279 34 1 Troubleshooting Malfunctions Cont Table 2 3 Troubleshooting Cont 2 2 8 5...
Page 83: ...TM 9 2320 279 34 1 Troubleshooting Malfunctions Cont Table 2 3 Troubleshooting Cont 2 28 7...
Page 91: ...TM 9 2320 279 34 1 Troubleshooting Malfunctions Cont Table 2 3 Troubleshooting Cont 2 3 5...
Page 93: ...TM 9 2320 279 34 1 Troubleshooting Malfunctions Cont Table 2 3 Troubleshooting Cont 2 3 7...
Page 95: ...TM 9 2320 279 34 1 Troubleshooting Malfunctions Cont Table 2 3 Troubleshooting Cont 2 3 9...
Page 97: ...TM 9 2320 279 34 1 Troubleshooting Malfunctions Cont Table 2 3 Troubleshooting Cont 2 41...
Page 99: ...TM 9 2320 279 34 1 Troubleshooting Malfunctions Cont Table 2 3 Troubleshooting Cont 2 4 3...
Page 101: ...TM 9 2320 279 34 1 Troubleshooting Malfunctions Cont Table 2 3 Troubleshooting Cont 2 4 5...
Page 103: ...TM 9 2320 279 34 1 Troubleshooting Malfunctions Cont Table 2 3 Troubleshooting Cont 2 4 7...
Page 105: ...TM 9 2320 279 34 1 Troubleshooting Malfunctions Cont Table 2 3 Troubleshooting Cont 2 4 9...
Page 109: ...TM 9 2320 279 34 1 Troubleshooting Malfunctions Cont Table 2 3 Troubleshooting Cont 2 5 3...
Page 111: ...TM 9 2320 279 34 1 Troubleshooting Malfunctions Cont Table 2 3 Troubleshooting Cont 2 5 5...
Page 113: ...TM 9 2320 279 34 1 Troubleshooting Malfunctions Cont Table 2 3 Troubleshooting Cont 2 5 7...
Page 115: ...TM 9 2320 279 34 1 Troubleshooting Malfunctions Cont Table 2 3 Troubleshooting Cont 2 5 9...
Page 117: ...TM 9 2320 279 34 1 Troubleshooting Malfunctions Cont Table 2 3 Troubleshooting Cont 2 61...
Page 121: ...TM 9 2320 279 34 1 Troubleshooting Malfunctions Cont Table 2 3 Troubleshooting Cont 2 65...
Page 123: ...TM 9 2320 279 34 1 Troubleshooting Malfunctions Cont Table 2 3 Troubleshooting Cont 2 6 7...
Page 125: ...TM 9 2320 279 34 1 Troubleshooting Malfunctions Cont Table 2 3 Troubleshooting Cont 2 6 9...
Page 127: ...TM 9 2320 279 34 1 Troubleshooting Malfunctions Cont Table 2 3 Troubleshooting Cont 2 71...
Page 129: ...TM 9 2320 279 34 1 Troubleshooting Malfunctions Cont Table 2 3 Troubleshooting Cont 2 7 3...
Page 131: ...TM 9 2320 279 34 1 Troubleshooting Malfunctions Cont Table 2 3 Troubleshooting Cont 2 7 5...
Page 133: ...TM 9 2320 279 34 1 Troubleshooting Malfunctions Cont Table 2 3 Troubleshooting Cont 2 77...
Page 135: ...TM 9 2320 279 34 1 Troubleshooting Malfunctions Cont Table 2 3 Troubleshooting Cont 2 7 9...
Page 139: ...TM 9 2320 279 34 1 Troubleshooting Malfunctions Cont Table 2 3 Troubleshooting Cont 2 8 3...
Page 141: ...TM 9 2320 279 34 1 Troubleshooting Malfunctions Cont Table 2 3 Troubleshooting Cont 2 8 5...
Page 147: ...TM 9 2320 279 34 1 Troubleshooting Malfunctions Cont Table 2 3 Troubleshooting Cont 2 91...
Page 149: ...TM 9 2320 279 34 1 Troubleshooting Malfunctions Cont Table 2 3 Troubleshooting Cont 2 9 3...
