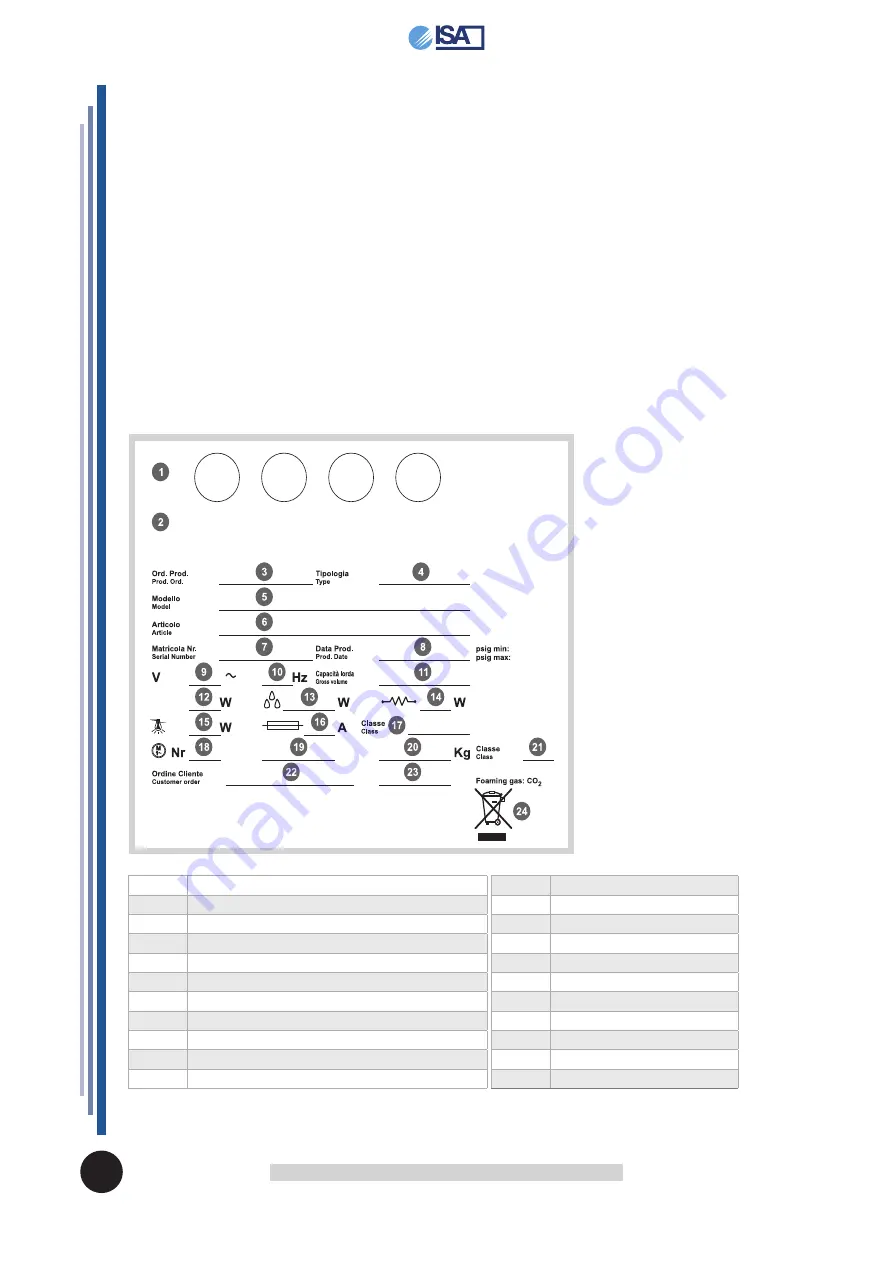
15
ISETTA
USE AND MAINTENANCE MANUAL
428000372
237
EN
6. EQUIPMENT DESCRIPTION
6.1 Assembled structure
The equipment comprises a single furniture on which all the functional devices needed to make it a
professional product effi cient for its intended use are assembled.
The equipment comprises:
- Insulated structure in ecological polyurethane
- Cooling system
- Electronic control panel
- Electrical system
- Built-in hermetic condensing unit
- Lighting
- Rear pivoting methacrilate panel system on operator side
- 4 pivoting whells
6.2 Identifi cation
1
Symbols of Compliance
2
Manufacturer's address
3
Production Order
4
Type
5
Model Name
6
Article
7
Serial Number
8
Production Date
9 - 10
Power Supply Voltage and Frequency
11
Gross Capacity
12
Absorption at Rated Capacity
13
Absorption during Defrosting
14
Absorption of Heating Elements
15
Lamp Power
16
Fuse Value
17
Climate Class
18
Number of Motors
19
Type of Coolant
20
Amount of Coolant
21
Safety Class
22 - 23
Customer order
24
WEEE Mark
Summary of Contents for Isetta 12R LX
Page 32: ......