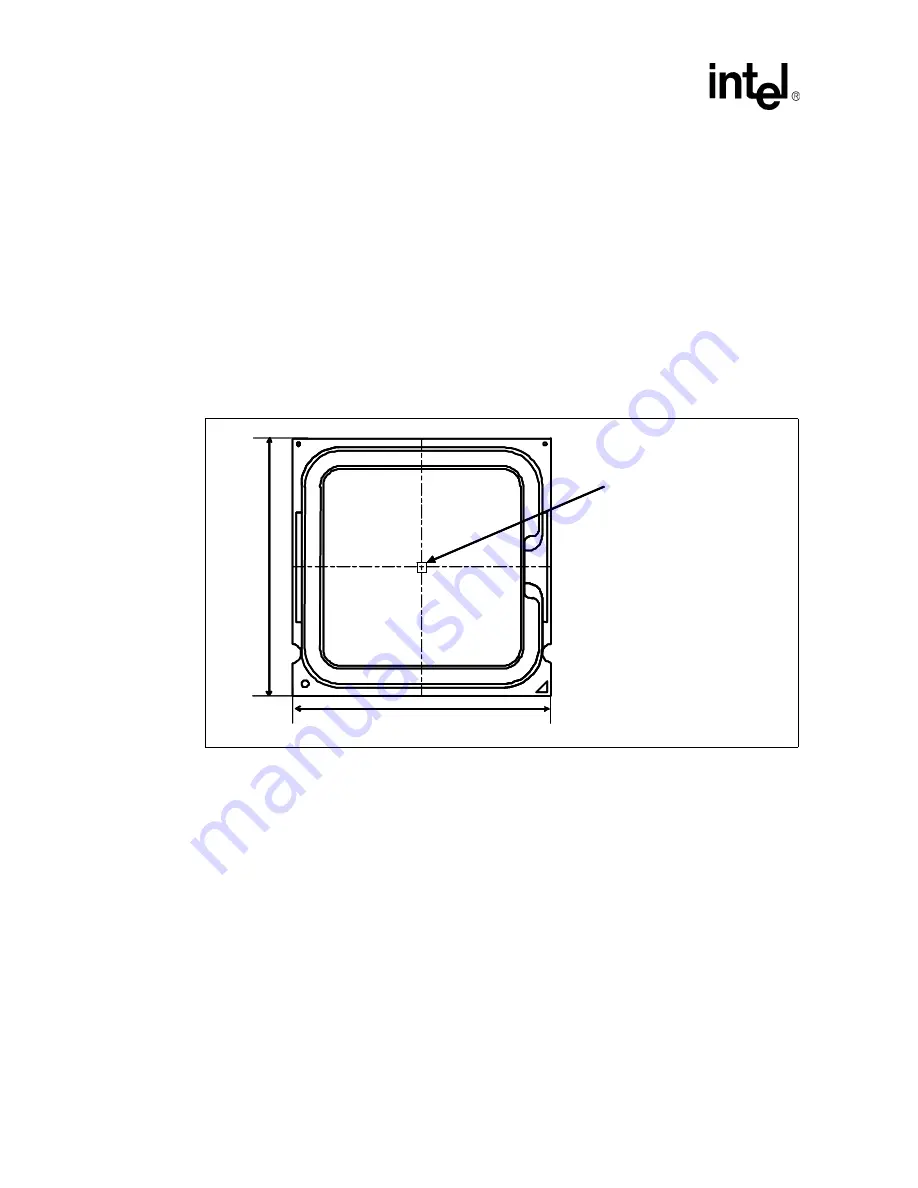
12
Intel
®
Celeron
®
D Processor in the 775-Land LGA Package
Thermal Design Guide
Order #303730
Processor Thermal/Mechanical Information
Intel has introduced a new method for specifying the thermal limits for the Celeron D Processor in
the 775-Land LGA Package. The new parameters are the Thermal Profile and T
CONTROL
. The
Thermal Profile defines the maximum case temperature as a function of power being dissipated.
T
CONTROL
is a specification used in conjunction with the temperature reported by the on-die
thermal diode. Designing to these specifications allows optimization of thermal designs for
processor performance and acoustic noise reduction.
2.2.1
Processor Case Temperature and Power Dissipation
For the Celeron D processor in the 775-land LGA package, the case temperature is defined as the
temperature measured at the geometric center of the package on the surface of the IHS. For
illustration,
shows the measurement location for a 37.5 mm x 37.5 mm [1.474 in x 1.474
in] FCLGA4 package with a 28.7 mm x 28.7 mm [1.13 in x 1.13 in] IHS top surface. Techniques
for measuring the case temperature are detailed in
.
2.2.2
Thermal Profile
The Thermal Profile defines the maximum case temperature as a function of processor power
dissipation. The TDP and Maximum Case Temperature are defined as the maximum values of the
thermal profile. By design the thermal solutions must meet the thermal profile for all system
operating conditions and processor power levels.
The slope of the thermal profile was established assuming a generational improvement in thermal
solution performance of about 10% based on previous Intel reference design. This performance is
expressed as the slope on the thermal profile and can be thought of as the
Ψ
CA
. The intercept on the
thermal profile assumes a maximum ambient operating condition that is consistent with the
available chassis solutions.
Figure 2. Processor Case Temperature Measurement Location
37.5 mm
Measure T
C
at this point
(geometric center of the package)
37.
5 m
m
37.5 mm
Measure T
C
at this point
(geometric center of the package)
37.
5 m
m