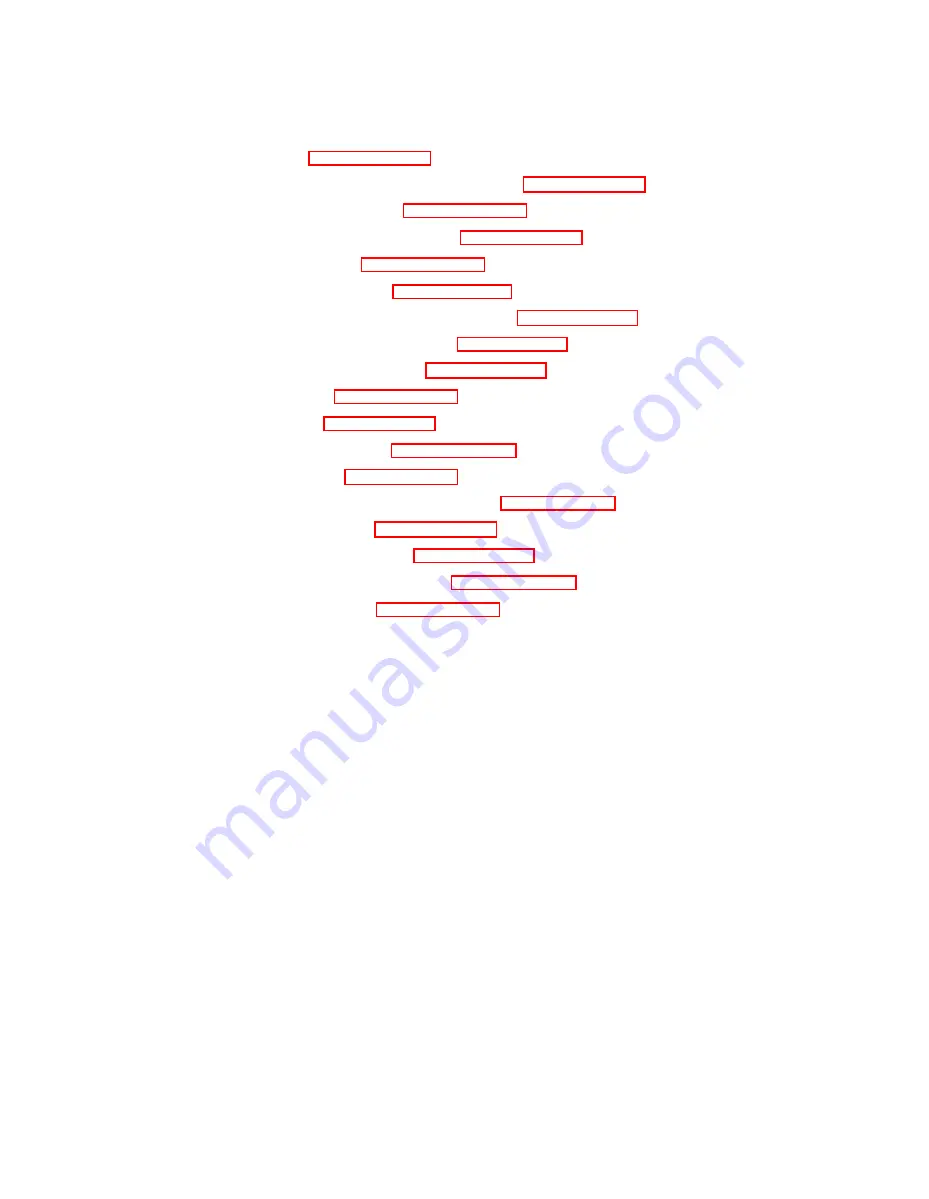
ARMY TM 9-2815-254-24
AIR FORCE TO 36G1-94-2
i.
Install oil pan, refer to paragraph 3-17.3.
j.
Install cylinder head assembly and Push rods, refer to paragraph 3-27-6.
k.
install rocker arm assembly, refer to paragraph 3-26.5.
I.
install intake and exhaust manifolds, refer to paragraph 3-21.3.
m. Install PCV assembly, refer to paragraph 3-20.3.
n.