Page 151: ...T M 9 2 3 2 2 7 9 3 4 1 Troubleshooting Malfunctions Cont Table 2 3 Troubleshooting Cont 2 9 5...
Page 160: ......
Page 167: ...TM 9 2320 279 34 1 Troubleshooting Malfunctions Cont Table 2 3 Troubleshooting Cont 2 109...
Page 169: ...TM 9 2320 279 34 1 Troubleshooting Malfunctions Cont Table 2 3 Troubleshooting Cont 2 111...
Page 171: ...TM 9 2320 279 34 1 Troubleshooting Malfunctions Cont Table 2 3 Troubleshooting Cont 2 1 1 3...
Page 173: ...TM 9 2320 279 34 1 Troubleshooting Malfunctions Cont Table 2 3 Troubleshooting Cont 2 115...
Page 181: ...TM 9 2320 279 34 1 Troubleshooting Malfunctions Cont Table 2 3 Troubleshooting Cont 2 1 2 3...
Page 183: ...TM 9 2320 279 34 1 Troubleshooting Malfunctions Cont Table 2 3 Troubleshooting Cont 2 1 2 5...
Page 187: ...TM 9 2320 279 34 1 Troubleshooting Malfunctions Cont Table 2 3 Troubleshooting Cont 2 1 2 6 3...
Page 189: ...TM 9 2320 279 34 1 Troubleshooting Malfunctions Cont Table 2 3 Troubleshooting Cont 2 1 2 6 5...
Page 212: ......
Page 231: ...TM 9 2320 279 34 1 Engine Maintenance Instructions Cont 3 1 7...
Page 232: ...3 3 TM 9 2320 279 34 1 Engine Maintenance Instructions Cont 3 1 8...
Page 235: ...TM 9 2320 279 34 1 Engine Maintenance Instructions Cont 3 21...
Page 236: ...3 3 TM 9 2320 279 34 1 Engine Maintaince Instructions Cont 3 22...
Page 237: ...TM 9 2320 279 34 1 Engine Maintenance Instructions Cont 3 2 3...
Page 238: ...3 3 TM 9 2320 279 34 1 E n g i n e M a i n t e n a n c e I n s t r u c t i o n s C o n t 3 2 4...
Page 241: ...TM 9 2320 279 34 1 Engine Maintenance Instructions Cont 3 2 7...
Page 242: ...3 3 TM 9 2320 279 34 1 Engine Maintenance Instructions Cont 3 2 8...
Page 244: ...3 4 TM 9 2320 279 34 1 E n g i n e M a i n t e n a n c e I n s t r u c t i o n s C o n t 3 3 0...
Page 245: ...T M 9 2 3 2 0 2 7 9 3 4 1 Engine Maintenance Instructions Cont 3 31...
Page 248: ...4 2 TM 9 2320 279 34 1 Fuel Sustem Maintenance Instructions Cont 4 2...
Page 249: ...T M 9 2 3 2 0 2 7 9 3 4 1 Fuel System Maintenance Instructions Cont 4 3 4 4 blank...
Page 250: ......
Page 252: ...5 2 T M 9 2 3 2 0 2 7 9 3 4 1 Cooling System Maintenance Instructions Cont 5 2...
Page 253: ...WARNING TM 9 2320 279 34 1 Cooling System Maintenance Instructions Cont 5 3...
Page 254: ...5 2 TM 9 2320 279 34 1 Cooling System Maintenance Instructions Cont 5 4...
Page 257: ...TM 9 2320 279 34 1 Electrical System Maintenance Instructions Cont 6 3...
Page 258: ...6 2 TM 9 2320 279 34 1 Electrical System Maintenance Instructions Cont 6 4...
Page 259: ...TM 9 2320 279 34 1 Electrical System Maintemance Instructions Cont 6 5...
Page 260: ...6 2 TM 9 2320 279 34 1 Electrical System Maintenance Instructions Cont 6 6...
Page 263: ...CAUTION TM 9 2320 279 34 1 Electrical System Maintenance Instructions Cont 6 9...
