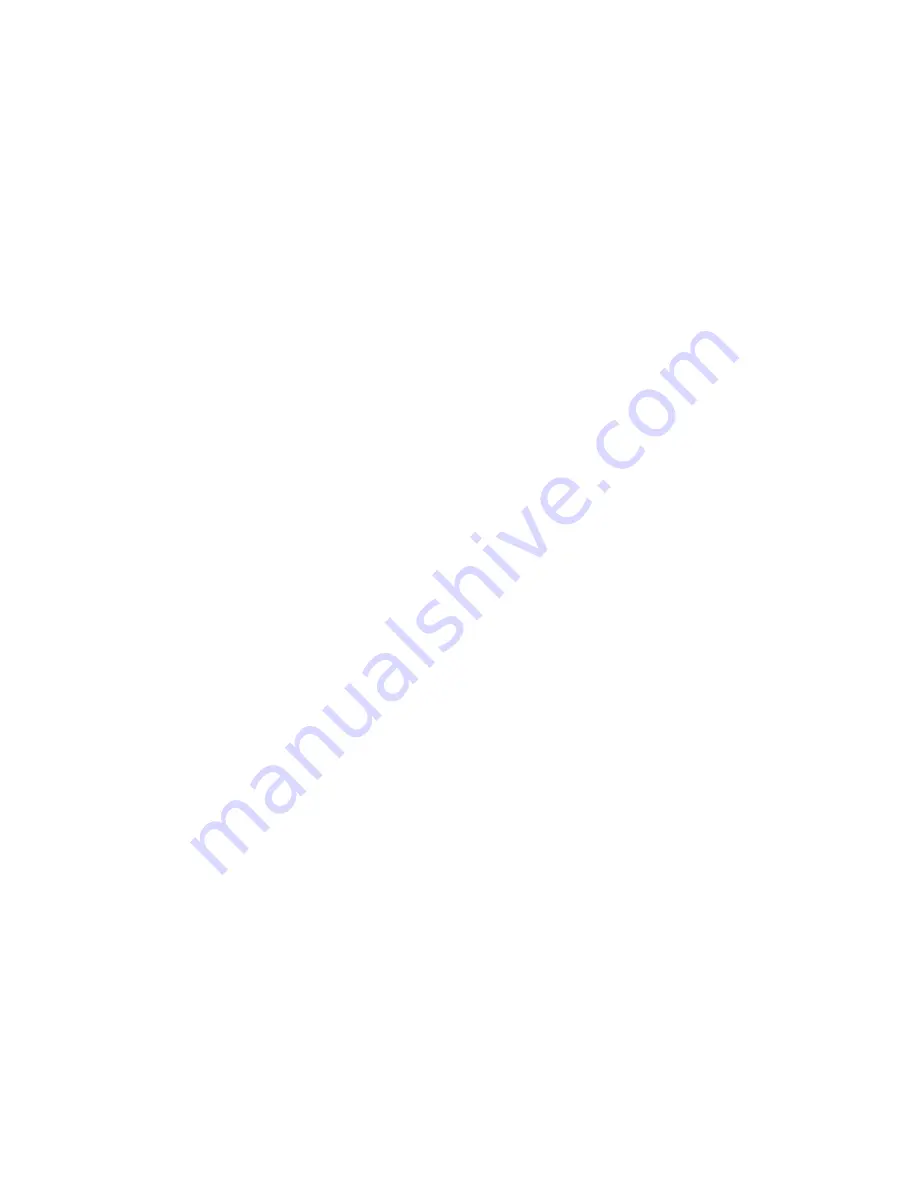
Copyright 2005 ISC Technologies
4.2.2.4 Fix Bias Supply
At P10-4, a 0.64 and 0.05 Vdc bias power supply is produced by QA1B, QA1D, QA1E, and
Q5. This bias voltage is used to bias some of the power amplifier’s driver transistors.
4.2.3 RF Power Detection
The rectified RF signals (RF in, forward RF output, and reflected RF output) provided by
the power amplifier’s directional coupler and input detector are processed to indicate the
power amplifier’s status.
The RF levels are buffered and compared by U3 and U7. See Section 6.2.2, Low and High
Power Adjust, for setting the comparator’s reference voltage level. The forward RF output
signal is fed to US.
The linear bar graph gives an approximation of the power amplifier’s output RF power. The
indication range of bar graph LED’s Dl1 to D20 is from 10% to 100% of the power
amplifier’s RF output. Resistor R48 is used to adjust the bar graph. One of ten jumpers (JR
12 to JR2I) is used to set the relative low forward RF output; a logic high at U2’ s pin 5
indicates a relative low RF level detected. The second jumper (from JR2 to JRI 1) is select-
ed for turning on the fan whenever output power is detected above a threshold level (about
20%).
4.2.4 Status Indication and Alarm
The power on LED D7, and RF IN LED D8, are green. LED D8 indicates the input status of
the power amplifier. LED D8 is turned on whenever 50% of rated exciter power is detected.
The level of triggering D8 is adjusted by R50.
The high reflection output LED D9, and overheat LED D10, are red. When these LED’s are
illuminated, this indicates a problem in the power amplifier. LED D9 is latched by Q1 where
the reflected level is detected above a certain level (30% of rated power amplifier power)
for approximately 10 ms. LED D9 is disabled only by resetting the latch (U1 and the NOR
RS flip flop). It is reset on the application or removal of PTT (or by a transition from low to
high or high to low power) if the alarm condition has been corrected.
The temperature sensor, mounted on the heatsink, will switch on Q2 and LED D10 when it
detects the ambient temperature of the heat sink is above the rated temperature level (set
by R14 and R28 or R51). There is about 10oC hysteresis built into the temperature sensor
circuitry to ensure the power amplifier is cooled down before the next transmission. The
overheat signal sent by the temperature sensor is latched by U1, and sends an alarm
signal to the system through P10-11. The overheat alarm will only be reset when the heat
sink is cool enough for the power amplifier’s next transmission.
The alarm signal is fed to driver regulator switch Q3, and it will disable the power amplifier
(JR26 installed) or switch the power amplifier to low power (JR27 installed) as long as the
alarm condition is present. On the other hand, it is desirable to disable the alarm signal,
and enable the power amplifier when a new antenna system is set up at a site. This can be
achieved by removing JR26 or JR27 (which ever is installed).
Note
Remember to replace JR26 or JR27 (whichever was installed) after theantenna system is
set up. The power amplifier may be shutdown remotely if desired, by supplying 5 Vdc to pin
14 on connector DB15.