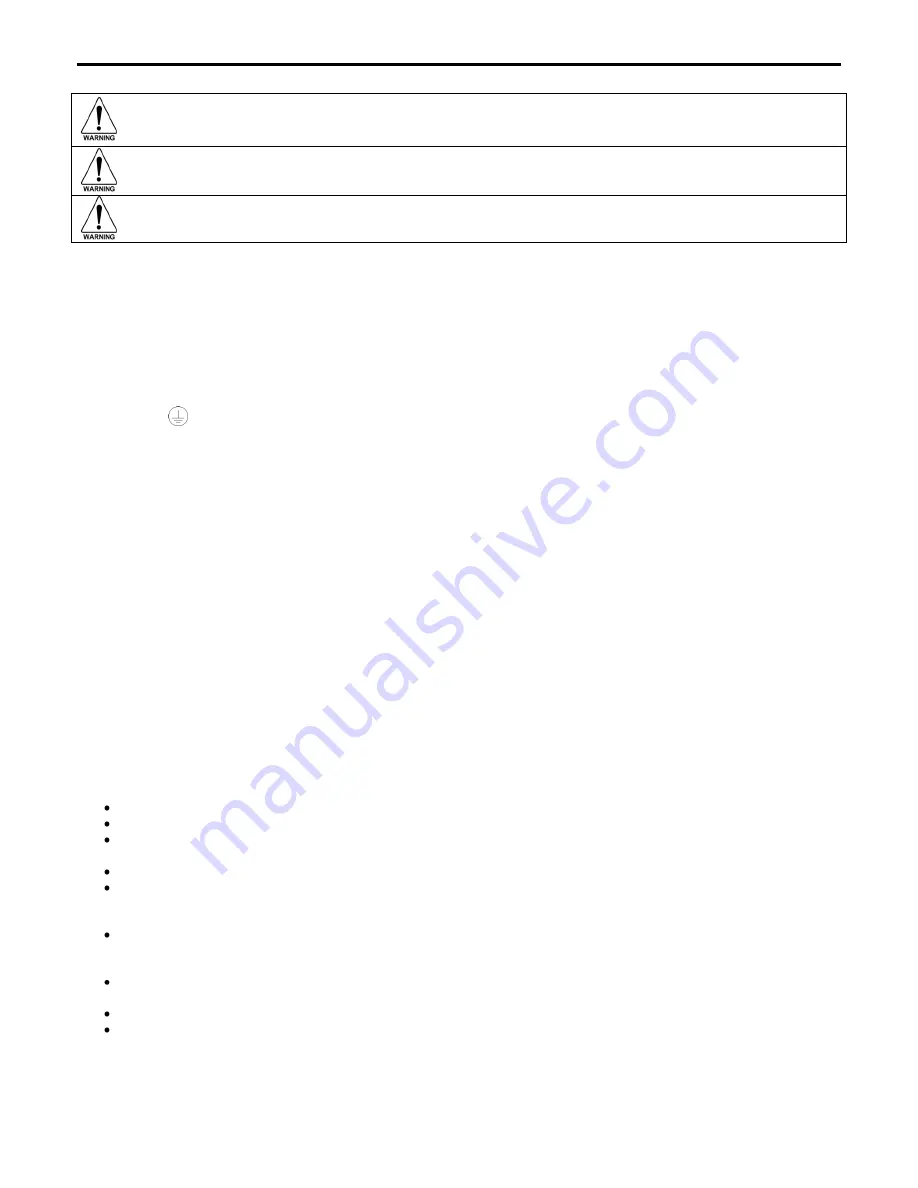
Optidrive VTC – User Guide
www.invertek.co.uk
9
4.
Electrical Installation
4.1.
Grounding the Drive
This manual is intended as a guide for proper installation. Invertek Drives Ltd cannot assume responsibility for the compliance or the
non-compliance to any code, national, local or otherwise, for the proper installation of this drive or associated equipment. A hazard
of personal injury and/or equipment damage exists if codes are ignored during installation.