Page 266: ...6 2 TM 9 2320 279 34 1 Electrical System Maintenance Instructions Cont 6 12...
Page 284: ...6 3 TM 9 2320 279 34 1 Electrical Sustem Maintenance Instructions Cont 6 16...
Page 286: ...6 3 TM 9 2320 279 34 1 Electrical System Maintenance Instructions Cont 6 18...
Page 287: ...TM 9 2320 279 34 1 Electrical System Maintenance Instructions Cont 6 19...
Page 288: ...6 4 TM 9 2320 279 34 1 Electrical System Maintenance Instructions Cont 6 20...
Page 289: ...TM 9 2320 279 34 1 Electrical System Maintenance Instructions Cont 6 21...
Page 290: ...6 4 TM 9 2320 279 34 1 Electrical System Maintenance Instructions Cont 6 22...
Page 291: ...TM 9 2320 279 34 1 Electrical System Maintenance Instructions Cont 6 23...
Page 292: ...6 4 TM 9 2320 279 34 1 Electrical System Maintenance Instructions Cont 6 24...
Page 293: ...WARNING TM 9 2320 279 34 1 Electrical System Maintenance Instructions Cont 6 25...
Page 294: ...6 4 TM 9 2320 279 34 1 Electrical System Maintenance Instructions Cont 6 26...
Page 295: ...TM 9 2320 279 34 1 Electrical System Maintenance Instructions Cont 6 27...
Page 296: ...6 4 TM 9 2320 279 34 1 Electrical System Maintenance Instructions Cont 6 28...
Page 297: ...TM 9 2320 279 34 1 Electrical System Maintenance Instructions Cont 6 29...
Page 298: ...6 4 TM 9 2320 279 34 1 Electrical System Maintenance Instructions Cont 6 30...
Page 299: ...Electrical System Maintenance Instructions Cent TM 9 2320 279 34 1 6 31...
Page 300: ...6 4 TM 9 2320 279 34 1 Electrical System Maintenance Instructions Cont 6 3 2...
Page 301: ...TM 9 2320 279 34 1 Electrical System Maintenance Instructions Cont 6 3 3...
Page 302: ...6 4 TM 9 2320 279 34 1 Electrical System Maintenance Instructions Cont 6 34...
Page 303: ...TM 9 2320 279 34 1 Electrical System Maintenance Instructions Cent 6 3 5...
Page 305: ...T M 9 2 3 2 0 2 7 9 3 4 1 Electrical System Maintenance Instructions Cont 6 3 7...
Page 306: ...6 5 TM 9 2320 279 34 1 Electrical System Maintenance Instructions Cont 6 38...
Page 307: ...6 6 TM 9 2320 279 34 1 Electrical System Maintenance Instructions Cont 6 39...
Page 308: ...6 6 TM 9 2320 279 34 1 Electrical System Maintenance Instructions Cont 6 40...
Page 309: ...6 7 TM 9 2320 279 34 1 Electrical System Maintenance Instructions Cont 6 41...
Page 310: ...6 7 TM 9 2320 279 34 1 Electrical System Maintenance Instructions Cont 6 4 2...
Page 311: ...WARNING TM 9 2320 279 34 1 Electrical System Maintenance Instructions Cont 6 43...
Page 312: ...6 8 TM 9 2320 279 34 1 Electrical System Maintenance Instructions Cont 6 44...
Page 313: ...TM 9 2320 279 34 1 Electrical System Maintenance Instructions Cont 6 4 5...
Page 314: ...6 8 TM 9 2320 279 34 1 Electrical System Maintenance Instructions Cont 6 46...
Page 315: ...TM 9 2320 279 34 1 Electrical System Maintenance Instructions Cont 6 47...
Page 316: ...6 9 TM 9 2320 279 34 1 Electrical System Maintenance Instructions Cont 6 48...
Page 317: ...WARNING TM 9 2320 279 34 1 Electrical System Maintenance Instructions Cont 6 49...
Page 318: ...6 9 TM 9 2320 279 34 1 Electrical System Maintenance Instructions Cont 6 50...
