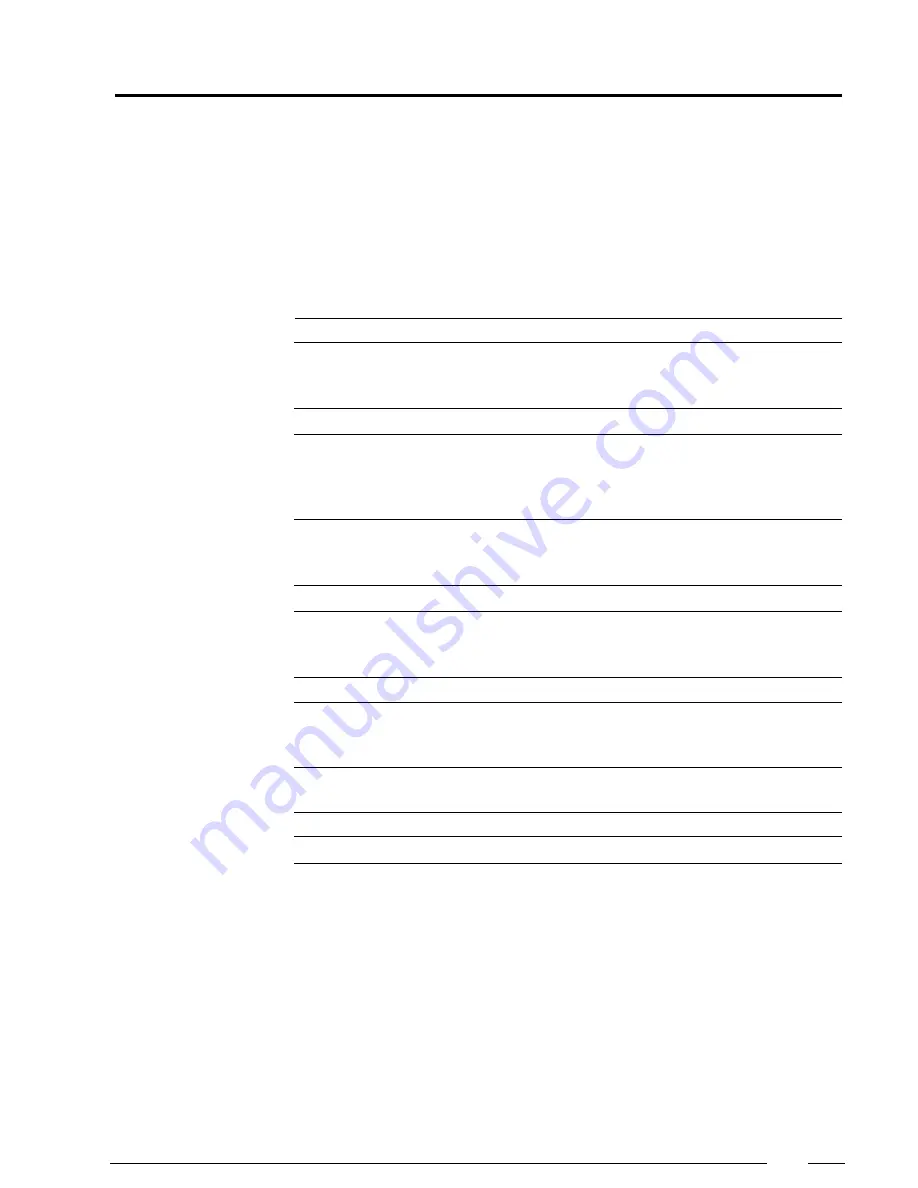
16
5
Technical remarks
Program time (Machine with CAM-timer)
Remark
In the programs 1 & 2 the pre-wash is installable on 430" or 630" and the main wash installable
on 9' or 12',according to the cabling.
Every time the machine is out of balance during the spin 1 minute is added to the program. (See
electronical repetition system)
Code 10.1126 - 220 V (50Hz with brown CAM-timer)
There are several possibilities according to cabling, microprocessor, type of heating, tempe-
rature control, water level control, etc.... For your information you can find the details of the
programs for a machine with standard programs, boiler fed (
without temperature control nor
water level controls
).
1
2
3
4
5
Hot
Warm
Synth. 1
Synth. 2
Wool
water inlet
cold+warm
cold+warm
cold+warm
cold+warm
cold
pre-wash
630"
630"
430"
630"
630"
water drain
130"
130"
130"
130"
1'30"
spin
230"
230"
230"
130"
130"
water inlet
warm
33% cold+
50%cold+
66% warm
50%warm
main wash
12'
12'
9'
water drain
130"
130"
130"
water inlet
cold
cold
cold
cold
cold
rinse1
2'
2'
2'
2'
2'
water drain
130"
130"
130"
130"
130"
spin
230"
230"
130"
130"
130"
water inlet
cold
cold
cold
cold
cold
rinse
2
2'
2'
2'
2' 2'
water drain
130"
130"
130"
130"
130"
spin
230"
230"
130"
130"
130"
water inlet
cold
cold
cold
cold
cold
rinse 3
230"
230"
230"
230"
230"
water drain
130"
130"
130"
130"
130"
low spin
250"
250"
250"
250"
250"
high spin
440"
440"
delay
30"
30"
30"
30"
30"
tumble
30"
30"
30"
30"
30"
total
4830"
4830"
3650"
2720"
2720"