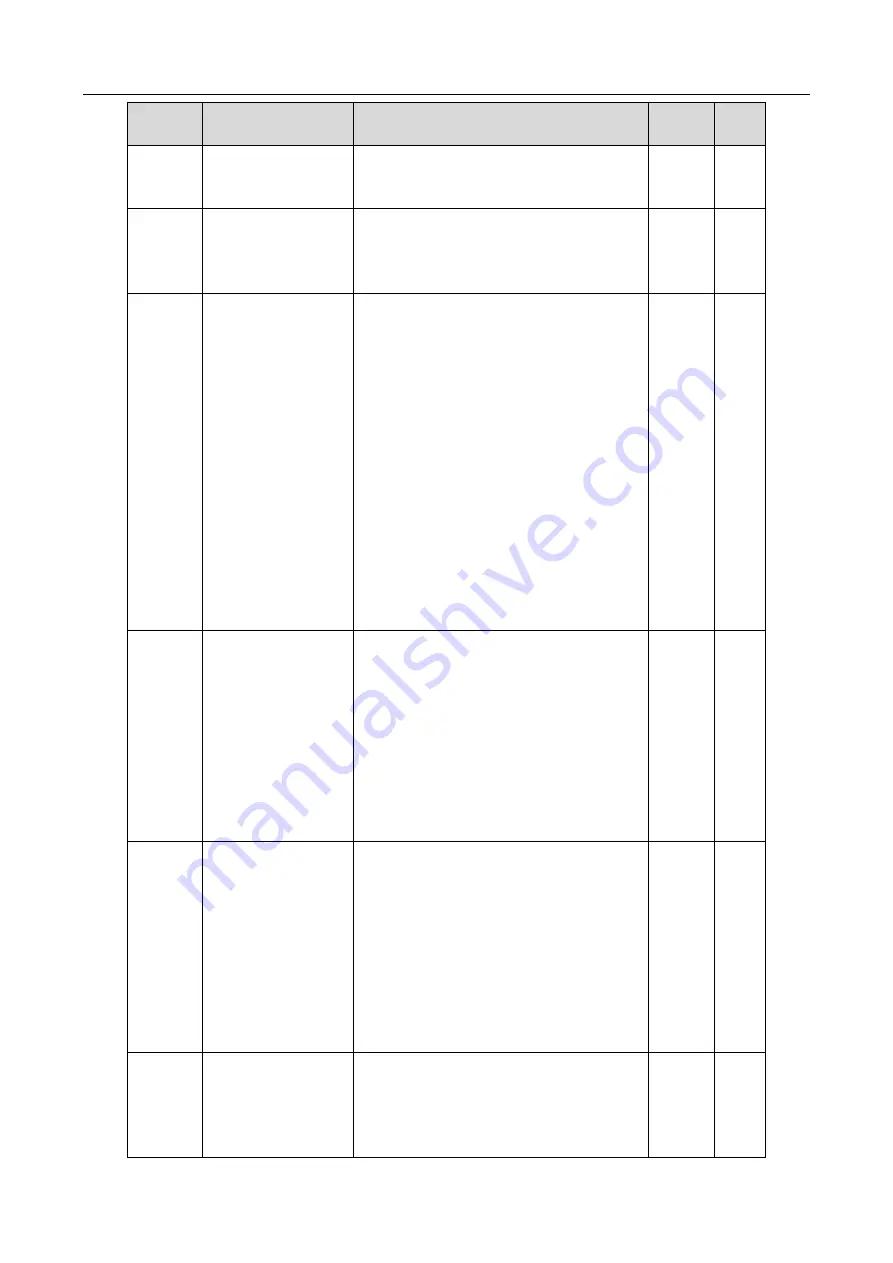
Goodrive600 series high-performance multifunction VFD
Function parameter list
-288-
Function
code
Name
Description
Default Modify
signal of the controlled system.
The system always performs calculation by using
a relative value (0
–100.0%).
P09.01
PID reference preset
through keypad
The function code is mandatory when P09.00=0.
The base value of The function code is the
feedback of the system.
Setting range: -100.0%
–100.0%
0.0%
○
P09.02
PID feedback source
Used to select PID feedback channel.
0: AI1
1: AI2
2: AI3
3: Reserved
4: Modbus communication
5: CANopen communication
6: Ethernet communication
7: Reserved
8: EtherCAT/PROFINET communication
9: Programmable expansion card
10: MAX(AI1,AI2)
11: PROFIBUS-DP/DeviceNet communication
Note: The reference channel and feedback
channel cannot be duplicate. Otherwise,
effective PID control cannot be achieved.
0
○
P09.03
PID output
characteristics selection
0: PID output is positive. When the feedback
signal is greater than the PID reference value,
the output frequency of the inverter unit will
decrease to balance the PID. Example: PID
control on strain during unwinding.
1: PID output is negative. When the feedback
signal is greater than the PID reference value,
the output frequency of the inverter unit will
increase to balance the PID. Example: PID
control on strain during unwinding
0
○
P09.04
Proportional gain (Kp)
The function is applied to the proportional gain P
of PID input.
P determines the strength of the whole PID
adjuster. The value 100 indicates that when the
difference between the PID feedback value and
given value is 100%, the range within which the
PID regulator can regulate the output frequency
command is the max. frequency (ignoring
integral function and differential function).
Setting range: 0.00
–100.00
1.80
○
P09.05
Integral time (Ti)
Used to determine the speed of the integral
adjustment on the deviation of PID feedback and
reference from the PID regulator.
When the deviation of PID feedback and
reference is 100%, the integral adjuster works
0.90s
○