Install fuel injection pump, refer to paragraph 3-11.6.
o.
install front gear cover and crankshaft pulley, refer to paragraph 3-25.3.
p.
Time and adjust fuel injection pump, refer to paragraph 3-13.
q.
Install fuel injectors and piping. refer to paragraph 3-10.7.
r.
Install glow plugs, refer to paragraph 3-22.4.
s.
Install fuel filter, refer to paragraph 3-9.4.
t.
Install oil filter and piping, refer to paragraphs 3-15.4 and 3-16.2.
u.
Install water pump, refer to paragraph 3-7.4.
v.
Install thermostat housing with thermostat, refer to Paragraph 3-6.4.
w.
Install starter assembly, refer to paragraph 3-23.6.
x.
Install alternator and fan belt, refer to paragraph 3-24.5.
y.
Adjust valves/rocker arm assembly, refer to paragraph 3-26.6.
z.
Install rocker arm cover, refer to Paragraph 3-26.5.
aa. Fill engine with proper oil and coolant, refer to end item maintenance manual.
ab. Perform normal standard engine performance checks.
3-15
Summary of Contents for C-240PW-28
Page 2: ......
Page 4: ......
Page 16: ......
Page 26: ......
Page 46: ...ARMY TM 9 2815 254 24 AIR FORCE TO 38G1 94 2 FIGURE 3 2 Water Pump 3 20...
Page 49: ...ARMY TM 9 2815 254 24 AIR FORCE TO 38G1 94 2 FIGURE 3 3 Fuel Filter Assembly 3 23...
Page 52: ...ARMY TM 9 2815 254 24 AIR FORCE TO 38G1 94 2 FIGURE 3 4 Fuel lnjectors and Piping 3 26...
Page 60: ...ARMY TM 9 2815 254 24 AIR FORCE TO 38G1 94 2 FIGURE 3 7 Fuel Feed Pump and Timer Assembly 3 34...
Page 61: ...ARMY TM 9 2815 254 24 AIR FORCE TO 38G1 94 2 FIGURE 3 8 Fuel Injection Pump Assembly 3 35...
Page 82: ...ARMY TM 9 2815 254 24 AlR FORCE TO 36G1 94 2 TABLE 3 1 Fuel Pump Test Specifications 3 56...
Page 98: ...ARMY TM 9 2815 254 24 AIR FORCE TO 38G1 94 2 FIGURE 3 39 Oil Piping 3 72...
Page 106: ...ARMY TM 9 2815 254 24 AIR FORCE TO 38G1 94 2 FIGURE 3 44 PCV Assembly 3 80 Change 2...
Page 109: ...ARMY TM 9 2815 254 24 AIR FORCE TO 38G1 94 2 FIGURE 3 45 Intake and Exhaust Manifolds 3 83...
Page 122: ...ARMY TM 9 2815 264 24 AIR FORCE TO 38G1 94 2 FIGURE 3 49 Alternator Assembly 3 96 Change 2...
Page 126: ...ARMY TM 9 2815 254 24 AIR FORCE TO 38G1 94 2 FIGURE 3 50 Front Gear Cover 3 100...
Page 129: ...ARMY TM 9 2815 254 24 AIR FORCE TO 38G1 94 2 FIGURE 3 52 Rocker Covet and Arms 3 103...
Page 137: ...ARMY TM 9 2815 254 24 AIR FORCE TO 38G1 94 2 FIGURE 3 60 Cylinder Head Assembly 3 111...
Page 185: ...ARMY TM 9 2815 254 24 AIR FORCE TO 38G1 94 2 FIGURE 3 107 Flywheel and Housing 3 159...
Page 198: ......
Page 210: ......
Page 214: ......
Page 216: ...ARMY TM 9 2815 254 24 AIR FORCE TO 38G1 94 2 Section 111 MAINTENANCE LEVELTD PARAGRAPHS...
Page 220: ......
Page 221: ......
Page 222: ......
Page 224: ......
Page 225: ......
Page 226: ......
Page 227: ......
Page 228: ......
Page 229: ......
Page 230: ......
Page 231: ......
Page 232: ......
Page 233: ......
Page 234: ...PIN 071752 002...