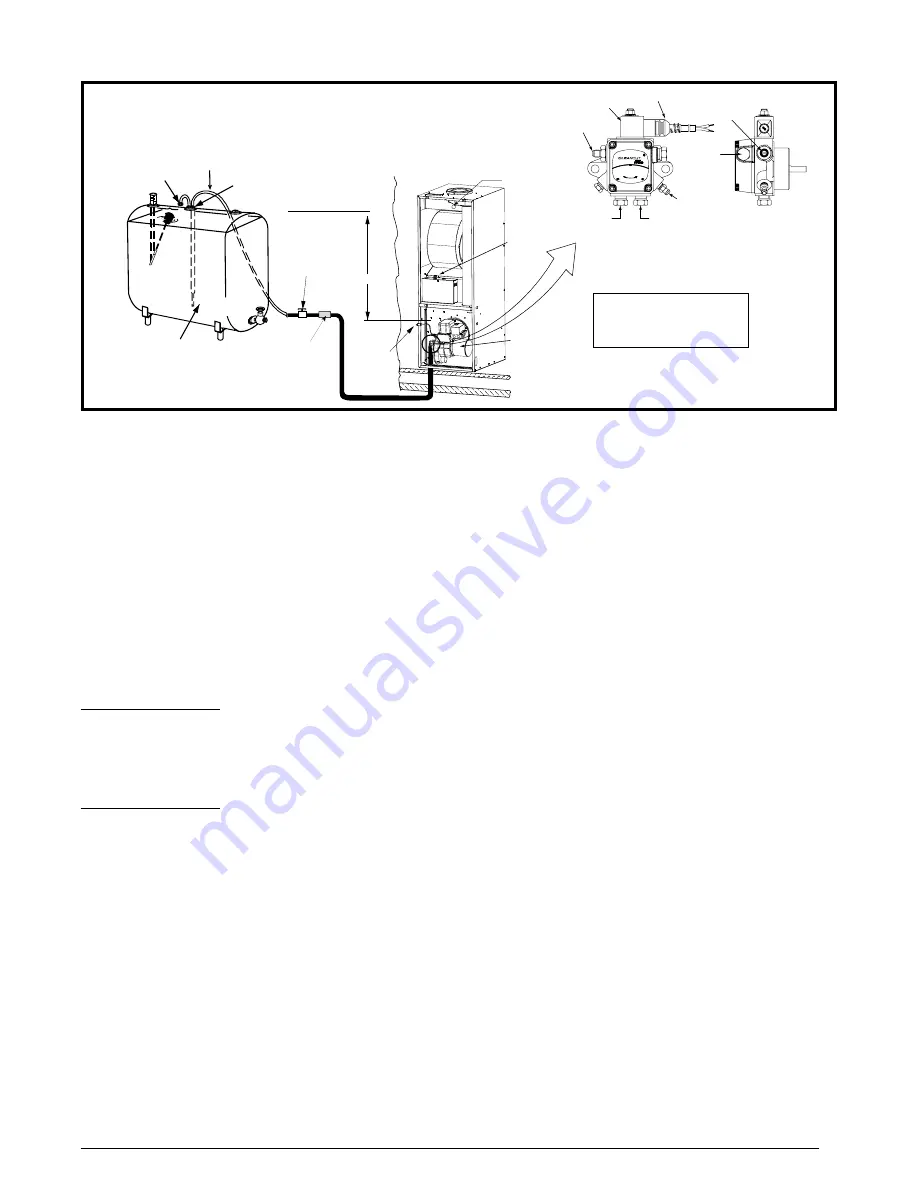
19
Figure 27
Figure 27. typical oil Piping for above Ground (single-line) supply
If fuel pump fails to lift oil, check for air
port plug and repeat priming procedure.
leaks and tighten all fuel fittings. Re-
prime fuel pump by injecting fuel oil into
optional (top) return port. Replace return
Top of Tank
8 ft.