Page 319: ...TM 9 2320 279 34 1 Electrical System Maintenance Instructions Cont 6 51...
Page 320: ...6 9 TM 9 2320 279 34 1 Electrical System Maintenance Instructions Cont 6 52...
Page 321: ...TM 9 2320 279 34 1 Electrical System Maintenance Instructions Cont 6 53...
Page 322: ...6 10 TM 9 2320 279 34 1 Electrical System Maintenance Instructions Cont 6 54...
Page 323: ...6 11 TM 9 2320 279 34 1 Electrical System Maintenance Instructions Cont 6 55...
Page 324: ...6 11 TM 9 2320 279 34 1 Electrical System Maintenance Instructions Cont 6 56...
Page 368: ......
Page 379: ...T M 9 2 3 2 0 2 7 9 3 4 1 Electrical System Maintenance Instructions Cont 6 9 5...
Page 397: ...T M 9 2 3 2 0 2 7 9 3 4 1 Electrical Systems Maintenance Instructions Cont 6 1 1 3...
Page 399: ...T M 9 2 3 2 0 2 7 9 3 4 1 Electrical Systems Maintenance Instructions Cont 6 1 1 5...
Page 400: ...T M 9 2 3 2 0 2 7 9 3 4 1 Electrical Systems Maintenance Instructions Cont 6 1 1 6...
Page 401: ...T M 9 2 3 2 0 2 7 9 3 4 1 Electrical Systems Maintenance Instructions Cont 6 117...
Page 402: ...T M 9 2 3 2 0 2 7 9 3 4 1 Electrical Systems Maintenance Instructions Cont 6 1 1 8...
Page 403: ...T M 9 2 3 2 0 2 7 9 3 4 1 Electrical Systems Maintenance Instructions Cont 6 119...
Page 405: ...T M 9 2 3 2 0 2 7 9 3 4 1 Electrical Systems Maintenance Instructions Cont 6 1 2 1...
Page 409: ...T M 9 2 3 2 0 2 7 9 3 4 1 Electrical System Maintenance Cont 6 122 3...
Page 410: ...T M 9 2 3 2 0 2 7 9 3 4 1 Electrical System Maintenance Cont 6 122 4...
Page 411: ...T M 9 2 3 2 0 2 7 9 3 4 1 Electrical System Maintenance Cont 6 122 5...
Page 412: ...T M 9 2 3 2 0 2 7 9 3 4 1 Electrical System Maintenance Cont 6 122 6...
Page 413: ...TM 9 2320 279 34 1 Electrical System Maintenance Cont 6 1 2 2 7...
Page 414: ...T M 9 2 3 2 0 2 7 9 3 4 1 Electrical System Maintenance Cont 6 122 8...
Page 415: ...T M 9 2 3 2 0 2 7 9 3 4 1 Electrical System Maintenance Cont 6 1 2 2 9...
Page 416: ...T M 9 2 3 2 0 2 7 9 3 4 1 Electrical System Maintenance Cont 6 122 10...
Page 420: ......
Page 421: ...T M 9 2 3 2 0 2 7 9 3 4 1 Electrical System Maintenance Instructions Cont 6 1 2 3...
Page 424: ...T M 9 2 3 2 0 2 7 9 3 4 1 Electrical System Maintenance Cont 6 1 2 6...
Page 425: ...T M 9 2 3 2 0 2 7 9 3 4 1 Electrical System Maintenance Instructions Cont 6 1 2 7...
Page 426: ...T M 9 2 3 2 0 2 7 9 3 4 1 Electrical System Maintenance Instructions Cont 6 1 2 8...
Page 427: ...Electrical System Maintenance Cont T M 9 2 3 2 0 2 7 9 3 4 1 6 1 2 9...
Page 428: ...T M 9 2 3 2 0 2 7 9 3 4 1 Electrical System Maintenance Cont 6 1 3 0...
Page 432: ......
Page 436: ...T M 9 2 3 2 0 2 7 9 3 4 1 Transmission Maintenance Instructions Cont 7 4...
