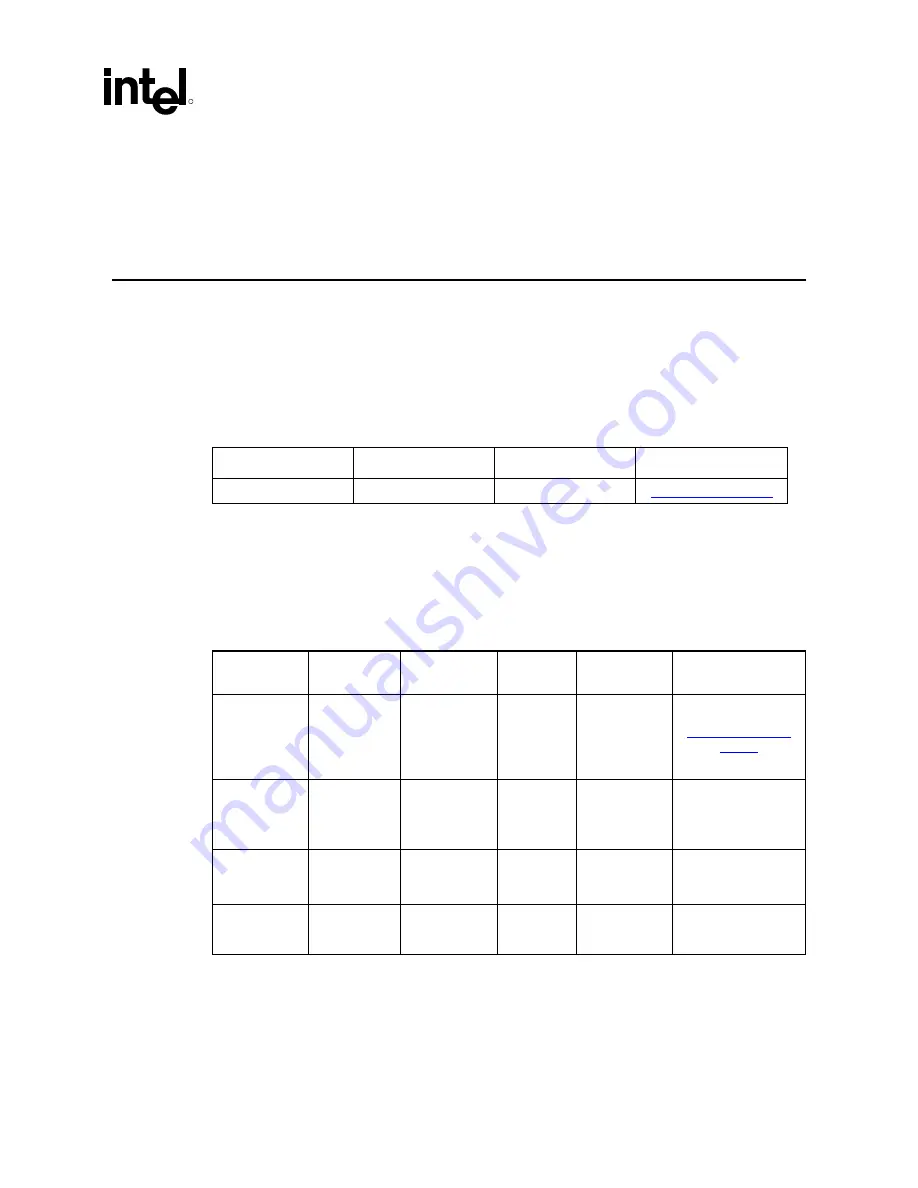
Intel Enabled Reference Solution Information
R
Thermal/Mechanical Design Guide
105
Appendix H Intel Enabled Reference
Solution Information
This appendix includes current supplier information for Intel enabled vendors for the Pentium 4
processor in the 775–land LGA package reference thermal solution.
The reference component designs are available for adoption by suppliers and heatsink integrators
pending completion of appropriate licensing contracts. For more information on licensing, contact
the Intel representative mentioned in Table 10.
Table 10. Intel Representative Contact for Licensing Information
Company Contact Phone
Intel Corporation
Tony De Leon
(253) 371-9339
Table 11 lists current suppliers that produce Intel enabled reference components. The part
numbers listed below identifies these reference components. End-users are responsible for the
verification of the Intel enabled component offerings with the supplier. OEMs and System
Integrators are responsible for thermal, mechanical, and environmental validation of these
solutions.
Table 11. Intel Reference Component Thermal Solution Provider
Supplier Part
Description
Part Number
Contact
Phone
CCI
(Chaun-
Choung
Technology
Corp.)
Intel
®
RCBFH-3
Reference
Heatsink
C40387 Harry
Lin
Monica
Chih
714-739-5797
+886-2-
29952666
Extension 131
AVC
(ASIA Vital
Components
Co., Ltd)
Intel
®
RCBFH-3
Reference
Heatsink
C40387 David
Chao
+886-2-
22996930
Extension:
619
m.tw
Sunon RCBFH-3
Fan
Assembly
N/A Tom
Blaskovich
714-255-0208
extension 206
ITW Fastex
RCBFH-3
Fastener
Base: C33389
Cap: C33390
Ron
Schmidt
847-299-2222 rschmidt@itwfastex.
com
Note:
These vendors and devices are listed by Intel as a convenience to Intel's general customer base,
but Intel does not make any representations or warranties whatsoever regarding quality,
reliability, functionality, or compatibility of these devices. This list and/or these devices may be
subject to change without notice.
§
Summary of Contents for 640 - Pentium 4 640 3.2GHz 800MHz 2MB Socket 775 CPU
Page 14: ...Introduction R 14 Thermal Mechanical Design Guide ...
Page 38: ...Thermal Management Logic and Thermal Monitor Feature R 38 Thermal Mechanical Design Guide ...
Page 52: ...Intel Thermal Mechanical Reference Design Information R 52 Thermal Mechanical Design Guide ...
Page 60: ...Acoustic Fan Speed Control R 60 Thermal Mechanical Design Guide ...
Page 72: ...Heatsink Clip Load Metrology R 72 Thermal Mechanical Design Guide ...
Page 99: ...Mechanical Drawings R Thermal Mechanical Design Guide 99 Figure 50 Reference Fastener Sheet 1 ...
Page 103: ...Mechanical Drawings R Thermal Mechanical Design Guide 103 Figure 54 Clip Heatsink Assembly ...