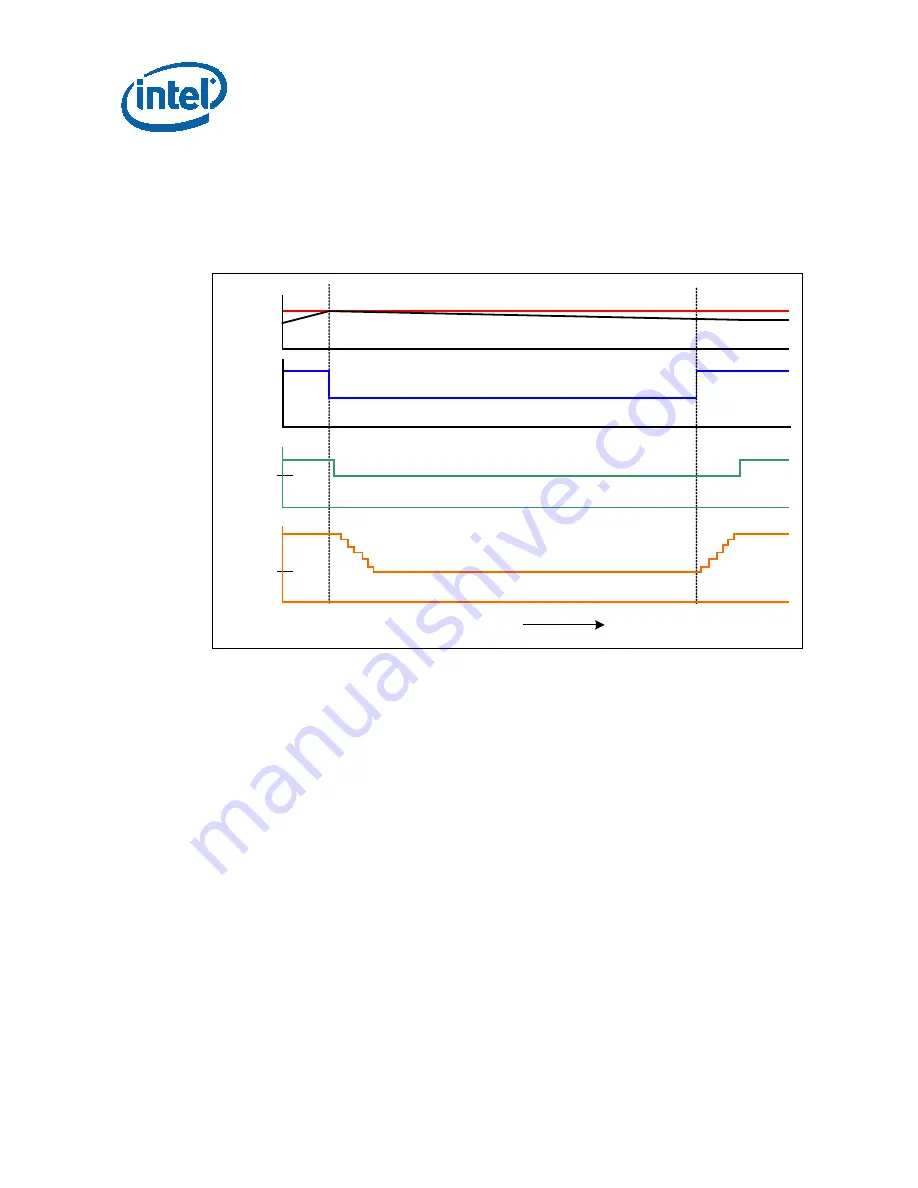
Thermal Management Logic and Thermal Monitor Feature
34
Thermal and Mechanical Design Guidelines
Once the processor has sufficiently cooled, and a minimum activation time has
expired, the operating frequency and voltage transition back to the normal system
operating point. Transition of the VID code will occur first, in order to insure proper
operation once the processor reaches its normal operating frequency. Refer to
Figure 4-2 for an illustration of this ordering.
Figure 4-2. Thermal Monitor 2 Frequency and Voltage Ordering
Refer to the datasheet
for further information on TM2.
4.2.4
Operation and Configuration
Thermal Monitor must be enabled to ensure proper processor operation.
The Thermal Control Circuit feature can be configured and monitored in a number of
ways. OEMs are required to enable the Thermal Control Circuit while using various
registers and outputs to monitor the processor thermal status. The Thermal Control
Circuit is enabled by the BIOS setting a bit in an MSR (model specific register).
Enabling the Thermal Control Circuit allows the processor to attempt to maintain a
safe operating temperature without the need for special software drivers or interrupt
handling routines. When the Thermal Control Circuit has been enabled, processor
power consumption will be reduced after the thermal sensor detects a high
temperature (that is, PROCHOT# assertion). The Thermal Control Circuit and
PROCHOT# transitions to inactive once the temperature has been reduced below the
thermal trip point, although a small time-based hysteresis has been included to
prevent multiple PROCHOT# transitions around the trip point. External hardware can
monitor PROCHOT# and generate an interrupt whenever there is a transition from
active-to-inactive or inactive-to-active. PROCHOT# can also be configured to generate
an internal interrupt which would initiate an OEM supplied interrupt service routine.
VID
Frequency
Temperature
T
TM2
f
MAX
f
TM2
VID
VID
TM2
PROCHOT#
Time
Summary of Contents for CELERON PROCESSOR E3000 - THERMAL AND MECHANICAL DESIGN
Page 24: ...Processor Thermal Mechanical Information 24 Thermal and Mechanical Design Guidelines ...
Page 80: ...Heatsink Clip Load Metrology 80 Thermal and Mechanical Design Guidelines ...
Page 82: ...Thermal Interface Management 82 Thermal and Mechanical Design Guidelines ...
Page 108: ...Fan Performance for Reference Design 108 Thermal and Mechanical Design Guidelines ...