Page 437: ...Transmission Maintenance Instructions Cont T M 9 2 3 2 0 2 7 9 3 4 1 7 5...
Page 438: ...T M 9 2 3 2 0 2 7 9 3 4 1 Transmission Maintenance Instructions Cont 7 6...
Page 441: ...T M 9 2 3 2 0 2 7 9 3 4 1 Transmission Maintenance Instructions Cont 7 9...
Page 442: ...T M 9 2 3 2 0 2 7 9 3 4 1 Transmission Maintenance Instructions Cont 7 10...
Page 444: ......
Page 445: ...T M 9 2 3 2 0 2 7 9 3 4 1 Transmission Maintenance Instructions Cont 7 1 1...
Page 446: ...T M 9 2 3 2 0 2 7 9 3 4 1 Transmission Maintenance Instructions C o n t 7 1 2...
Page 447: ...Transmission Maintenance Instructions T M 9 2 3 2 0 2 7 9 3 4 1 C o n t 7 1 3...
Page 448: ...T M 9 2 3 2 0 2 7 9 3 4 1 Transmission Maintenance Instructions Cont 7 1 4...
Page 449: ...T M 9 2 3 2 0 2 7 9 3 4 1 Transmission Maintenance Instructions Cont 7 1 5...
Page 450: ...T M 9 2 3 2 0 2 7 9 3 4 1 Transmission Maintenance Instructions Cont 7 1 6...
Page 451: ...T M 9 2 3 2 0 2 7 9 3 4 1 Transmission Maintenance Instructions Cont 7 1 7...
Page 452: ...T M 9 2 3 2 0 2 7 9 3 4 1 Transmission Maintenance Instructions Cont 7 18...
Page 455: ...T M 9 2 3 2 0 2 7 9 3 4 1 Transmission Maintenance Instructions Cont 7 2 1...
Page 456: ...T M 9 2 3 2 0 2 7 9 3 4 1 Transmission Maintenance Instructions Cont 7 2 2...
Page 459: ...T M 9 2 3 2 0 2 7 9 3 4 1 Transmission Maintenance Instructions Cont 7 2 5...
Page 460: ...T M 9 2 3 2 0 2 7 9 3 4 1 Transmission Maintenance Instructions Cont 7 2 6...
Page 463: ...T M 9 2 3 2 0 2 7 9 3 4 1 Transmission Maintenance Instructions Cont 7 2 9...
Page 464: ...T M 9 2 3 2 0 2 7 9 3 4 1 Transmission Maintenance Instructions Cont 7 3 0...
Page 467: ...Transmission Maintenance Instructions Cont T M 9 2 3 2 0 2 7 9 3 4 1 7 32 1 7 32 2 blank...
Page 468: ......
Page 469: ...T M 9 2 3 2 0 2 7 9 3 4 1 Transmission Maintenance Instructions Cont 7 3 3...
Page 470: ...T M 9 2 3 2 0 2 7 9 3 4 1 Transmission Maintenance Instructions Cont 7 3 4...
Page 471: ...T M 9 2 3 2 0 2 7 9 3 4 1 Transmission Maintenance Instructions Cont 7 3 5...
Page 475: ...T M 9 2 3 2 0 2 7 9 3 4 1 Transmission Maintenance Instructions Cont 7 3 9...
Page 476: ...T M 9 2 3 2 0 2 7 9 3 4 1 Transmission Maintenance Instructions Cont 7 4 0...
Page 477: ...T M 9 2 3 2 0 2 7 9 3 4 1 Transmission Maintenance Instructions Cont 7 4 1...
Page 478: ...T M 9 2 3 2 0 2 7 9 3 4 1 Transmission Maintenance Instructions Cont 7 4 2...
Page 487: ...TM 9 2320 279 34 1 Transmission Maintenance Instructions Cont 7 5 1...
Page 488: ...TM 9 2320 279 34 1 7 5 2 C h a n g e 2...
Page 493: ...CAUTION TM 9 2320 279 34 1 Transmission Maintenance Instructions Cont 7 57...
Page 494: ...7 9 TM 9 2320 279 34 1 Transmission Maintenance Instructions Cont 7 58...
