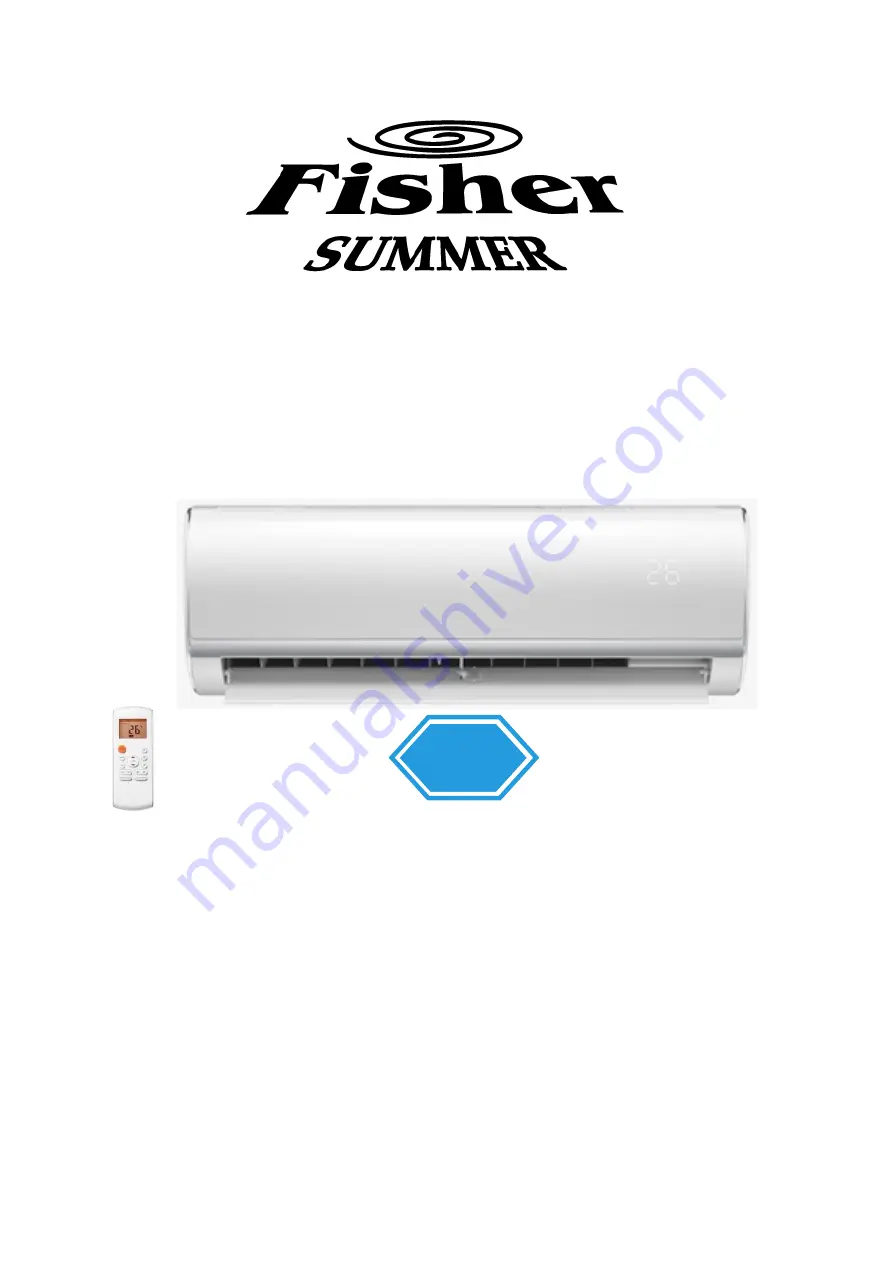
SERVICE MANUAL
Room Air Conditioner
Split Wall-Mounted Type
NOTE:
Before servicing the unit, please read this at first.
Always contact with your service center if meet problem.
FSAI-SU-123AE3 / FSOAI-SU-123AE3
FSAI-SU-93AE3 / FSOAI-SU-93AE3
FSAIF-SU-183AE3 / FSOAIF-SU-183AE3
FSAIF-SU-243AE3 / FSOAIF-SU-243AE3
FI_SM_FSAI-S
U
-93-123_FSAIF-S
U
-183-243AE3_20180909
R32
Summary of Contents for FSAI-SU-93AE3
Page 2: ......
Page 4: ......
Page 5: ...Contents 1 Precautions 2 2 Information servicing 3 Safety Precautions...