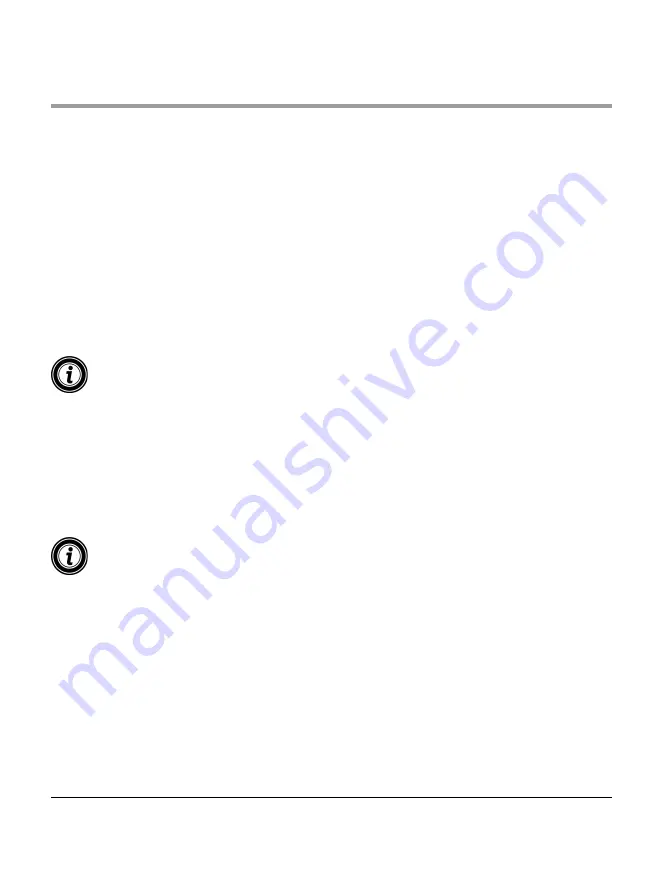
Version 2.5 (11/2020) UL
Translation of the original operating manual
15 of 140
Product information
3
Product information
3.1
Product description
The MultiControl is a control system for conveyor systems, which can control up to four Interroll RollerDrives. It is also
a certified I/O device for PROFINET, EtherNet/IP and EtherCAT and can therefore be linked with other MultiControls
and a PLC.
Sensors and RollerDrives can be directly integrated into the fieldbus level via the MultiControl. This completely
eliminates the need for an additional sensor/actuator level.
Some applications are already pre-programmed in the MultiControl for applications with special conveying logic. It
can therefore be used as a standalone control system – with or without connected PLC.
The MultiControl is compatible with all 24 V/48 V conveyor modules from Interroll Automation GmbH. So-called ZPA
(zero pressure accumulation) programs are used for operating the conveyor modules with zero pressure accumulation.
The MultiControl BI communicates with the connected RollerDrive EC5000 BI via the CANopen protocol.
Further information on the integrated programs and functions can be found in accompanying document
"MultiControl / RollerDrive - Start-up and Programming".
Energy recovery/overvoltage protection
If the RollerDrive is stopped or the speed is abruptly reduced, the kinetic energy of the conveyed material in the
RollerDrive is converted into electrical energy, akin to a generator. This energy is fed back into the system, where it
can be used by other RollerDrive units.
If more energy is fed back than can be used, the excess energy is converted into heat via a brake chopper in the
MultiControl. The brake chopper is activated when the voltage rises above 28 V/56 V. This prevents excessively high
voltages within the system.
Note the energy recovery capacity of the power supply units used.
We recommend the use of Interroll High Performance power supplies HP 5424 / HP5448 with a
regenerative strength up to 35 V / 60 V.
With the MultiControl 24 V it is possible to reduce the brake chopper operating voltage to 26 V (see
Overload protection
If the brake chopper remains switched on for longer than two seconds, it is switched off again as it is assumed that the
power supply unit is delivering an incorrect voltage. The activated overload protection is indicated by the LED display.
Whenever the overload protection is active, the motors cannot be switched on.
The MultiControl does not provide a protective mechanism against excess temperature in the connected RollerDrive.
Summary of Contents for MultiControl AI
Page 68: ...68 of 140 Version 2 5 11 2020 UL Translation of the original operating manual Appendix ...
Page 74: ...74 sur 140 Version 2 5 11 2020 UL Traduction de la notice d utilisation originale ...
Page 136: ...136 sur 140 Version 2 5 11 2020 UL Traduction de la notice d utilisation originale Annexe ...
Page 137: ...Version 2 5 11 2020 UL Traduction de la notice d utilisation originale 137 sur 140 Notes ...
Page 138: ...138 sur 140 Version 2 5 11 2020 UL Traduction de la notice d utilisation originale Notes ...
Page 139: ......
Page 140: ...INSPIREDBY EFFICIENCY 2020 INTERROLL EN FR UL 11 2020 Version 2 5 1119087 ...