Page 501: ...CAUTION Transmission Maintenance Instructions Cont TM 9 2320 279 34 1 7 65...
Page 502: ...7 9 TM 9 2320 279 34 1 Transmission Maintenance Instructions Cont 7 6 6...
Page 515: ...TM 9 2320 279 34 1 Transmission Maintenance Instructions Cont 7 7 9...
Page 516: ...7 13 TM 9 2320 279 34 1 Transmission Maintenance Instructions Cent 7 8 0...
Page 522: ......
Page 527: ...7 14 TM 9 2320 279 34 1 Transmission Maintenance Instructions Cont 7 8 9...
Page 528: ...7 14 TM 9 2320 279 34 1 Transmission Maintenance Instructions Cont 7 9 0...
Page 531: ...TM 9 2320 279 34 1 Transmission Maintenance Instructions Cont 7 9 3...
Page 532: ...7 15 TM 9 2320 279 34 1 Transmission Maintenance Instructions Cont 7 9 4...
Page 539: ...CAUTION TM 9 2320 279 34 1 Transmission Maintenance Instructions Cont 7 101...
Page 540: ...7 15 TM 9 2320 279 34 1 Transmission Maintenance Instructions Cont 7 102...
Page 558: ......
Page 561: ...CAUTION T M 9 2 3 2 0 2 7 9 3 4 1 Transmission Maintenance Instructions Cont 7 121...
Page 562: ...7 17 7 18 TM 9 2320 279 34 1 Transmission Maintenance Instructions Cont 7 122...
Page 576: ...7 20 T M 9 2 3 2 0 2 7 9 3 4 1 Transmission Maintenance Instructions Cont 7 136...
Page 600: ......
Page 603: ...T M 9 2 3 2 0 2 7 9 3 4 1 Transfer Case Maintenance Instructions Cont 8 2 1 8 2 2 blank...
Page 604: ......
Page 607: ...T M 9 2 3 2 0 2 7 9 3 4 1 Transfer Case Maintenance Instructions Cont 8 5...
Page 608: ...8 2 TM 9 2320 279 34 1 Transfer Case Maintenance Instructions Cont 8 6...
Page 611: ...TM 9 2320 279 34 1 Transfer Case Maintenance Instructions Cont 8 9...
Page 612: ...8 2 T M 9 2 3 2 0 2 7 9 3 4 1 Transfer Case Maintenance Instructions Cont 8 1 0...
Page 615: ...T M 9 2 3 2 0 2 7 9 3 4 1 Transfer Case Maintenance Instructions Cont 8 1 3...
Page 616: ...8 4 T M 9 2 3 2 0 2 7 9 3 4 1 Transfer Case Maintenance Instructions Cont 8 14...
Page 617: ...TM 9 2320 279 34 1 Transfer Case Maintenance Instructions Cont 8 1 5...
Page 618: ...8 4 TM 9 2320 279 34 1 Transfer Case Maintenance Instructions Cont 8 1 6...
Page 621: ...TM 9 2320 279 34 1 Transfer Case Maintenance Instructions Cont 8 1 9...
Page 622: ...8 4 TM 9 2320 279 34 1 Transfer Case Maintenance Instructions Cont 8 2 0...
Page 625: ...WARNING Transfer Case Maintenance Instructions Cont TM 9 2320 279 34 1 8 23...
Page 626: ...8 4 TM 9 2320 279 34 1 Transfer Case Maintenance Instructions Cont 8 2 4...
Page 633: ...Transfer Case Maintenance Instructions Cont TM 9 2320 279 34 1 8 31...
Page 634: ...8 6 TM 9 2320 279 34 1 Transfer Case Maintenance Instructions Cont 8 32...
Page 637: ...TM 9 2320 279 34 1 Transfer Case Maintenance Instructions Cont 8 3 5...
Page 638: ...8 7 TM 9 2320 279 34 1 Transfer Case Maintenance Instructions Cont 8 3 6...
Page 641: ...TM 9 2320 279 34 1 Transfer Case Maintenance Instructions Cont 8 39...
