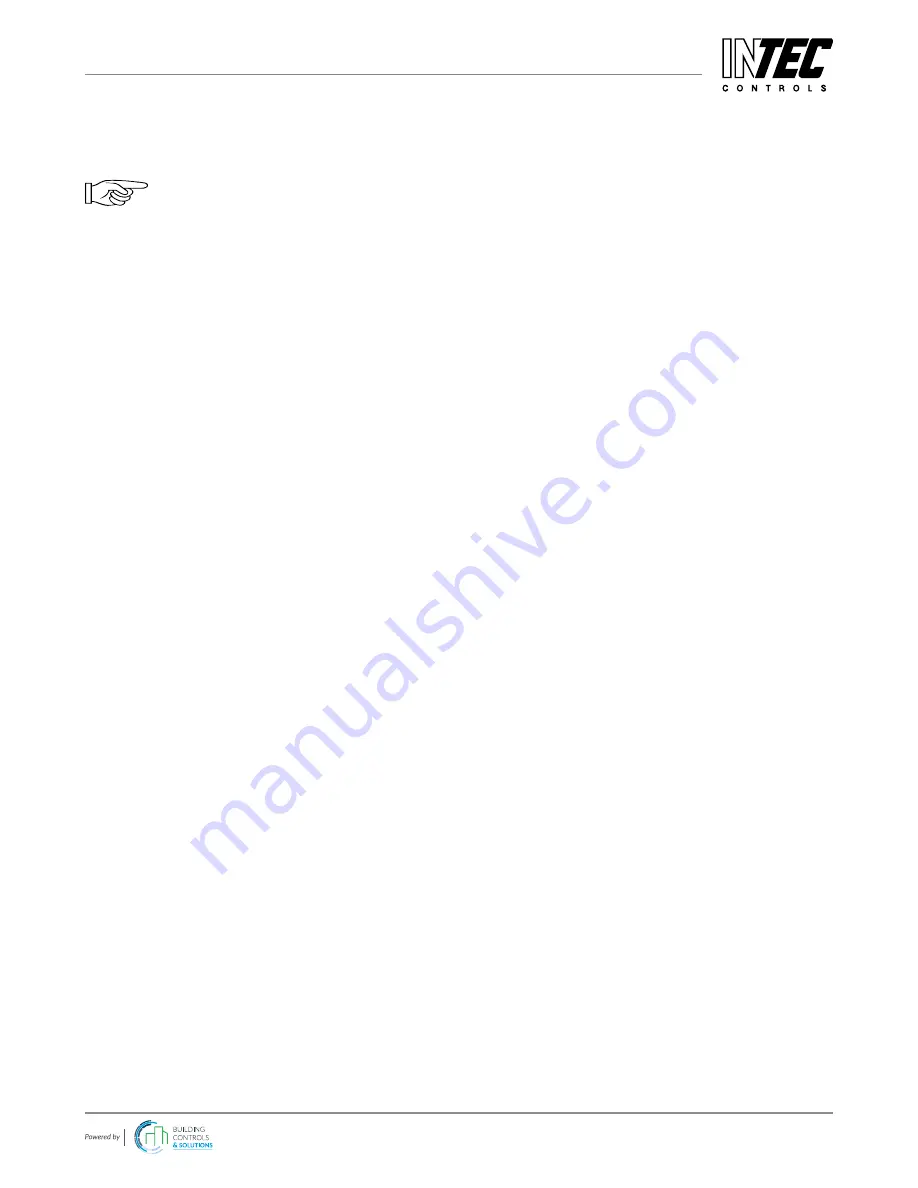
INTEC Controls | 12700 Stowe Drive, Suite 100, Poway, CA 92064 | Ph: (858) 578.7887 & (888) GO.INTEC | inteccontrols.com
Specifications subject to change without notice. | Tox_D_1119, Ex_D_1119, CO2_D_0320 | USA 200413 | Page 9 of 17
SC2-AT6 – UserManual
5.2 Exchange of Sensor Cartridge
Instead of the on-site calibration, the used SC can be replaced simply and conveniently by a calibrated one.
The communication of the sensor cartridge to the sensor board is continuously monitored during
operation and results in an immediate error message on the gas controller in case of fault or interruption.
When replacing the sensor unit, the communication of the local bus is interrupted when unplugging the
SC connector which leads to an immediate triggering of the error message.
• Disconnect the SC connector from the printed circuit board (error message will be activated).
• Loosen the locknut.
• Remove used SC.
• Take calibrated SC out of the original packaging, check for gas type, measuring range and valid calibration
date.
• Insert the SC and re-tighten with lock nut.
• Insert the SC plug into the socket at the circuit board. Check plug for proper connection.
The local bus communication is automatically established and tested. At the same time the gas type and the
measuring range of the “new” SC are compared with the data stored in the circuit board. If they match and the
communication is correct, the error message will be automatically acknowledged in the Gas Controller.
The yellow LED of the circuit board flashes with a pulse of 1 sec. as long as the SC connector is disconnected
(communication error). After the local bus communication has been re-established and the conformity test has been
successful, the LED goes into flashing mode with 3 sec. pulse duration until the sensor’s warm-up time is over.
Apply a defined gas concentration on the sensor element with the help of the gas generator and check the
measurement signal at the analog output or at the relay outputs.
The entire cycle “Sensor Element > Sensor Cartridge > Local Bus > Sensor Board > Field Bus > Controller” is
observed and completed.
6 Inspection and Service
Inspection, service and calibration of the sensor should be done by trained technicians at regular intervals. We
therefore recommend concluding a service contract with INTEC Controls or one of their authorized partners.
According to EN 45544-4, inspection and service have to be executed at regular intervals. The maximum intervals
have to be determined and respected by the person responsible for the gas warning system according to the legal
requirements. INTEC Controls recommends employing the common inspection and service intervals as specified in
the general regulations of the gas measuring technique. The recommended calibration intervals depend on the sensor
element and can be read from the table “Calibration”. If there are different intervals, always observe the shortest one.
Inspections and services must be documented. The date for the next maintenance has to be affixed to the sensor.
6.1 Inspection
Gas sensors should be controlled regularly by a competent person according to EN 45544-4. The following has to be
checked in particular:
• Maintenance/ calibration interval not exceeded.
• Visual inspection of the sensor including cable for damage etc.
• Remove dust deposits, especially at the gas inlet.
• The filter at the gas inlet has to be replaced if extremely dirty.