This Optidrive contains high voltage capacitors that take time to discharge after removal of the main supply. Before working on the
drive, ensure isolation of the main supply from line inputs. Wait ten (10) minutes for the capacitors to discharge to safe voltage levels.
Failure to observe this precaution could result in severe bodily injury or loss of life.
Only qualified electrical personnel familiar with the construction and operation of this equipment and the hazards involved should
install, adjust, operate, or service this equipment. Read and understand this manual and other applicable manuals in their entirety
before proceeding. Failure to observe this precaution could result in severe bodily injury or loss of life.
Grounding Guidelines
The ground terminal of each Optidrive should be individually connected DIRECTLY to the site ground bus bar (through the filter if installed).
Optidrive ground connections should not loop from one drive to another, or to, or from any other equipment. Ground loop impedance must
confirm to local industrial safety regulations. To meet UL regulations, UL approved ring crimp terminals should be used for all ground wiring
connections.
The drive Safety Ground must be connected to system ground. Ground impedance must conform to the requirements of national and local
industrial safety regulations and/or electrical codes. The integrity of all ground connections should be checked periodically.
Protective Earth Conductor
The Cross sectional area of the PE Conductor must be at least equal to that of the incoming supply conductor.
Safety Ground
This is the safety ground for the drive that is required by code. One of these points must be connected to adjacent building steel (girder, joist), a
floor ground rod, or bus bar. Grounding points must comply with national and local industrial safety regulations and/or electrical codes.
Motor Ground
The motor ground must be connected to one of the ground terminals on the drive.
Ground Fault Monitoring
If a system ground fault monitor is to be used; only Type B devices should be used to avoid nuisance tripping.
Shield Termination (Cable Screen)
The safety ground terminal provides a grounding point for the motor cable shield. The motor cable shield connected to this terminal (drive end)
should also be connected to the motor frame (motor end). Use a shield terminating or EMI clamp to connect the shield to the safety ground
terminal.
When shielded cable is used for control and signal wiring, the shield should be grounded at the source end only, not at the drive end.
4.2.
Wiring Precautions
Connect drive according to section 4.4 Connection Diagram, ensuring that motor terminal box connections are correct. There are two connections
in general: Star and Delta. It is essential to ensure that the motor is connected in accordance with the voltage at which it will be operated. For
more information, refer to section 4.6 Motor Terminal Box Connections.
For recommended cabling and wiring sizing, refer to section 9.2 Rating tables.
It is recommended that the power cabling should be 3-core or 4-core PVC-insulated screened cable, laid in accordance with local industrial
regulations and codes of practice.
4.3.
Incoming Power Connection
For 1 phase supply power should be connected to L1/L, L2/N.
For 3 phase supplies power should be connected to L1, L2, and L3. Phase sequence is not important.
The Optidrive should be connected to a fixed supply using a suitable disconnecting device between the Optidrive and the AC Power
Source. The disconnecting device must conform to the local safety code / regulations.
The cables should be dimensions according to any local codes or regulations. Guideline dimensions are given in section 9.2.
Suitable fuses to provide wiring protection should be installed in the incoming supply line, according to the data in section 9.2. The fuses
must comply with any local codes or regulations in place. In general, IEC type gG or UL type T fuses are suitable. The operating time of
the fuses must be below 0.5 seconds.
Where allowed by local regulations, suitably dimensioned circuit breakers may be utilised in place of fuses. Thermal overload protection
is not required, as the Optidrive provides thermal protection for the motor and motor cable. Guideline dimensions are given in section
9.2.
When the power supply is removed from the drive, a minimum of 30 seconds should be allowed before re-applying the power. A
minimum of 5 minutes should be allowed before removing the terminal covers or connection.
The maximum permissible short circuit current at the Optidrive Power terminals as defined in IEC60439-1 is 100kA.
An Input Choke should be installed in the supply line for frame size 1 to 3 Optidrives where any of the following conditions occur:-
o
The incoming supply impedance is low or the fault level / short circuit current is high
o
The supply is prone to dips or brown outs
o
An imbalance exists on the supply (3 phase drives)
o
All installations of Frame Size 2 drives on 575 Volt Supply