Page 642: ...8 9 TM 9 2320 279 34 1 Transfer Case Maintenance Instructions Cont 8 4 0...
Page 648: ...T M 9 2 3 2 0 2 7 9 3 4 1 Transfer Case Maintenance Instructions Cont 8 4 6...
Page 657: ...T M 9 2 3 2 0 2 7 9 3 4 1 Transfer Case Maintenance Instructions Cont 8 5 5...
Page 658: ...T M 9 2 3 2 0 2 7 9 3 4 1 Transfer Case Maintenance Instructions Cont 8 5 6...
Page 665: ...T M 9 2 3 2 0 2 7 9 3 4 1 Axles No 1 and No 2 Maintenance Instructions Cont 9 7...
Page 666: ...T M 9 2 3 2 0 2 7 9 3 4 1 Axles No 1 and No 2 Maintenance Instructions Cont 9 8...
Page 667: ...T M 9 2 3 2 0 2 7 9 3 4 1 Axles No 1 and No 2 Maintenance Instructions Cont 9 9...
Page 671: ...T M 9 2 3 2 0 2 7 9 3 4 1 Axles No 1 and No 2 Maintenance lnstructions Cont 9 1 3...
Page 674: ......
Page 677: ...T M 9 2 3 2 0 2 7 9 3 4 1 Axles No 1 and No 2 Maintenance Instructions Cont 9 1 7...
Page 678: ...9 6 T M 9 2 3 2 0 2 7 9 3 4 1 Axles No 1 and No 2 Maintenance Instructions Cont 9 1 8...
Page 682: ......
Page 685: ...T M 9 2 3 2 0 2 7 9 3 4 1 Axles No 1 and No 2 Maintenance lnstructions Cont 9 2 3...
Page 686: ...T M 9 2 3 2 0 2 7 9 3 4 1 Axles No 1 and No 2 Maintenance Instructions Cont 9 2 4...
Page 689: ...T M 9 2 3 2 0 2 7 9 3 4 1 Axles No 1 and No 2 Maintenance Instructions Cont 9 2 7...
Page 690: ...9 9 T M 9 2 3 2 0 2 7 9 3 4 1 Axles No 1 and No 2 Maintenance Instructions Cont 9 28...
Page 691: ...T M 9 2 3 2 0 2 7 9 3 4 1 Axles No 1 and No 2 Maintenance lnstructions Cont 9 2 9...
Page 692: ...9 9 T M 9 2 3 2 0 2 7 9 3 4 1 Axles No 1 and No 2 Maintenance Instructions Cont 9 3 0...
Page 693: ...T M 9 2 3 2 0 2 7 9 3 4 1 Axles No 1 and No 2 Maintenance Instructions Cont 9 3 1...
Page 694: ...T M 9 2 3 2 0 2 7 9 3 4 1 Axles No 1 and No 2 Maintenance Instructions Cont 9 3 2...
Page 695: ...T M 9 2 3 2 0 2 7 9 3 4 1 Axles No 1 and No 2 Maintenance Instructions Cont 9 33...
Page 696: ...T M 9 2 3 2 0 2 7 9 3 4 1 Axles No 1 and No 2 Maintenance Instructions Cont 9 3 4...
Page 700: ......
Page 703: ...T M 9 2 3 2 0 2 7 9 3 4 1 Axles No land No 2 Maintenance lnstructions Cont 9 3 9...
Page 704: ...T M 9 2 3 2 0 2 7 9 3 4 1 Axles No 1 and No 2 Maintenance Instructions Cont 9 4 0...
Page 705: ...T M 9 2 3 2 0 2 7 9 3 4 1 Axles No 1 and No 2 Maintenance Instructions Cont 9 4 1...
Page 706: ...T M 9 2 3 2 0 2 7 9 3 4 1 Axles No 1 and No 2 Maintenance Instructions Cont 9 4 2...
Page 707: ...T M 9 2 3 2 0 2 7 9 3 4 1 Axles No 1 and No 2 Maintenance Instructions Cont 9 4 3...
Page 708: ...9 11 TM 9 2320 279 34 1 Axles No 1 and No 2 Maintenance Instructions Cont 9 44...
