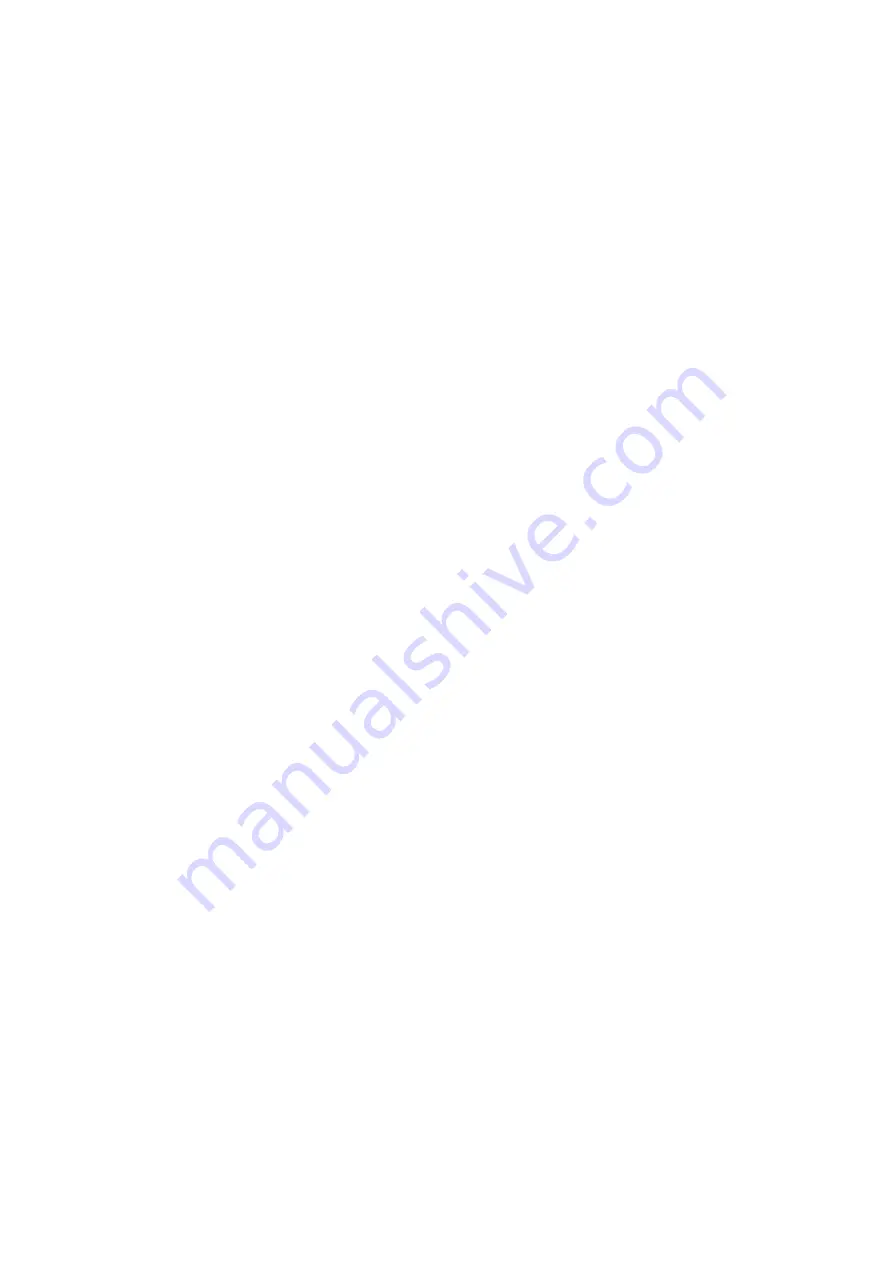
Technical data
3
j
| BA 14.0190 - EN | 02/2007
10
3.1.1
General information
The spring-applied brake INTORQ BFK468-
is a single-disk brake with two friction
surfaces. The brake torque is generated by several compression springs (2) by friction. The
brake is released electromagnetically with holding current reduction via an INTORQ
bridge/half-wave rectifier.
The spring-applied brake is designed for the conversion of mechanical work and kinetic energy
into heat. For operating speed, see chapter 3.3 Rated data. Due to the static brake torque,
the brake can hold loads without speed difference. Emergency braking is possible at high
speed, see chapter 3.3 Rated data. The more friction work, the higher the wear.
The stator (7) is designed in thermal class F. The limit temperature of the coils is 155°C.
3.1.2
Braking
During braking, the rotor (3), which is axially movable on the hub (4), is pressed against
the friction surface - via the armature plate (1) - by means of the inner and outer springs
(2). The asbestos-free friction linings ensure a high brake torque with low wear. The brake
torque is transmitted between hub (4) and rotor (3) via the splines.
3.1.3
Brake release
In braked state, there is an air gap ”s
Lü”
between stator (7) and armature plate (1). To release
the brake, the stator coil (7) is excited with the DC voltage provided. The magnetic force
generated attracts the armature plate (1) towards the stator (7) against the spring force. The
rotor (3) is then released and can rotate freely.
3.1.4
Reducing the brake torque
For basic module E (adjustable), the spring force and thus the brake torque can be reduced
by unscrewing the adjuster nut (8) (
35).
3.1.5
Manual release (optional for sizes 18 to 25)
The manual release is optionally available for short-term releases when no voltage is applied.
The manual release can be retrofitted.
3.1.6
Microswitch (optional)
The manufacturer offers the microswitch for air-gap or wear monitoring. The user must provide
the corresponding electrical connection (
27 following).
When air-gap monitoring, the motor does not start before the brake has been released. With
this set-up, all possible faults are monitored. For example, in the event of defective rectifiers,
interrupted connection cables, defective coils, or excessive air gaps the motor will not start.
When checking the wear, no current will be applied to the brake and the motor if the air gap
is too large.