Shut-off
Valve
Optional
Fuel
Filter
Alternate
Fuel Line
Entry
Control
Panel
Oil
Furnace
On-Off-Fan
Switch
Floor Cavity
Oil-Gun
Burner
Floor
Flue Gas
Sampling
Hole
Drain
End of Oil Supply Line
3" to 5" Above Bottom Drain
Guide
Pipe
Gauge
Vent with cap
2" Duplex
Bushing
2" Fill
3/8" Oil Supply Line
NOTE:
Additional venting may be
required if tank is filled rapidly.
4 GPH 100-150 PSI 3450 RPM
3 GPH 150-200 PSI 3450 RPM
VALVE ON DELAY
NO. 2 & LIGHTER FUEL
USE ONLY WITH
INLET
BY-PASS
Exclusively for Beckett
Made by Suntec
INLET
NO. 2 FUEL
A2EA-6520
Beckett
Nozzle Port
3/16 Flare Fitting
Bypass Solenoid Valve
Cordset
Inlet Port
1/4 NPTF
Bleed & Gauge Port
Pressure Adjustment
Screw
Inlet Port
1/4 NPTF
Return Port - Install 1/6” Bypass Pipe
Plug for 2-pipe System Only.
(Use 5/32” Allen Wrench)
• The inside of the tank must be clean before filling. All
water, rust, sediment, and debris must be flushed out.
• A fuel or tank gauge is recommended for easy checking
of the fuel level. Check the gauge reading with a dipstick.
See
.
• Locate the storage tank conveniently near the home.
If the fuel tank is installed above ground, the tank may
rest 3 to 4 inches off the ground. Fuel tanks may also
be buried if properly coated to resist corrosion. The
vertical dimension from the bottom of the fuel tank to
the fuel pump must not exceed 10 feet.
• Keep the tank filled, especially in the summer to reduce
the accumulation of condensation.
One-Line System
The One-Line System is highly recommended where
vertical lift, from bottom of tank to pump, is less than 8
feet (
). A single line hookup has the advantage
of lower cost and quieter operation.
Two-Line System
If a Two-Line system is used or if oil is taken from the
bottom of the tank, a filter is recommended. A Two-Line
system should only be used if vertical lift exceeds 8 feet.
1. Install the oil feed line as outlined in steps 1 - 6 below.
2. Install the oil pump bypass plug in the bottom return
port.
3. Route the return line up through the furnace base to
the return port of the pump. Route the other end of the
line to the tank, using 3/8” O.D. copper tubing or 1/4”
pipe with the ends capped.
4. Insert the return line through the second opening in the
duplex bushing. If the bottom of the tank is lower than
the pump intake, the tube should be inserted three or
four inches from the tank bottom. If the bottom of the
tank is higher than the pump intake, the return line
should extend not more than 8” inside the tank.
Fuel line Hook-up
1. Use a 3/8” O.D. copper tubing for the fuel line.
notE:
Cap the end with tape to keep out dirt while the
line is being routed.
2. Install duplex bushing for two 3/8” lines in the top fitting
of the tank. See
3. Insert one end of the tubing through the duplex bushing
until it is three to five inches from the bottom drain.
Tighten the bushing.
4. Route the line where it will not incur any damage. Make
bends gradual and avoid kinks which might restrict oil
flow.
5. Open the furnace door and connect the oil line to the
intake port on the pump. Tighten other port plugs on
the pump.
notE:
Verify the oil line is airtight! Air leaks
can cause the pump to lose prime and will create other
problems such as nozzle failure, odors, rumbling noise,
and false safety shutdown.
6. Insert the short length of the copper tube level with the
bottom of the duplex bushing. Form the tube into an
inverted “U” to serve as a vent.
Fuel Line Bleeding
To eliminate problems caused by air in the oil line, all
connections in the oil supply line and all plugs, nuts,
and fittings on the pump must be airtight.
notE:
This
includes the nut that covers the pressure adjustment. It
is important that the hook-up be done carefully and with
a good flaring tool.
Prepare the burner for priming by attaching a clear plastic
hose over the bleed port fitting and fully opening the pump
bleed port. Use a suitable container to collect purged oil.
To ensure continuous operation, use a wire to jump
terminals
t-t
(or
F-F
) on the primary control while burner
is running.