Page 709: ...T M 9 2 3 2 0 2 7 9 3 4 1 Axles No 1 and No 2 Maintenance lnstructions Cont 9 4 5...
Page 710: ...T M 9 2 3 2 0 2 7 9 3 4 1 Axles No 1 and No 2 Maintenance Instructions Cont 9 4 6...
Page 711: ...T M 9 2 3 2 0 2 7 9 3 4 1 Axles No 1 and No 2 Maintenance Instructions Cont 9 4 7...
Page 712: ...T M 9 2 3 2 0 2 7 9 3 4 1 Axles No 1 and No 2 Maintenance Instructions Cont 9 4 8...
Page 713: ...TM 9 2320 279 34 1 Axles No 1 and No 2 Maintenance lnstructions Cont 9 49...
Page 714: ...9 11 T M 9 2 3 2 0 2 7 9 3 4 1 Axles No 1 and No 2 Maintenance Instructions Cont 9 5 0...
Page 715: ...T M 9 2 3 2 0 2 7 9 3 4 1 Axles No 1 and No 2 Maintenance Instructions Cont 9 5 1...
Page 716: ...TM 9 2320 279 34 1 Axles No 1 and No 2 Maintenance Instructions Cont 9 5 2...
Page 717: ...T M 9 2 3 2 0 2 7 9 3 4 1 Axles No 1 and No 2 Maintenance Instructions Cont 9 5 3...
Page 718: ...9 11 T M 9 2 3 2 0 2 7 9 3 4 1 Axles No 1 and No 2 Maintenance lnstructions Cont 9 5 4...
Page 719: ...T M 9 2 3 2 0 2 7 9 3 4 1 Axles No 1 and No 2 Maintenance lnstructions Cont 9 5 5...
Page 721: ...T M 9 2 3 2 0 2 7 9 3 4 1 Axles No 1 and No 2 Maintenance Instructions Cont 9 57...
Page 722: ...T M 9 2 3 2 0 2 7 9 3 4 1 Axles No 1 and No 2 Maintenance Instructions Cont 9 5 8...
Page 723: ...T M 9 2 3 2 0 2 7 9 3 4 1 Axles No 1 and No 2 Maintenance Instructions Cont 9 5 9...
Page 725: ...T M 9 2 3 2 0 2 7 9 3 4 1 Axles No 1 and No 2 Maintenance Instructions Cent 9 6 1...
Page 726: ...T M 9 2 3 2 0 2 7 9 3 4 1 Axles No 1 and No 2 Maintenance Instructions Cont 9 6 2...
Page 727: ...T M 9 2 3 2 0 2 7 9 3 4 1 Axles No 1 and No 2 Maintenance Instructions Cont 9 6 3...
Page 728: ...T M 9 2 3 2 0 2 7 9 3 4 1 Axles No 1 and No 2 Maintenance Instructions Cont 9 6 4...
Page 731: ...T M 9 2 3 2 0 2 7 9 3 4 1 Axles No 1 and No 2 Maintenance Instructions Cont 9 6 7...
Page 732: ...9 12 T M 9 2 3 2 0 2 7 9 3 4 1 Axles No 1 and No 2 Maintenance Instructions Cont 9 6 8...
Page 733: ...T M 9 2 3 2 0 2 7 9 3 4 1 Axles No 1 and No 2 Maintenance Instructions Cont 9 69...
Page 734: ...T M 9 2 3 2 0 2 7 9 3 4 1 Axles No 1 and No 2 Maintenance Instructions Cont 9 7 0...
Page 735: ...T M 9 2 3 2 0 2 7 9 3 4 1 Axles No land No 2 Maintenance lnstructions Cont 9 71...
Page 736: ...TM 9 2320 279 34 1 9 72...
Page 758: ......
Page 774: ......
Page 775: ...T M 9 2 3 2 0 2 7 9 3 4 1...
Page 776: ......
Page 777: ...TM 9 2320 279 34 1...
Page 778: ......
Page 779: ...TM 9 2320 279 34 1...
Page 780: ...PIN 062143 000...