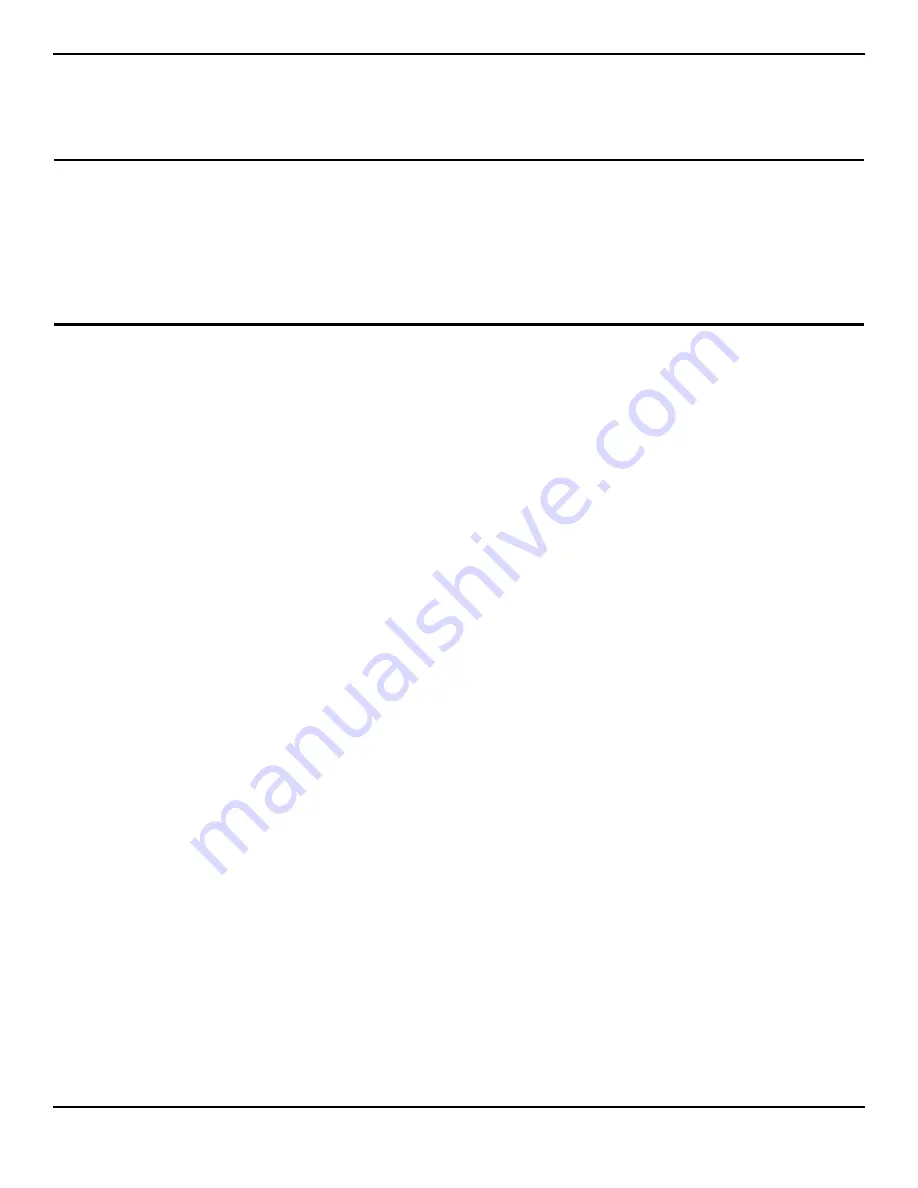
SECTION 11—TRANSPORT IN VEHICLES
82
Securing the Occupant
Wheelchair-Anchored Belts
WARNING
Risk of Injury, Damage or Death
Lack or improper use of wheelchair transport systems may result in injury, damage or death.
– Use both pelvic and upper torso belts.
– The pelvic belt that is provided by Invacare has been tested for use in a motor vehicle on this
wheelchair only. Do not replace the pelvic belt with a different style pelvic belt.
NOTE: For this procedure, refer to FIGURE 11.2 on page 83.
The wheelchair has been provided with a pelvic belt which meets the requirements of ANSI/RESNA W/C 19.
The pelvic belt, provided by Invacare, has been designed to accommodate use on either side of the vehicle. If necessary,
follow the instructions below to reverse the orientation of the pelvic belt to accommodate the vehicle-anchored upper-torso
belt.
1.
Install the pelvic belt pin (Detail “A” of FIGURE 11.2) into the large end of the slot in the belt mounting bracket (Detail
“B” or Detail “C”). Rotate downward and forward until it snaps into place into the small end of the slot.
NOTE: Note the position of the male end of the belt when installing the pelvic belt onto the belt mounting brackets. The male end of the
pelvic belt (Detail "A" of FIGURE 11.2) has a pin which is used to secure the vehicle-anchored upper-torso belt.
2.
Repeat STEP 1 for the opposite belt mounting bracket.
3.
Install the vehicle-anchored upper-torso belt onto the pin on the male end of the pelvic belt.