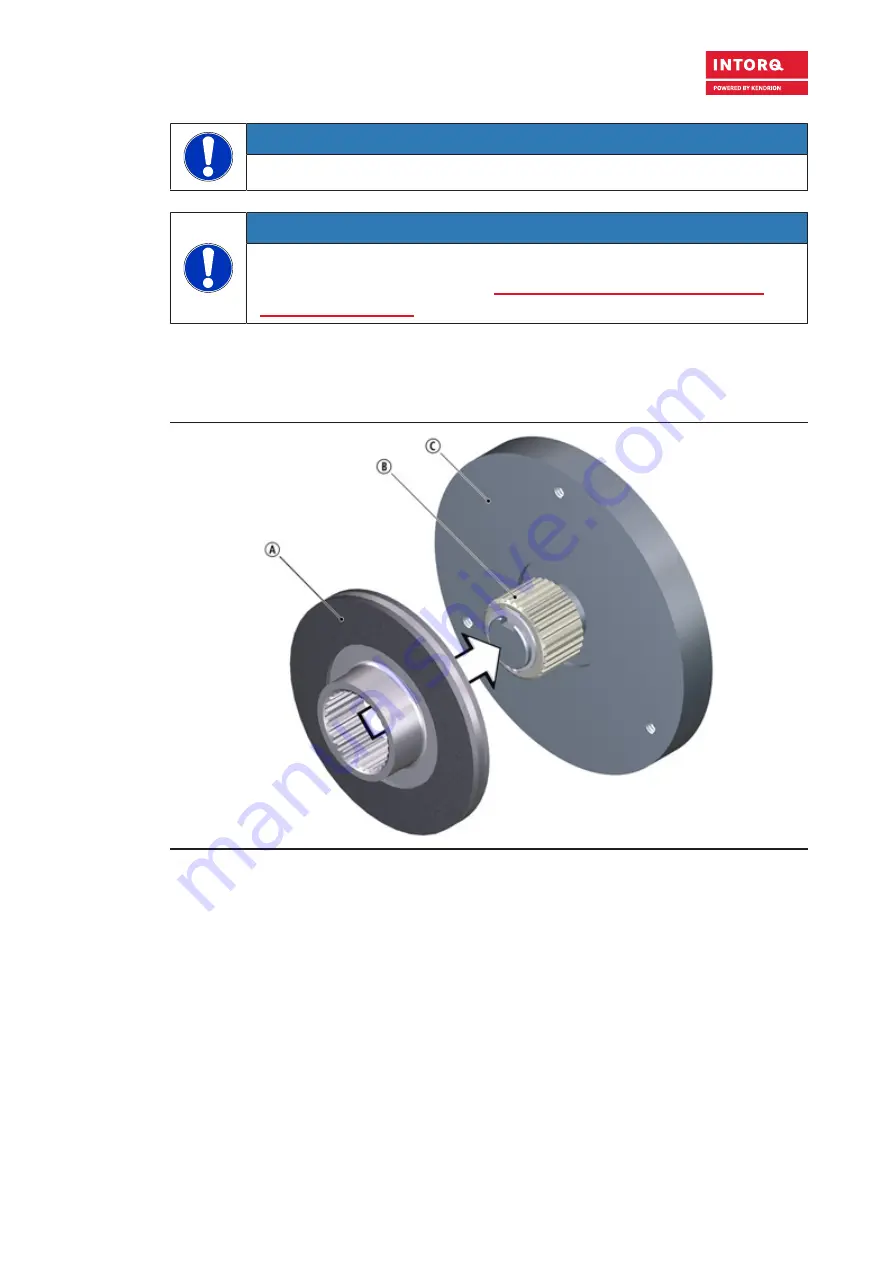
Mechanical installation
Kendrion INTORQ | BA 14.0225 | 05/2022
29
NOTICE
If you are using the spring-applied brake for reverse operations, glue the hub to the shaft.
NOTICE
When using the spring-applied brake as a safety brake: Observe the information concern-
ing the shaft-hub connection in section Applications with special safety requirements
("Safety Brake"), Page 10.
5.5
Mounting the brake
Mounting the rotor (without friction plate / without brake flange)
Fig. 12:
Assembly of the rotor
A
Rotor
B
Hub
C
End shield
1. Push the rotor on the hub.
2. Check if the rotor can be moved manually.