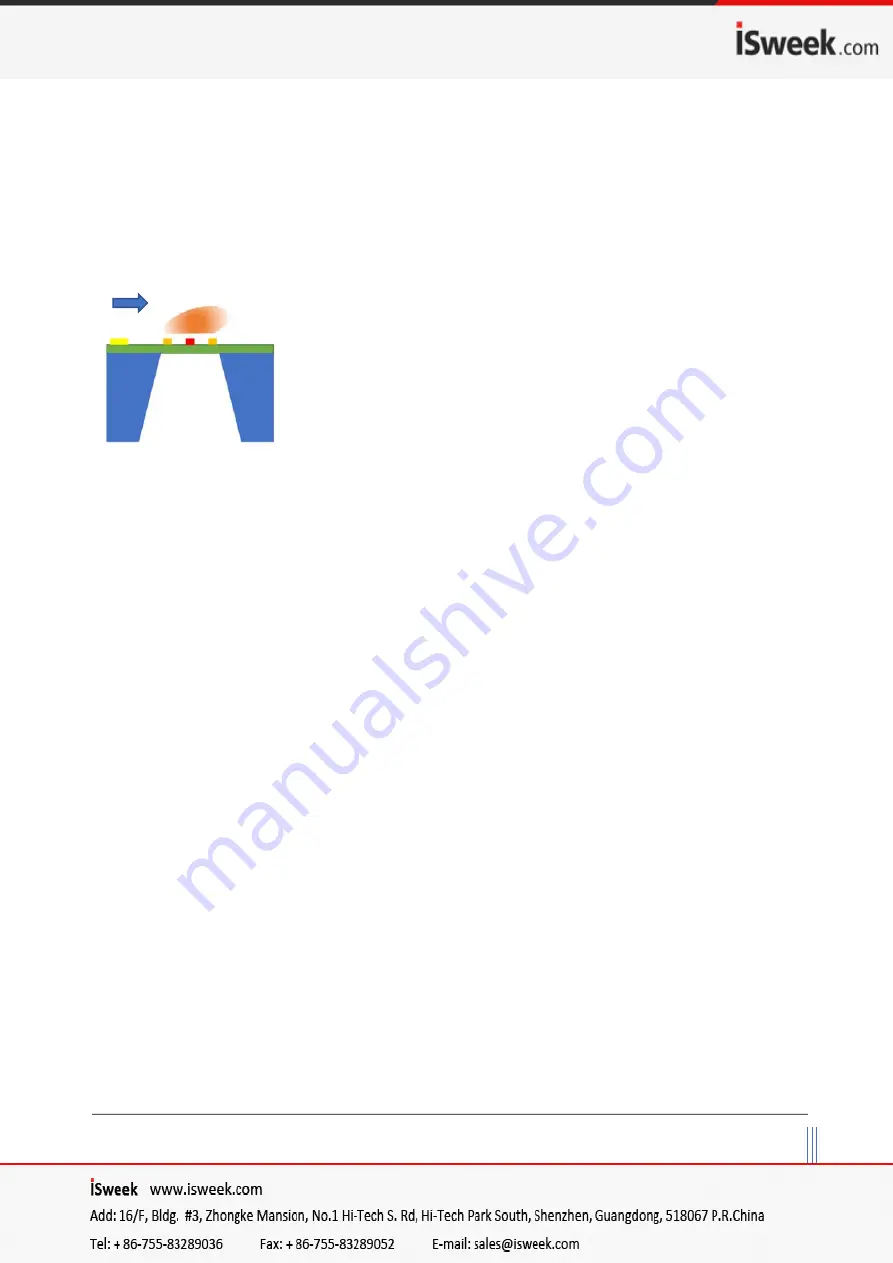
MF5700
User
Manual
31
|
P a g e
8.
Technical
notes
for
the
product
performance
8.1
Measurement
principle
The
products
utilize
the
Company’s
proprietary
micro
‐
machined
(MEMS)
thermal
calorimetric
sensing
technology.
A
thermal
signal
generator
(microheater)
is
placed
on
a
thermally
isolated
membrane
where
two
thermistors
are
placed
symmetrically
concerning
the
microheater.
The
flowing
fluid
carries
away
the
heat
from
the
microheater
causing
a
re
‐
distribution
of
the
temperature
field
which
is
registered
by
the
thermistors.
The
amount
of
heat
carried
by
the
flowing
fluid
is
dependent
on
the
fluid’s
mass
as
well
as
its
thermal
properties.
By
precisely
gauging
the
changing
of
the
temperature
field
with
a
metrological
reference
standard,
the
fluid’s
mass
flow
rate
can
be
established
and
reproduced.
After
the
circuitry
temperature
compensation,
and
with
the
proper
design
of
the
MEMS
sensing
chip
by
adding
the
pressure
balancer
that
allows
the
flatness
of
the
membrane
at
various
fluidic
pressure
conditions.
the
calorimetric
thermal
sensing
will
guarantee
a
pressure
and
temperature
independent
mass
flow
data
acquisition.
The
MEMS
technology
also
allows
the
mass
production
of
the
sensing
elements
that
significantly
reduces
the
cost
compared
to
a
traditional
thermal
mass
flow
sensing
element.
It
enables
the
current
offer
with
superior
value
to
the
users.
For
additional
information,
please
refer
to
the
company’s
US
patents
and
other
publications
made
available
to
the
public.
8.2
Precautions
for
the
best
performance
of
the
product
8.2.1
Comparison
with
a
third
party
reference
meter
It
is
very
common
that
a
user
may
compare
the
data
from
the
product
with
a
third
‐
party
reference
meter,
and
in
many
cases,
there
could
be
some
discrepancies.
When
performing
such
a
comparison,
please
note
that
the
reference
meter
should
have
a
better
‐
specified
accuracy
(about
1/3
of
the
product),
and
pay
special
attention
to
the
differences
in
the
reading
accuracy
and
full
‐
scale
accuracy.
A
full
scale
accuracy
=
reading
accuracy
x
(full
scale
flow
rate/
set
point
(current)
flow
rate)
Figure
8.1.
Measurement
approach
illustration.