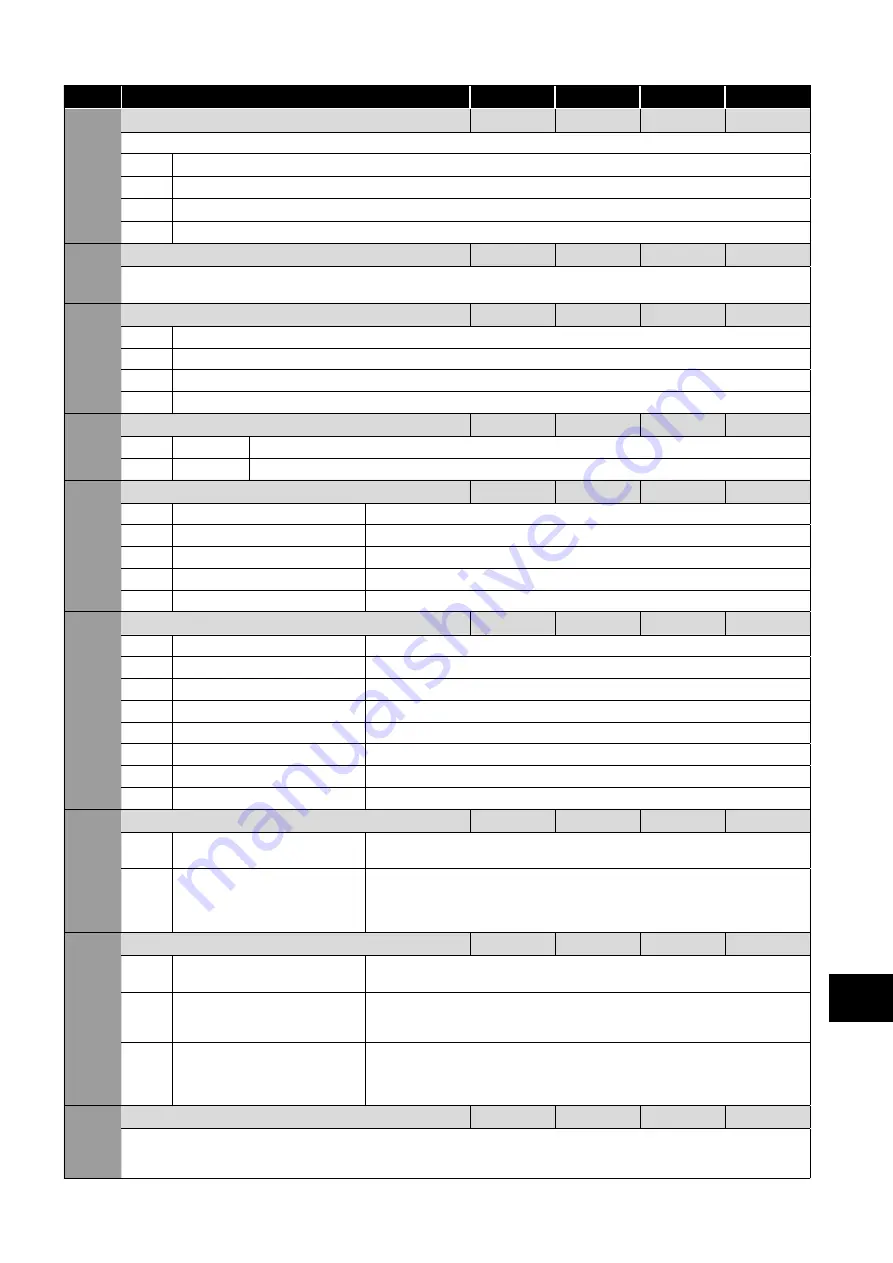
Version 3.00
| Optidrive P2 User Guide |
55
www.invertekdrives.com
Par
Name
Minimum
Maximum
Default
Units
P5-04 Modbus RTU / BACnet MSTP Data Format
-
-
-
-
Sets the expected Modbus telegram data format as follows:
No Parity, 1 stop bit
No parity, 2 stop bits
Odd parity, 1 stop bit
Even parity, 1 stop bit
P5-05 Communications Loss Timeout
0.0
5.0
2.0
Seconds
Sets the watchdog time period for the communications channel. If a valid telegram is not received by the Optidrive within this time period,
the drive will assume a loss of communications has occurred and react as selected below. Setting to zero disables the function.
P5-06 Communications Loss Action
0
3
0
-
0
Trip & Coast To Stop
1
Ramp to Stop Then Trip
2
Ramp to Stop Only (No Trip)
3
Run at Preset Speed 8
P5-07 Fieldbus Ramp Control
0
1
0
-
0
Disabled
Ramps are control from internal drive parameters P1-03 and P1-04.
1
Enabled
Ramps are controlled directly by the Fieldbus PDI4 Data Word.
P5-08 Fieldbus Process Data Output Word 4 Select
0
4
0
-
0
Output Torque
0 to 2000 = 0 to 200.0%
1
Output Power
Output power in kW to two decimal places, e.g. 400 = 4.00kW
2
Digital Input Status
Bit 0 indicates digital input 1 status, bit 1 indicates digital input 2 status etc
3
Analog Input 2 Signal Level
0 to 1000 = 0 to 100.0%
4
Drive Heatsink Temperature
0 to 100 = 0 to 100°C
P5-12
Fieldbus Process Data Output Word 3 Select
0
7
0
-
0
Motor current
Output current to 1 decimal place, e.g. 100 = 10.0 Amps
1
Power (x.xx kW)
Output power in kW to two decimal places, e.g. 400 = 4.00kW
2
Digital input status
Bit 0 indicates digital input 1 status, bit 1 indicates digital input 2 status etc.
3
Analog Input 2 Signal Level
0 to 1000 = 0 to 100.0%
4
Drive Heatsink Temperature
0 to 100 = 0 to 100°C
5
User register 1
User Defined Register 1 Value
6
User register 2
User Defined Register 1 Value
7
P0-80 value
User Selected data value
P5-13
Fieldbus Ramp Control
0
1
0
-
0
Fieldbus Ramp Control
This option must be selected if the drive acceleration and deceleration ramps are to
be controlled from the fieldbus. P5-07 must also be set to 1 to enable this function.
1
User register 4
The value received by the drive in PDI 4 is transferred to User Register 4. This option
allows the function of the process data word to be defined in Parameter Group 9.
In this case, User Register 4 should not be written to within any PLC function code,
although the value can be read.
P5-14
Fieldbus Process Data Input Word 3 Select
0
2
0
-
0
Torque limit/reference
This option must be selected if the drive output torque limit / setpoint is to be controlled
from the fieldbus. This also requires setting P4-06 = 3.
1
User PID reference register
This option allows the setpoint to the PID controller to be received from the Fieldbus. In
order for this option to be used, P9-38 must be set to 1, and the PID User setpoint must
not be utilised within the PLC function.
2
User register 3
The value received by the drive in PDI 3 is transferred to User Register 3. This option
allows the function of the process data word to be defined in Parameter Group 9.
In this case, User Register 3 should not be written to within any PLC function code,
although the value can be read.
P5-15
Modbus Response Delay
0
16
0
Chr
Allows the user to configure an additional delay between the drive receiving a request via the Modbus RTU interface, and transmitting a
reply. The value entered represents the delay in addition to the minimum delay permissible according to the Modbus RTU specification,
and is expressed as the number of additional characters.
8
Extended P
arameters