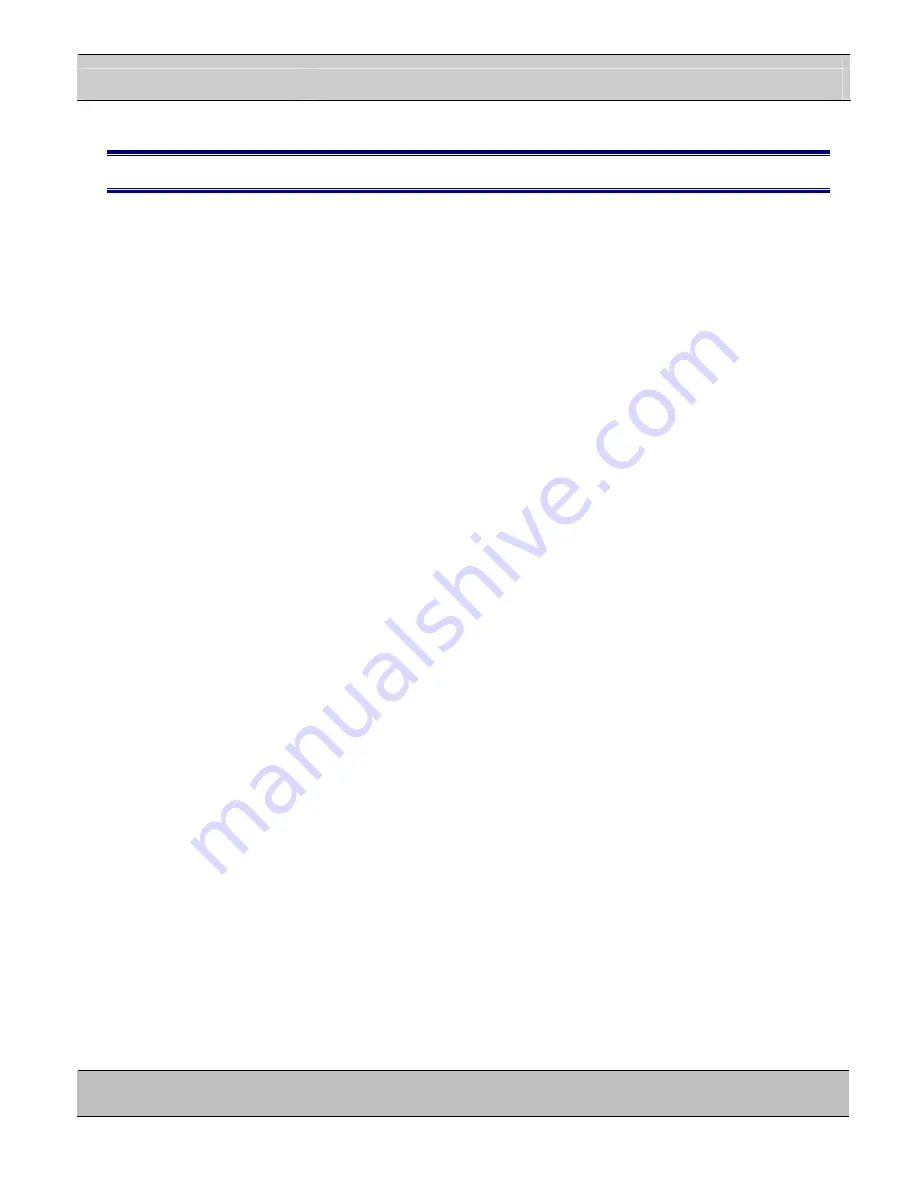
Instruction Manual
InstruTech CVM-211 "
Stinger
" Convection Vacuum Gauge Module
InstruTech, Inc
page 18
A
A
p
p
p
p
e
e
n
n
d
d
i
i
x
x
C
C
:
:
V
V
a
a
c
c
u
u
u
u
m
m
g
g
a
a
u
u
g
g
e
e
c
c
o
o
n
n
t
t
a
a
m
m
i
i
n
n
a
a
t
t
i
i
o
o
n
n
a
a
n
n
d
d
c
c
l
l
e
e
a
a
n
n
i
i
n
n
g
g
The most common cause of all vacuum gauge failures is contamination of the sensor. Noisy or erratic
readings, the inability to set zero or atmosphere, and total gauge failure, are all possible indications of
gauge contamination.
Contamination can be generally characterized as either: A) a reaction of process gases with sensor
elements, or B) an accumulation of material on the sensor elements. Sensors that fail due to chemical
reaction are generally not salvageable. Sensors that fail due to condensation, coatings, or particles may
possibly be restored by following the cleaning procedure described below.
A) Reactive Gases
If process gases react with the materials of construction of the sensor, the result is corrosion and
disintegration of the sensor over time. Plasma etching and other reactive semiconductor processes are
examples where this failure mode is common. In this instance, cleaning can not solve the problem,
because the sensor has been destroyed; the gauge or module must be replaced.
If you experience this failure mode quickly or frequently, you should consider a different vacuum gauge for
your application. Thermal vacuum gauges may be available with different sensor materials that are not as
reactive with your particular process gases. Or you may consider a different type of gauge, such as a
capacitance diaphragm gauge, which exposes only stainless steel or ceramic to the gases.
There is no material that is universally chemical resistant; your choice of vacuum gauge (as well as all
other vacuum components) should take into consideration the potential reactions between your process
gases and the materials of construction.
Consider what effect water vapor will have when combined with
your process gases because a finite amount of water will enter the chamber during venting to atmosphere.
B) Condensation, Coatings, and Particles
If the failure is due to an accumulation of material in the sensor, you may be able to restore your gauge or
module by cleaning. Contamination may be as simple as condensed water, or as difficult as solid particles.
Condensation
: Some gases (such as water vapor) can condense on sensor surfaces, forming a liquid
coating that changes the rate at which heat is removed from the sensor (which changes the calibration).
The sensor can often be restored simply by pumping on the gauge between process cycles. A dry N
2
purge will help speed up drying, or the gauge may be gently heated, provided temperature doesn't exceed
the specified limit (150
o
C with cables or electronics removed).
Coatings
: Some gases can condense on sensor surfaces, forming a solid coating, which again changes
the rate at which heat is removed from the sensor. Some of these coatings may be removed using an
appropriate solvent, following the procedure described below.
Particles
: Particles generated by the process may enter the gauge during the process cycle or during the
venting cycle. The result is interference with heat removal from the sensor. The cleaning procedure
described below may be able to remove particles from the gauge. However, particulate contamination is
the most difficult to remove as particles can become stubbornly trapped inside the gauge.