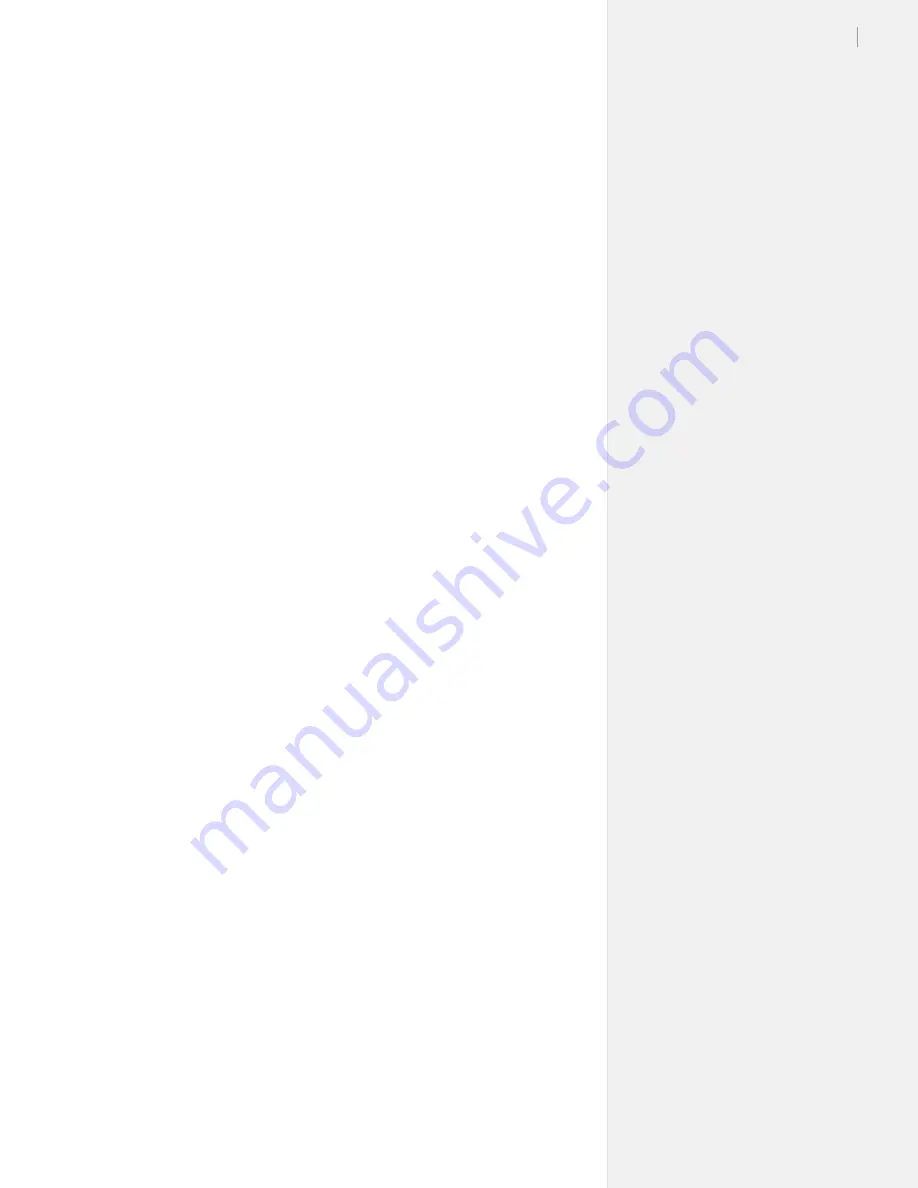
37
Chapter 2: Operation
5.
Lower
Acceleration
. Using the Ioline
Control Center
, set
Accel-
eration
to
0.5 g
or less. Lower acceleration will help with overall
accuracy, especially in the transition between
Frames
.
6.
Use
Autoloop
.
Autoloop
will gently pull a set amount of mate-
rial from the roll. This helps the material feed into the cutter
more accurately and keeps it from “jerking” from the roll.
Autoloop
also helps to set up the drive track in the backing of
the material, which helps keep the material aligned.
Autoloop
is enabled in the
Control Center
. Set
Autoloop
to
ON
and set
the
Loop Size
to the default of
30 inches
. Setting the
Panel
Size
in the design making software to the same length as the
Loop Size
might help tracking accuracy. If
Autoloop
is
OFF
,
maintain a service loop of material behind the cutter to prevent,
“jerking,” material from the roll.
7.
Speed
. Set the
Speed
knob to
50 percent or less
. Moving the
material at a slower speed helps to keep it more stable and
prevents it from kinking or buckling.
8.
Force
and
Blade Depth
. Incorrect cutting
Force
and
Blade
Depth
can cause misalignment problems over the range of a
long plot. If the
Force
is too high, the material may skew. If the
Blade Depth
is set too deep, it could cut all the way through
the material and/or cause the material to become jammed un-
der the blade.
9.
Let the software help. Use the
Automatic Sorting, Ordering or
Contour Ordering
feature in the design software (some soft-
ware programs automatically handle this process). This will
reduce the number of time consuming back and forth and side
to side movements. Wear on the material backing (as well as
the material itself) is decreased, which will improve tracking.
The more complex the file, the more difficult the problem.
10. Use the
Paneling
feature in the design software.
Paneling
will
restrict the length of any X-axis move. Ioline suggests a
Panel
Size
of
10
to
20 inches
. With most design making software,
the
Paneling
feature allows the placement of a panel between
characters.
Cutting Small Characters (Under
1
/
4
-in.)
For cutting small characters or intricate detail in various material, it
is necessary for the cutter to be calibrated properly and to make sure
the pinchwheels are spaced correctly. Also, some of the system set-
tings should be adjusted to achieve more accurate detailed cutting.
This is done by making changes in the Ioline
Control Center
and by
adjusting the dial controls on the front panel. The following is a list
of adjustments that should be made:
1.
Lower
Force
. The lowest blade force possible is the best for
small, detailed cutting. Start by making test cuts with
one
quarter
Force
. Gradually increase the
Force
until the material is
completely cut.
2.
Slower
Speed
. The
Speed
knob should be set halfway or less.
3.
Foot Adjustment
. After setting the lowest cutting
Force
, adjust
the
Foot
downward until the cut is not complete, then back
it up just enough to get a complete cut. Since some
Force
is